《鋼桶制造技術》
楊文亮 辛巧娟 編著
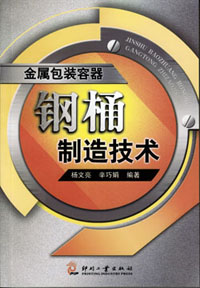
第三章 鋼桶制造技術基礎
第三節 鋼桶制造工藝流程
制桶的工藝過程較為復雜,一般是將各部件加工完成后再進行組裝。鋼桶一般由桶身、桶底、桶頂、封閉器等四大部分組成。
一、200升標準鋼桶制造工藝流程
以200升閉口鋼桶為例,其制造的工序過程如圖3-1所示。其它鋼桶的工藝過程與之大致相似,由于所用材料不同,設備不同,工藝過程也有差異。
流程圖既包括了平板鋼材為原料的鋼桶生產工藝,也包括了卷板為原料的鋼桶生產工藝,同時還包括了采用半自動縫焊機的工藝流程與采用自動縫焊機的工藝流程,而且還包括了清洗磷化處理與內噴涂的工藝流程。
采用卷板生產鋼桶需采用開卷、校平、定尺下料的工藝流程,這是目前國內最為先進的下料生產工藝。對于采用平板料生產的企業,“卷板開卷校平下料”工序就只是下料這一項。
采用半自動縫焊機生產桶身時,需要進行磨邊、卷圓、點焊定位、縫焊幾個工序;而采用全自動縫焊機時,這些工序都合成為縫焊,即圖中虛線部分的流程。
桶身及桶底頂的清洗磷化工序,實際包括了除油、清洗、除銹、清洗、磷化、烘干幾個工序,這是一條清洗生產線。對于不同的企業,不同的用戶要求,其中的某一部分或全部都可以省略。
內涂烘干工序包括了桶身內涂、桶底頂內涂、涂膜烘干幾道工序,在某些企業中這也是一條生產線。圖中所示內涂烘干工序位置是閉口鋼桶內涂的工藝,對于開口鋼桶來說,目前內涂可以在桶底與桶身卷邊封口后與外涂同時進行。
螺圈和螺塞的生產工藝流程中,其實G2和G3/4的封閉器稍有不同,在G3/4封閉器螺圈和螺塞的實際生產中,需分別加上二次拉深與精整兩個環節。
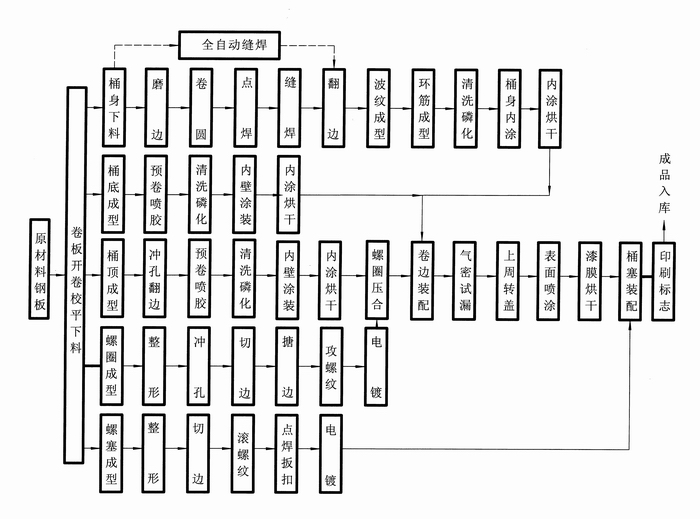
圖3-1 閉口鋼桶的一般工藝流程圖
二、200升標準鋼桶制造工藝概述
鋼桶生產所采用的工藝手段涉及面很廣,基本上可分為三大類,即機械加工工藝、焊接工藝和涂裝工藝。
1.鋼桶生產的機械加工工藝
從機械加工成形方式來分類,鋼桶制造的加工工藝可分為兩類,一類是金屬切削加工工藝;另一類是無切削加工工藝。
金屬切削加工工藝,如板材磨邊的磨削、螺圈成形的擴孔車削和螺紋攻絲等。這類加工工藝與普通的切削加工相比,本質上是完全相同的。只是為了提高加工速度,鋼桶制造生產中都有自己的專用設備,如磨邊機、專用車床、滾絲機和攻絲機等。從而使它們跟鋼桶制造的節拍和達到鋼桶制造的工藝要求。
