《制桶工培訓教程》
楊文亮 辛巧娟 編著
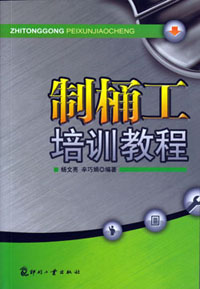
第六章 桶底頂沖壓和預卷成形
本章主要學習桶底頂沖壓成形、預卷邊,以及封閉器的成形加工等工序的技術要求、設備結構、操作維護、質量控制等方面的內容。重點掌握沖壓工藝的基本知識和設備的安全操作、維護保養等關鍵技術,掌握封閉箍式封閉器的生產方法和工藝要點。
第一節 桶底頂沖壓成形
沖壓加工在鋼桶生產中有著很重要的地位,它是在鋼桶生產中應用廣泛的一種加工工藝,鋼桶的桶底頂蓋和封閉器等大量零部件均采用冷沖壓方法加工。
一、沖壓加工的工藝要點
(1)沖壓生產應選擇合適的材料組織生產,不能滿足沖壓工藝要求的材料(延展性差、表面粗糙、薄厚不均等)不能投入生產。
(2)沖壓工藝設計時,應盡快選擇復合模具生產,以便提高生產效率和產品質量。
(3)鋼桶沖壓件的尺寸必須符合產品的工藝要求,避免形狀及尺寸精度超差,影響鋼桶整體質量。
(4)桶底頂拉深不允許有破損、裂紋等致命缺陷,以免造成廢品。
(5)沖壓件表面不應有皺紋、翹曲不平等形狀缺陷,以免影響產品美觀和影響后道工序的質量。
(6)沖裁邊緣不應有毛刺,以免對后道工序的設備造成過大磨損,影響設備壽命。
(7)沖壓件表面不應有機械劃傷,以免影響產品的表面質量。
二、沖壓成形方法及設備
1、沖壓成形的方法
沖壓成形是利用沖壓設備和沖模,使毛坯發生塑性變形或分離的加工方法。
所有沖壓方法,從工作原理上基本可歸納為分離和變形兩大基本工序。分離工序是使毛坯材料發生剪切破裂的沖壓工序,如落料、切斷、沖孔、切口等都屬于分離工序,在沖壓工藝上通常稱為沖裁;變形工序是使毛坯材料產生塑性變形的沖壓工序,如彎曲、拉深、翻邊等都屬于變形工序。在鋼桶生產中,多數沖壓加工工序都是多種沖壓工序組合在一起的復合工序,是利用復合模具來實現的,例如桶底頂的成形是沖裁和拉深相結合的工序。
沖裁是利用沖模使材料分離的一種沖壓工序。一般來說,沖裁工藝主要是指落料和沖孔工序。當沖裁以后,板料分成兩個部分,即落料部分和帶孔的部分。若沖裁的目的是為了制取一定外形的沖落部分,則該工序稱為落料;若為了制取內孔,則稱為沖孔。
拉深是利用模具使沖裁后得到的平面毛坯變成為開口的空心零件的沖壓工藝方法。拉深時,其凸模與凹模和沖裁時不同,它們的工作部分都沒有鋒利的刃口,而是做成一定的圓角半徑,并且其間的間隙也稍大于板料的厚度。在凸模的作用下,毛坯在凹模端面和壓邊圈之間的縫隙中變形,并被拉進凸模與凹之間的間隙里形成空間零件的直壁。
2、沖壓設備的工作原理和結構
沖壓設備通常有三種類型,即曲柄壓力機、螺旋壓力機和液壓機。鋼桶生產中最常用的是曲柄壓力機。曲柄壓力機是由機身、傳動系統、離合器、制動器、曲軸滑塊機構和下部拉伸墊等部件組成的。如圖6-1為曲柄壓力機的結構示意圖。
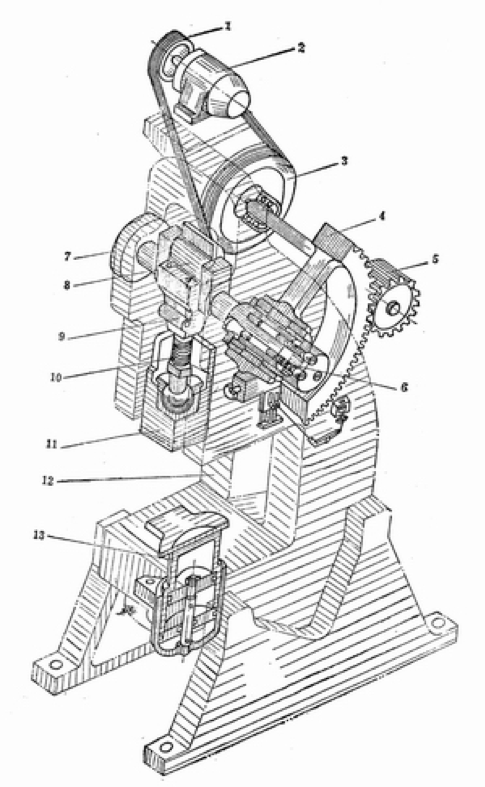
圖6-1 曲柄壓力機結構示意圖
1-小皮帶輪;2-電動機;3-飛輪;4-大齒輪;5-小齒輪;6-離合器;7-制動輪; 8-曲軸;9-邊桿;10-螺桿;11-滑塊;12-機身、13-位伸墊
