《制桶工培訓教程》
楊文亮 辛巧娟 編著
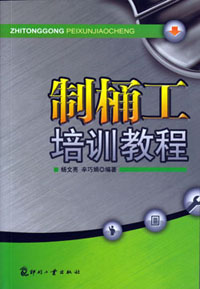
第四章 鋼桶的焊接
第二節 縫焊工序
縫焊是采用縫焊機對卷圓后的桶身縱縫進行焊接,目前常見的縫焊機有半自動縫焊機和全自動縫焊機,另一種就是介于半自動與全自動焊機之間的半自動改型焊機,雖然設備不同,但焊接要求是一樣的,主要要求焊縫要有足夠的強度和密封性。
一、縫焊工藝要點
以焊接200L鋼桶桶身為例,一般鋼材為08號優質碳素鋼板、熱軋板或A2、A3普通碳素鋼冷軋板,材料厚度多為1~1.2mm。
采用FN1-150-5型縫焊機進行縫焊時,焊接速度為1.5~3m/min;焊接電流為14~18kA,電極壓力為2~3kg/cm2,焊縫寬度為5.5+0.5mm。
工藝要求一般為:
(1)焊縫兩端應脫焊,但脫焊處長度不得超過3mm。
(2)焊縫兩端不允許出現拉長凸嘴。
(3)焊縫強度不得低于原材料的抗拉強度。
(4)焊縫要平直,不得偏斜或脫出搭邊,無開焊或裂邊。
(5)焊縫外觀要均勻,不得出現起泡、飛剌、燒黑或起皮現象。
(6)縫焊搭邊尺寸應符合工藝要求。
二、縫焊機原理及結構
1、縫焊機的工作原理和特點
縫焊機的焊接原理與點焊機基本相同,即將準備好的桶身工件置于兩極之間加壓,并對焊接處通以電流,利用桶件電阻產生的熱量加熱并形成局部融化(或達到塑性狀態),斷電后,在壓力繼續作用下,形成牢固接頭,這是電阻焊的一種型式。
與點焊不同的是,縫焊時,電極是滾盤型式的,因電極輪不斷轉動,電極輪與板件相對位置不斷變化,形成了一個個重疊的焊點。按核心熔化重疊度不同,可以分為滾點焊和氣密縫焊。縫焊一般采用交流脈沖電流或調幅電流,也可用高頻或直流電流。鋼桶生產中以氣密縫焊占多數,組成氣密縫焊的各個焊點的形成過程,同樣存在加壓、加熱熔化和冷卻結晶三個階段,但與點焊過程有兩點最主要的區別,其一是傳遞壓力、通電加熱的電極輪不斷轉動變換焊接位置,所以焊縫密封性能與焊接速度關系較大;其二是不可避免的分流使熔化區尺寸減小。
2、縫焊機的結構
(1)半自動縫焊機
國內大多數制桶企業都是采用通用型半自動縫焊機進行鋼桶的桶身焊接,雖然各企業都為了提高生產效率和質量,對半自動縫焊機進行了不同程度的改造,但主要結構并沒有太大的改變。
半自動縫焊機一般由機身、焊接變壓器、焊輪加壓裝置、氣路系統、上下焊頭系統、傳動系統、冷卻水系統、控制系統等組成。如圖4-2所示為通用半自動縫焊機結構示意圖。

圖4-2 半自動縫焊機結構示意圖
1-變壓器;2-加壓系統;3-上下電極輪;4-焊接回路;5-機身;6-傳動系統;7-控制系統
半自動縫焊機的減速系統一般采用可調速的直流電動機,也有采用交流電動機,通過齒輪減速箱由剛性連軸器帶動摩擦輪支架的錐齒輪,再由錐齒輪傳動驅動一對正齒輪轉動,正齒輪再帶動摩擦輪。由彈簧壓緊在電極焊輪上的磨擦輪使焊輪旋轉。這種傳動使得電極輪無論直徑如何變化都能獲得相等的線速度。
半自動縫焊機的氣動加壓系統屬固定行程的氣缸裝置,只有一個活塞,但活塞的行程由氣缸活塞桿另一端的螺桿確定。另外,氣壓系統中還裝有壓力繼電器,此裝置是保證氣路達到一定壓力值時才能接通焊接電流。此壓力須根據焊接需要加以調節。
半自動縫焊機的導電系統一般采用滑動接觸導電方式,導電間隙內用石墨、蓖麻油或錠子油保證其潤滑導電。也有用銀合金斜面滑塊作導電塊的,此方法接觸面好,磨擦小,對于型面接觸不良處,能自動補償,接觸面能達到80%以上。