無切削加工工藝在鋼桶制造生產中應用更為廣泛,如板材的裁剪、桶底頂與封閉器的沖壓、桶身成形與卷邊的壓力加工方式,以及桶塞螺紋的滾軋成形與卷圓的滾壓成形均屬于無切削加工。其中沖壓工藝應用最多,幾乎應用了包括沖裁、拉深、彎曲、成形在內的全部沖壓工藝。回轉旋壓成形工藝是鋼桶制造特有的加工工藝,只適用于如鋼桶的桶身生產。加工時,鋼桶夾持在胎具上并隨胎具轉動,用滾輪作為加工工具使其一部分彎曲(翻邊)、漲形(脹筋)、壓形(波紋成形)、卷邊(卷封裝配)。其中,漲筋加工,目前常采用的是冷擠壓工藝,近幾年來翻邊也多采用冷擠壓加工,即加工時鋼桶并不旋轉,也就是常說的模具翻邊。
鋼桶成型加工工序主要是翻邊、漲筋、壓波紋和卷邊裝配工藝,有的企業采用“三合一”生產設備,在一道工序上同時進行了翻邊、漲筋和壓波紋加工。這些屬于中段設備的制桶機械是鋼桶生產的專用設備,目前在國內有各式各樣的中段設備。按傳動方式分,有液壓設備、機械設備、手動設備、氣動設備等;按鋼桶在生產線上的位置分,有立式和臥式兩種;按生產自動化程度分,可分為全自動設備、半自動設備和手動設備等。
2.焊接工藝
鋼桶采用的焊接工藝也可分為兩種:一種是縫焊工藝,用于桶身直縫的焊接;另一種為點焊或凸焊工藝,用于桶身縫焊前的搭邊定位以及封閉器等的焊接。這兩種焊接方法均屬于電阻焊焊接。
縫焊是采用電極輪作為電極,焊接可連續加工。桶身搭邊定位是采用單純的點焊,電極是普通的電極頭,每個焊點加工一次,一般一個桶身需要2~5點焊接。而在鋼桶封閉器的生產中,一般是先在零件上加工若干個凸點,再采用專用的成形電極頭作為電極,即相當于若干點一次點焊加工成形,通常這種焊接叫做凸焊。
采用全自動縫焊機焊接桶身時,不需要點焊定位,也不需要磨邊、卷圓,裁好的桶身料只要送進機器,都會自動完成卷圓和縫焊加工。
3.涂裝工藝
涂裝工藝是保證鋼桶表面質量,增強鋼桶搞腐蝕能力的一種重要工藝手段。目前,國內采用最廣泛的涂裝工藝是油漆涂裝工藝。由于噴涂方式不同,可分為空氣噴涂、靜電噴涂和高壓無氣噴涂等幾類。
隨著鋼桶制造技術的發展,新的涂裝工藝已逐步加以應用,如粉末噴涂工藝、電泳涂裝工藝以及金屬噴涂等新工藝。鋼桶鋼板采用鍍鋅和鐵塑板或預涂鋼板后,鋼桶制造工藝會大大簡化,涂裝工藝也不再是制桶工藝中必需的重要環節。當然,這些新工藝新材料雖然在防腐蝕效果上比油漆更勝一籌,但成本也高很多,工藝、技術也復雜得多,因而,現在大量采用的還是油漆涂裝工藝。
為了保證涂裝質量,提高漆膜附著力,在涂裝前進行除油、除銹、磷化、清洗、烘干是必要的工藝。對于表面要求不高的鋼桶產品,多數企業采用人工擦桶的辦法,可以有效的降低成本。