曲柄壓力機工作時,電動機通過飛輪驅動曲軸旋轉,曲軸軸心線與其上的曲柄軸心線偏移一個偏心距r。連桿是連接曲柄和滑塊的零件。連桿用軸承與曲柄連接,連桿與滑塊的連接是通過球頭鉸接的。因此,曲軸旋轉時就使滑塊作上下的往復直線運動,這就是曲柄-連桿機構。這機構不但能使旋轉運動變成往復直線運動,還能起力的放大作用,即增力作用,使滑塊在最下位置時產生最大的壓力。
沖壓模具的上模固定在滑塊的下平面上,下模固定在工作臺板的平面上,因此,滑塊每上下運動一次就完成一次沖壓動作。雖然滑塊的往復直線運動是由曲柄的回轉運動促成的,曲柄也是勻速的轉動,但是滑塊在其行程中各點的速度是不一樣的。在滑塊向下行程時,滑塊在上死點的速度等于零。滑塊繼續向下運動,其速度就增加到某一個最大值,到達下死點時,其速度又重新降至零。在向上行程時和向下行程時一樣,滑塊的運動速度重復由零至最大再由最大降至零這個范圍內變化。
壓力機的飛輪有著比較特殊的作用。壓力機是一種間歇作功的機器,曲軸回轉一周滑塊進行一次沖壓工作,而實際工作行程僅占整個行程很小的一部分,在這很小的一段行程中卻要做很大的功,屬于沖擊負荷的性質。按照壓力機做功的要求,需要選定一個非常大的電機,但是這樣大的電機,只有在很短的工作時間里才滿負荷,而在大部分空程時間里負荷很小,這樣必造成很大的浪費,飛輪就是為了解決這一問題設置的。飛輪一般是裝在第一級齒輪傳動的高速軸上,這樣電動機的功率可以大為減少,因為當滑塊不動時,電動機帶動飛輪空轉,把電機供給的能量儲存起來。在沖壓制件的那一短暫時間內,主要靠飛輪釋放能量。釋放的方式是轉速降低。當制件沖壓完成之后,負荷減少,于是電機帶動飛輪加速旋轉,使它在沖壓下一個制件之前恢復到原來的轉速。這樣一來,沖壓制件所需的能量,也就是高峰負荷,便可以大大減少了。
離合器和制動器在壓力機上的作用是,在飛輪不停止旋轉的情況下,開動或停止壓力機。離合器和制動器一般是設置在飛輪軸上。當滑塊需要開動時,通過控制系統,使制動器脫開,離合器結合,電動機、飛輪的旋轉運動和能量通過離合器傳遞給傳動齒輪和滑塊。當需要停止滑塊時,通過控制系統使離合器脫開,制動器制動,將飛輪以下的運動件制動住,使壓力機停車。壓力機在不工作時離合器總是處在脫開狀態,而制動器則總是處于制動狀態。
滑塊機構包括滑塊體、閉合高度調節機構、平衡裝置、過載保護裝置、退料裝置等組成。滑塊本體是一個箱形結構,下平面上開有梯形槽或螺絲孔,用于固定沖模的上模板。閉合高度調節機構是為了適應不同閉合高度的模具能在一臺壓力機上安裝而設置的。平衡裝置是為了消除上模零件之間的應力和摩擦,減小振動和噪聲而設置的。退料裝置的作用是在滑塊向上回程時,把制件從上模中頂出來。過載保護裝置的作用是為了防預防壓力機在生產和調整的過程中,可能發生過載現象而損壞設備。
拉伸墊的作用有兩個方面,一是在拉深工序時把板料的邊緣壓緊,使制件在拉深過程中不致出現皺紋。二是在沖壓工序終于時把成形的制件從下模中頂出。拉伸墊有橡皮式和彈簧式的,也有純氣式的和液氣式的。
三、沖壓模具的結構
1、沖壓模具的基本結構
從沖模的結構來看,其主要零部件,依沖模類型不同而異。在鋼桶生產中,結構比較典型的沖壓模具有落料沖孔模、彎曲模、落料拉深模等,桶底頂沖壓成形多為落料拉深模。從工藝上分析,落料拉深模是由一道落料基本工序和一道拉深基本工序復合而成。如圖6-2為典型的落料拉深模結構示意圖。它主要由上下模板、導柱導套、凸凹模,退料裝置、擋料裝置、壓料裝置等組成。