縫焊機的電極是電極輪。電極輪的緣面形狀、寬度、直徑、冷卻方式和安裝方法均與焊接質量有直接關系。
(2)全自動縫焊機簡介
全自動縫焊機與半自動縫焊機的原理基本相同,不同的是全自動縫焊機實現了自動送料、卷圓、搭邊定位和焊接。其桶身周向定位機構、桶身導向機構和桶身推進機構是自動縫焊機完成自動送料的三大關鍵裝置。有了這三大機構,不但實現了進出料自動化,而且省去了點焊定位這一環節,大大簡化了鋼桶焊接工藝。此外,全自動縫焊機還將鋼板卷圓、桶身輸送、直縫焊接、焊縫滾壓集為一體,真正實現了從平直鋼板進入到縫焊完成及桶身送出的自動化生產。
全自動縫焊機主要由機身、自動進料系統、桶身卷圓系統、輸送系統、尋縫推進系統、定位電極系統、滾壓卸料系統、氣動系統、冷卻系統、電源及控制系統等組成。如圖4-2為全自動縫焊機外型結構示意圖。
全自動縫焊機的工藝流程分為自動進料、卷圓、待焊、焊接、滾壓焊縫、卸料等六個工位。進料的推進方向與卷圓成形軸線垂直;卷圓、待焊、焊接、焊縫壓平、卸料各工位上的零件軸線均同軸或平行。

圖4-3 全自動縫焊機結構示意圖
1-機身;2-加壓系統;3-滾壓系統;4-焊輪系統;5-傳動系統; 6-推進系統;7-電源控制系統;8-卷圓系統;9-定位系統
自動進料系統由自動上料機構、驅動機構、抽真空裝置和兩段輸送滾道等組成。鋼板毛坯由叉車運送到自動上料機構的輥筒平臺上,自動上料機構即可把鋼板自動吸送到卷圓機構中,并開始工作循環。
桶身料毛坯在三輥卷圓機構中被加工成圓筒狀。桶的直徑可以通過調整活動輥與固定輥及壓緊輥的距離相應改變。
輸送機構把圓筒狀的工件,由撥爪推至待焊工位短暫停留,待焊接工位的工件焊接完畢后,推進部件可將工件再次從待焊工位推至焊接工位,進入焊接狀態。隨后快速退回原位,等待下一個循環。
上電極輪安裝在上電極部件的前端,其后端為懸臂支架。下電極氣缸通過下支座對上電極輪施加電極壓力。上、下電極輪中間均裝有電極冷卻管路。
焊完的焊縫隨即經過兩組滾壓輪的滾壓,提高熔縫熔核的搭接量,并使焊縫外形表面平整光滑。焊接完畢的工件通過卸料部件的輸送帶及滾道,送到卸料位置,然后,卸料氣缸將工件頂出,完成一個工件的焊接循環。
底座部件上的龍門框配有三個定型壓輪組,可與定形滑道一同保證施焊工件的直徑和搭接量。縫焊機的進料、電極輪軸向移動、產生電極壓力、卸料等運動均以壓縮空氣作動力源。潤滑系統分導電脂潤滑部分和普通潤滑脂潤滑部分,兩部分分別用各自的干油泵自動供給潤滑脂。
控制部分采用PLC編程控制器和人機界面組成,整個操作系統由最新技術觸摸屏式控制,全中文顯示,直接顯示故障原因,維修方便快捷。
三、縫焊機的操作與維護
這里我們以國內常用的半自動縫焊機為主進行說明。全自動焊機各種機型區別較大,應以焊機使用說明書為準進行操作和維護。
1、縫焊機的操作規程
(1)先打開氣路系統,用調壓閥確定電極壓力,在無焊接電流的情況下調好壓力繼電器。
(2)開機前,檢查設備的傳動件、緊固件是否正常,安全防護裝置是否完好,氣路、水路是否暢通,特別是焊接變壓器更要注意。確保焊機的控制器可靠接地。一切正常后,按規定對設備進行全面潤滑。
(3)接入電源,將控制箱上電源控制開關轉到“通”位置,并接通可控硅冷卻水。