作為涂裝的最后一道工序,應該是標志的印刷,以前鋼桶的標志是采用空氣噴涂法,利用鏤空的標志版進行噴字。現在市場對鋼桶的外表質量要求越來越高,已經開始采用絲網印刷和熱轉印技術進行標志的印刷。
三、其他類型鋼桶的工藝流程簡介
1.桶身制造工藝
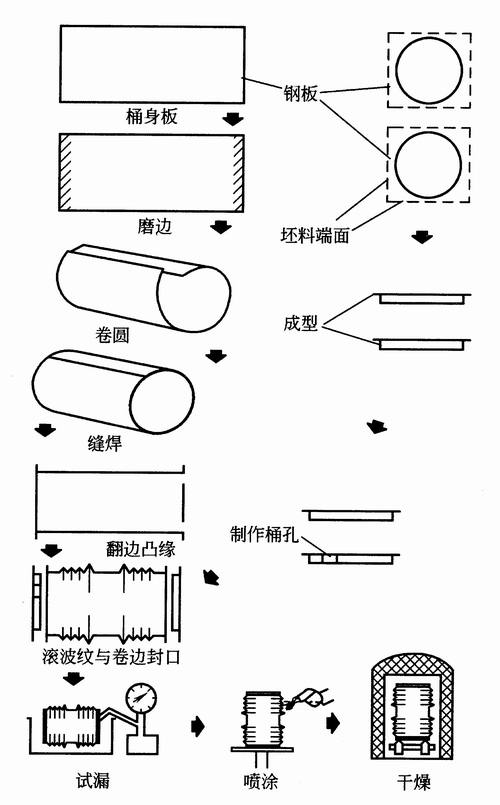
圖3-2 圓柱形閉口鋼桶工序過程示意圖
(1)圓柱形閉口鋼桶:圓柱形閉口鋼桶的制造工藝過程如圖3-2所示。其桶身制造的工藝流程如下:
原材料→剪切→磨邊→卷圓→點焊→縫焊→翻邊→滾波紋→脹環筋→桶身成形
選用合適的原材料,根據桶身設計尺寸剪切下料,將剪切好的桶身板料縫焊搭邊進行磨削;在卷板機上將桶身板材卷成圓筒形,用點焊機將已卷圓的桶身進行搭接點焊定位,再用縫焊機將桶身縱向搭邊焊接,形成一條氣密性的焊縫;在翻邊機上將縫焊后的桶身兩端邊緣向外翻出,以便卷封裝配;在波紋機上將桶身進行滾壓,使桶身獲得波紋式加強筋;在脹筋機上將桶身脹出環形筋,從而完成桶身的加工。
(2)圓柱形開口鋼桶
(a)桶口卷管:圓柱形開口鋼桶桶身的加工工藝和閉口鋼桶桶身的制造工藝基本相同,只多了一道桶口卷管工序,可在卷管機上完成,也可以在模具翻邊機上直接完成,也可以在卷封裝配機上完成。桶身翻邊時,桶口一端的翻邊寬度應比桶底端寬些。開口桶桶口卷管示意如圖3-3所示,桶身繞其軸線旋轉時,卷管壓滾向桶身上端的翻邊作徑向推動,形成桶口卷管。這種工藝方法一般是在卷封裝配機上進行的,只要把原先卷封桶頂的滾輪更換成卷管滾輪即可,并將桶頂壓盤改為開口桶桶口壓盤,在桶底卷封的同時進行桶口卷管。
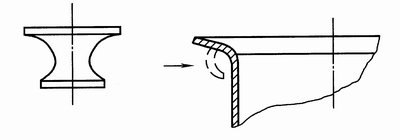
圖3-3 開口鋼桶桶口卷管示意圖
(b)桶口縮頸:開口縮頸桶的桶身制造又多了一道桶身縮頸工序。作業時,是在縮頸機上通過縮頸模具將桶口收縮變形,使桶口局部直徑變小。當縮頸變形較大時,可將縮頸成型分兩次完成,以免薄壁桶身在縮頸中失穩起皺。
(3)鋼提桶:圓柱形鋼提桶桶身的制造工藝與圓柱形閉口鋼桶桶身的生產工藝相類似。圖3-4所示為錐形鋼提桶生產工藝流程,圖中的底部翻邊前各道工序是鋼提桶桶身的生產工藝流程。
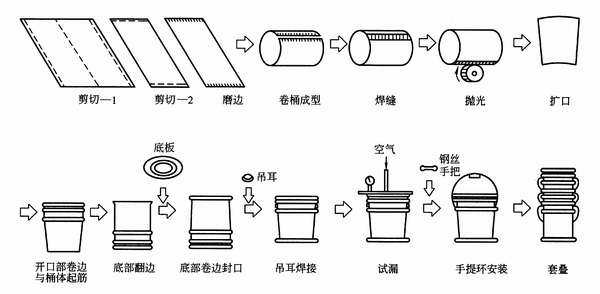
圖3-4 鋼提桶生產工藝流程
(4)異形桶:異形桶的桶身可用機械沖壓方法,通過模具使桶身折成所需的形狀,桶身的轉折處一般有小圓弧過渡,以保證桶身折方時不產生裂口等缺陷。為了不影響縫焊和卷封裝配,桶身上的加強筋需在桶身板折方前用壓力機模壓成形,且與縫焊搭邊處要空有一段距離。