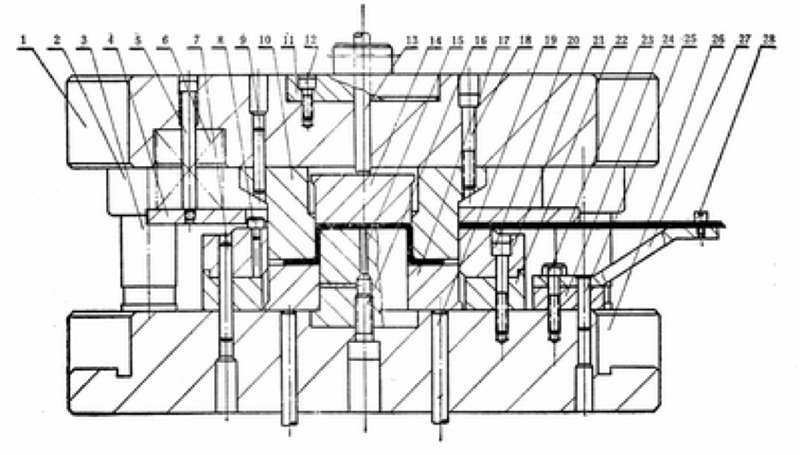
圖6-2 落料拉深模結構示意圖
1-上模板;2-襯套;3-導柱;4-退料板;5-退料板螺釘;6-彈簧;7、9、25-柱銷; 8-定料銷;10-凸凹模;11-模柄;12、16、18、20-內六角螺釘;13-推桿;14-頂出器; 15-凸模;17-壓料圈;19-托桿;21-凹模;22-固定板;23-外六角螺釘;24-墊板; 26-下模板;27-托料板;28-擋料螺釘
落料拉深模的工作過程是:放入的毛坯托在凹模21、壓料圈17和托料板27上。依靠定位銷8和擋料螺釘28定好位置。上模下行時,由退料板4將毛坯壓住,然后凸凹模10開始落料。此時壓料圈17借托桿19緊緊的壓住了毛坯,防止拉深時起皺。上模回程時,壓料圈17將制件從凸模15上頂出,卡在凸凹模10內,直到推桿13碰到壓力機的打料橫梁,推動頂出器14將拉深工件頂出。
組成模具的全部零件,根據其功用可以分成工藝結構零件和輔助結構零件兩大類。工藝結構零件直接參與完成工藝過程并和坯料直接發生作用,包括:工作零件(直接對毛坯進行加工的零件)、定位零件(用以確定加工中毛坯正確位置的零件)、壓料、卸料及出料零件。輔助結構零件不直接參與完成工藝過程,也不和坯料直接發生作用,只對模具完成工藝過程起保證作用或對模具的功能起完善的作用,它包括:導向零件(保證模具上下部分正確的相對位置)、固定零件(用以承裝模具零件或將模具安裝固定到壓力機上)、緊固及其他零件(連接緊固工藝零件與輔助零件)。
四、壓力機和沖模的使用與維護
1、壓力機的使用與維護
由于壓力機操作事故率較高,所以沖壓作業中,對沖壓設備的維護保養和操作,必須特別強調安全。
(1)操作工必須了解壓力機的型號、規格、性能及主要構造。了解模具對材料的要求,不應使用超過模具間隙厚度要求的材料。
(2)開機前,必須檢查設備。設備的安全防護裝置應齊全有效,離合器、制動器及其控制裝置應靈敏可靠,緊固件應不松動,電器的接地保護應可靠。
(3)操作前,必須準備好個人防護用品,工具準備齊全,機器周圍清理整潔,毛坯材料碼放整齊平穩。
(4)嚴禁在設備工作臺面和模具上放置量具及其他物件。
(5)當設備、模具和其他有關裝置發生故障時,必須停機檢查。當離開工作崗位時,應切斷電源。
(6)兩人以上同時操作時,要分工明確,配合協調,避免動作失誤。
(7)做好交接班工作。開機前應查看交班記錄,了解上一班設備的運行情況。按規定加油潤滑,經試車運轉正常后方可正式開機。
(8)規定用工具取放沖壓件的作業,不得用手直接操作。
(9)規定用單沖的作業,不得連沖。單沖時,沖一次踏一次,并隨即脫開腳踏板。
(10)工作期間,發生下列情況時應停機:
a.滑塊停點不準或停止后自動滑下。
b.設備發生不正常的響聲。
c.沖壓件或廢料卡在模具里。
d.模具上同時有一個以上毛坯。
e.模具上有廢料未被及時清除。
f.控制裝置失靈。
2、壓力機常見故障及維修
表6-1為壓力機常見故障及維修措施。
表6-1 壓力機常見故障及維修措施
序號 |
故障現象 |
原因分析 |
維修措施 |
1 |