(4)選擇好焊接變壓器級數,將機身上控制電路、壓力、電流開關置“通”位置,此時踩腳踏開關上面的開關焊接就開始,踩腳踏開關踏板焊接就結束。
(5)根據所縫焊的材料厚度、材質,調定焊接電流、電壓、壓力等參數。運行過程中,應注意觀察冷卻水量是否充足,絕緣是否良好,發現異常,應立即停機檢修。
(6)先不帶電試運行,將電流開關置于“斷”位置,如需修整焊輪,上電極置于上升位置,則壓力開關置于“斷”位置,上下電極焊輪空轉。
(7)工作時,應在接通水路和氣路后方可接通電源。焊機溫度不得超過規定溫度(75℃)。
(8)工作時焊機和控制箱的門必須關閉。在電源和氣源未切斷以前,禁止在焊機上進行任何安裝檢修工作。
(9)工作完畢后,切斷電源、氣源,等設備冷卻后,切斷水源,并清理設備及現場。
2、縫焊機的調試與使用
(1)焊接壓力調節:焊接壓力的調節是通過調節調壓閥來實現,并由氣壓表指示其氣壓,焊接壓力須視焊件的材料與厚度作相應調節,以免因壓力不夠造成飛濺或因壓力過大造成焊接不良。
(2)電極焊輪下壓速度調節:將功能選擇旋扭置于電極調整位置,踏動、松開腳踏開關,焊輪將上下運動,此時,根據上焊輪上升與下降速度調節限流閥及氣缸座處的緩沖調節鈕,直至焊輪上下速度適當。
(3)上下焊輪間距調節:上下焊輪間應小于焊輪的最大工作行程,調節上下焊輪之間距至適當(約25mm)。注意在以上過程中,不要踏動腳踏開關,以免造成誤通電而燒毀焊輪,發生危險。
(4)焊接速度調節:可根據不同材料,厚度的桶件調節電動機轉速,電機轉速由電機控制器控制,速度控制參數可調定范圍一般為1~60,設定參數為60時為最大。
(5)焊機按程序動作:
a.根據桶身的材料及厚度,選擇適當的規范(可參照《鋼桶制造技術》或焊機說明書),分別調節程序1、2、3十個功能項的參數值;
b.將功能選擇旋鈕置于運行位置,踏動腳踏開關,焊機按程序動作,但沒有焊接電流通過;
c.程序1、2、3各動作一次。注意桶身的焊接質量與焊接電流、焊接時間、焊接壓力等焊接工藝規范有著直接關系,因此在焊接時應根據具體情況作相應調整,焊接電流與焊輪壓力的調節應同步進行。
(6)焊機正常焊接:
a.動作完全正常之后,將功能選擇旋鈕置于焊接位置,就可以進行焊接;
b.踏動腳踏開關一次,焊機焊接一次;
c.需進行循環焊接時,將休止時間設置成大于1的數值(休止時間的數值根據實際情況設定),一直踏下腳踏開關,則焊接可進行多次,直至松開腳踏開關(這種循環可配合自動送料機或機械)。
(7)電極焊輪的修整:電極焊輪必須保持光潔,使用一定時期后電極焊輪出現磨損,可用細銼刀或砂紙修平或卸下在車床上加工平整。
(8)每天工作結束后,應依次進行以下操作,保證焊機長期安全運行。
a.關掉總機電源開關;
b.按動濾水器下的排水按鈕,排出貯存在里面的水;
c.關掉氣源,如果油霧器中的潤滑油太少,低于最低刻度,應向油霧器中添加潤滑油(應使用適于氣缸使用的潤滑油);
d.關掉冷卻水水源。注意在冬天,環境溫度低于0℃時,需將冷卻水管中的水排掉并用壓縮空氣吹去冷卻水管內的剩水,以免水管凍裂。
3、焊機的維護和保養
在縫焊機維護保養時,必須關掉總電源,以免發生危險。
(1)日常保養:這是保證焊機正常運行,延長使用期限的重要環節。
a.焊機須在干燥且少灰塵的環境中工作,切忌腐蝕性氣體的侵蝕;
b.注意冷卻水的流通情況;
c.注意保持焊機的清潔;
d.檢查各部位的接觸與絕緣情況;