脹形法是制造異形桶常用的方法,先將桶身做成圓筒狀,再放在脹型機上成型。
脹形機按脹型運動的轉動方式分為凸輪式、錐體式、楔塊式等。凸輪式脹形機的工作原理如圖3-5所示,在彈簧的作用下兩脹塊中心的滾子始終與凸輪邊緣接觸,圖3-5(a)中凸輪的位置使兩脹塊的距離最小,此時可將桶身套入。轉動凸輪,使兩脹塊向外移動,轉至圖3-5(b)的位置時,圓形桶身被脹為異形桶身。
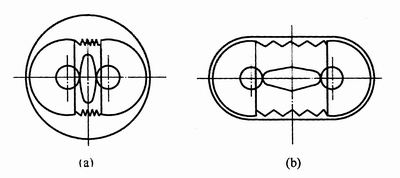
圖3-4 凸輪式脹形機工作原理
錐體式和楔塊式脹形機的脹形動作分別靠錐體的移動和楔塊與脹塊斜面間的相對運動來驅動兩脹塊的張開實現異形桶身的脹形。凸輪式脹形機是靠凸輪的轉動扭矩產生脹形力,和錐體式、楔塊式脹形機相比,脹形力小,一般用于薄壁小桶的脹形。
脹形法很容易獲得錐體桶身上的波紋且工藝簡單,主要問題是回彈性大,不易定型。為了克服回彈,可采取多次脹形或使桶壁脹形變形加大的方法使桶身變形硬化以減小回彈,但桶身板下料長度比理論計算值要大,以彌補變形產生的誤差。
2.桶底制造工藝
桶底的生產制造較簡單,制造工藝流程如下:
剪板→落料拉深→預卷噴膠
首先根據桶底設計尺寸和原料尺寸確定排樣方案,然后在剪切機上將原料切成桶底毛坯,再將毛坯送入沖床,利用模具同時完成落料和拉深而得到桶底。在預卷機上對桶底進行預卷邊,并在卷邊部位噴上密封膠。
異形桶底在沖壓拉深作業中,受力變形過程復雜,一般一次落料拉深后還要增加修邊工序,用修邊模具在沖床上再次落料,使桶底獲得準確的邊緣尺寸。
3.桶頂制造工藝
閉口桶桶頂的制造工藝和桶底基本相同,工藝流程如下:
剪板→落料拉深→桶口沖孔翻邊→鎖裝封閉器→壓印標記→預卷噴膠
落料拉深后,在復合模具中將桶頂進行沖孔和翻邊,然后將螺圈套上襯墊,放入桶頂孔內,在沖床上通過模具卷邊,使螺圈和桶頂壓緊鎖合在一起,同時在桶頂平面上壓印標記(商檢號、廠標、生產日期等),再預卷噴膠后即可進行卷封裝配。
開口桶桶頂即是桶蓋,其制造工藝流程如下:
剪板→落料拉深→圓邊→注膠→壓印標記
圓邊工序是將桶蓋周圍凸起的邊緣向下變曲,加工成形后的開口桶蓋結構形狀如圖3-6所示。有的開口桶對密封性有特殊要求,所以在邊緣卷槽里需要注入密封膠,加熱發泡后成為膠墊,裝配后在桶蓋和桶口之間起密封作用。
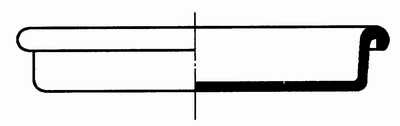
圖3-6 開口桶桶蓋的結構形狀
【返回目錄】