軸承(連桿支承、曲軸支承)發熱 |
軸承配合間隙太小 |
重新調整配合間隙或刮研軸承 |
潤滑不良 |
檢查潤滑情況 |
2 |
連桿球頭處有撞擊聲 |
連桿環頭配合松動 |
應擰緊連桿球頭處的調整螺母,控制配合間隙到正常值 |
3 |
滑塊導軌發熱 |
潤滑不良 |
檢查潤滑情況,立即潤滑 |
導軌面拉毛 |
調整配合間隙到正常值 |
配合間隙太小 |
將拉毛的導軌面重新刮研修理 |
4 |
停機后滑塊自動下滑 |
滑塊導軌間隙太大 |
調整間隙 |
制動力不足 |
調整制動力 |
5 |
開機、停機時滑塊動作不靈,或停機時停止位置不準 |
離合器和制動器失錄 |
修理離合器和制動器 |
離離合器和制動器調整不適當 |
調整離合器和制動器 |
摩擦式離合器摩擦面有油污 |
清理摩擦面 |
易損件損壞 |
更換易損件 |
3、沖模的使用與維護
(1)操作工必須了解沖模的基本結構、沖模的特點和使用該沖模時應注意的事項。
(2)檢查原料毛坯是否符合工藝要求,不符合要求時,應及時更換。
(3)清理工作現場,布置好工位,將需要用的操作工具及安全防護裝置等都準備好,放到規定的位置上。
(4)檢查沖模有無缺損零件和緊固螺釘有無松動現象。給潤滑部位全面潤滑。
(5)開空車運行數次,檢查壓力機和沖模的運轉情況。正常后,開機正常工作。
(6)工作時,送料要平穩,定位要牢靠,不可用力沖擊定位部件。及時清除沖裁廢料,不可使異物落入沖模內。按規定在毛坯上擦抹潤滑液。
(7)毛坯、成品應輕拿輕放。注意退料板、壓料圈及頂出器等的運動情況。
(8)隨時觀察毛坯和沖壓件有無質量缺陷。發現異常現象時,應立即停車檢修,不得湊合使用。
(9)發生壓力機或沖模事故,必須保留現場,及時報告設備管理人員處理。
(10)工作結束后,應及時清除沖模中的廢料和污垢等,拭擦沖模。
(11)擦拭壓力機,清理工位,收拾好生產所用的工具。
五、桶底頂沖壓成形工藝質量控制
表6-2為桶底頂沖壓成形常見缺陷、原因分析及解決辦法。
表6-2 桶底頂沖壓成形常見缺陷及解決措施
序號 |
缺陷 |
原因分析 |
解決措施 |
1 |
皺紋 |
毛坯厚度不均或材料拉深性能差 |
更換材料 |
模具拉深間隙大 |
修理模具間隙或更換較厚的材料 |
壓料力太小 |
調整壓料力 |
壓料圈或凹模表面磨損嚴重 |
修理磨損的部件 |
毛坯上涂潤滑油過多 |
適量涂抹潤滑油 |
托料桿長短不一或壓料彈簧布置不均 |
調整托料桿或壓料彈簧 |
2 |
裂紋和斷裂 |
材料拉深性能不好 |
更換材料 |
材料厚度超差 |
更換材料 |
材料表面質量不好 |
清理材料表面或更換材料 |
沖模壓料力調整不當 |
調整壓料力 |
凹模或壓料圈局部磨損嚴重 |
修理磨損部件 |
沖模間隙過小 |
修理模具間隙 |
模具潤滑不及時 |
按規定及時潤滑 |
壓力機下滑塊端面與工作臺的平行度超差 |
調整或修理壓力機 |
3 |
形狀和尺寸精度超差 |
模具間隙過大或過小 |
調整模具間隙 |
行程調整不當 |
調整滑塊行程 |
4 |
拉深件表面擦傷 |
凹模材料不當或表面粗糙 |
更換凹模材料或修理表面 |
拉深間隙小 |
調整間隙或修理模具 |
毛坯表面質量不好 |
更換材料或加強潤滑 |
【返回目錄】