e.焊機使用完畢后切斷電源且停止壓縮空氣及冷卻水的供應;
f.為確保良好的焊接效果,在修整氧化和磨損的焊輪表面時,應使用優質銼刀和砂紙。
(2)定期維護檢查
a.每天用機后排掉過濾器中的水;
b.每周往油霧器中注入一定量的潤滑油,選用純度較高的潤滑油;
c.定期檢查機械部分配合是否正常,有無漏水;
d.檢查連接是否緊固,特別是電氣連接處需定期緊固;
e.檢查水路管道有否堵塞,為防止水路堵塞,每月將壓縮空氣通入冷卻管清理水路;
f.檢查絕緣是否有損壞,氣管和水管是否老化。
四、縫焊質量的控制
1、焊接質量的影響因素
影響縫焊質量的因素很多,一般可歸納為設計、工藝和使用三類。當搭邊設計不合理時或材料不合焊接要求時,就會使焊接不易達到質量標準的要求;工藝參數選擇不當,電極或夾具不合要求,設備工作不正常,材料表面質量差,以及搭接不良等,都直接影響焊接質量;焊縫的質量要求是否正確,同樣會對縫焊質量有影響,當鋼桶不在規定技術條件下使用時,則會因環境的惡化而使焊縫性能迅速降低。由于焊接過程機械化、自動化程度較高,故縫焊質量同設備的穩定性及調整水平的關系更為密切。圖4-4列出了對焊接質量影響較大的幾個因素及相互之間的關系。
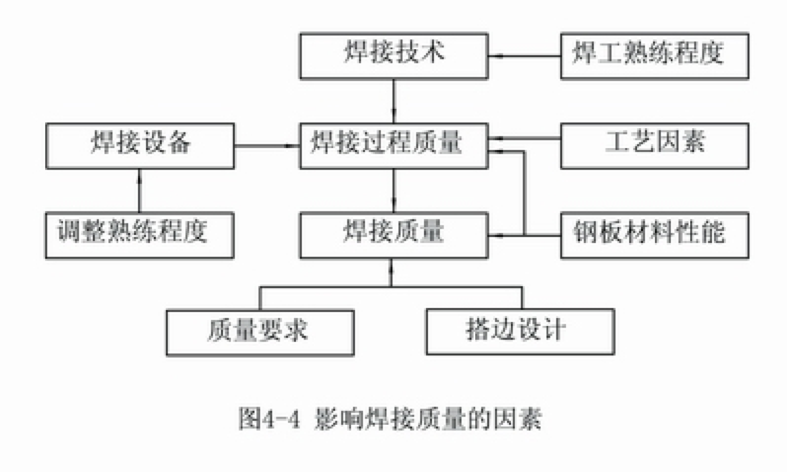
2、常見焊接缺陷及解決措施
如表4-2所示,為鋼桶縫焊常見缺陷及解決措施。
表4-2 鋼桶縫焊常見缺陷及解決措施
序號 |
缺陷 |
原因 |
改進措施 |
1 |
焊縫表面壓痕形狀及波紋度不均勻 |
焊輪工作表面形狀不正確或磨損不均勻 |
修整焊輪 |
焊接時,焊件與焊輪傾斜 |
檢查機頭剛度,預調焊輪傾角 |
焊速過快 |
調整焊速 |
2 |
焊點壓坑過深及表面過熱 |
通電時間過長 |
調整規范 |
電極壓力不足 |
改變焊輪端面錐角角度 |
電流過大 |
改善冷卻條件 |
3 |
表面局部燒穿或金屬強烈外溢 |
焊縫搭邊及電極表面不干凈,污物多 |
清理板料及電極表面 |
焊輪壓力不足,或焊輪與電極間未真正接觸 |
提高焊輪壓力,更換磨損過度的焊輪 |
焊輪接觸表面形狀不正確 |
修整焊輪 |
焊整過快,焊輪過熱 |
改善冷卻條件 |
4 |
焊縫表面發黑,包覆層破壞 |
桶身搭邊及焊輪表面清理不良 |
注意及時清理表面 |
焊輪壓力不足 |
調整規范 |
通電時間過長,電流過大 |
降低焊輪或改善冷卻條件 |
5 |
焊縫邊緣壓潰或開裂 |
邊距過小,焊輪未對中 |
調整規范 |
電流過大,時間過長 |
改進搭邊設計 |
大量焊后飛濺 |
注意焊輪安裝及桶身放平 |
6 |
焊縫脫開 |
搭邊不良,焊接時搭邊有錯位 |
注意定位,調整板間間隙。 |
7 |
焊縫發脆 |
通電時間短,焊接循環不合理 |
調整規范 |
改變熱循環形式 |
8 |
焊縫不氣密 |
焊接規范不穩定 |
調整設備與控制裝置 |
定位點焊燒穿 |
調整點焊,改善點焊質量 |
上、下焊輪直徑相差過大 |
適當改善兩焊輪直徑或散熱條件 |
復習題
1、點焊和縫焊的基本原理是什么?點焊機和縫焊機的基本結構是由哪些部分組成的?
2、縫焊機的工藝參數有哪些?如何調整這些參數?
3、全自動縫焊機與半自動縫焊機有哪些區別?優點是什么?
4、縫焊機的調試和使用應注意哪些環節?
5、如何進行縫焊機的維護和保養?
6、焊接質量與哪些因素有關?
【返回目錄】