《鋼桶制造技術》
楊文亮 辛巧娟 編著
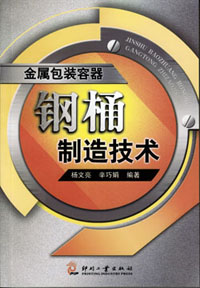
第十四章 鋼桶的涂裝工藝
第二節 涂裝前表面預處理
要保證鋼桶涂層經久耐用,符合使用要求,充分發揮涂料的保護和裝飾作用,除涂料本身的質量外,其施工也是一個很重要的關鍵因素。鋼桶的表面處理是涂裝前的準備工作,表面處理關系著涂層的附著力和使用壽命,直接影響涂裝質量,因此,這道工序應受到重視。
表面準備工序,主要是清除鋼桶表面的油脂、銹蝕、有機物污物和塵土等,以改善鋼桶表面狀態。表面處理的目的,主要有以下三個方面:
1.增強涂膜對鋼桶表面的附著力。鋼桶表面上存在著塵埃、油垢、水、氧化層、鐵銹或預卷噴上的膠等,會影響涂膜與鋼桶表面的附著力。表面處理的目的,就是要除凈這些雜質,使表面平整且有一定的粗糙度,以提高涂膜的附著力。
2.為涂膜的美觀平整準備條件。鋼桶表面的粗糙度,有時受到鋼板上的污物影響,顯得太粗糙而不夠平整,表面處理可使鋼桶表面平整。
3.增加表面抗腐蝕能力。鋼桶表面有水汽存在時,形成微電池,它是鋼桶腐蝕的主要因素,鐵銹的比容積大,存在于涂膜和鋼板之間,就會導致涂膜耐水性降低,使表面很快銹蝕。如果用表面處理的方法,去掉鐵銹,就能提高耐水性。
涂裝前表面處理的程序是:先除油,其次去銹,根據使用要求,還可以進行機械處理和化學處理。
一、鋼桶表面的除油方法
脫除油脂主要是利用溶解、皂化、乳化作用將鋼桶表面油污去掉。常用的除油方法如下。
1.有機溶劑除油
對于沒有設備或生產批量小的企業,人工除油常用有機溶劑和人工擦拭相結合的辦法除油。要求所用的溶劑溶解力強、不易著火、毒性小、便于操作、揮發性慢。實際上所用的溶劑很難完全符合以上要求。常用的溶劑有:汽油、石油溶劑、松節油、甲苯、二甲苯、二氯乙烷、三氯乙烷、四氯乙烷等。
操作時,人工用抹布蘸取有機溶劑,在鋼桶表面進行擦拭,一般來說,經過兩遍擦拭即可達到除油要求,待表面有機溶劑揮發掉后再進行涂裝即可。
2.堿液除油
堿液除油主要借助堿的化學作用來清除鋼桶表面的油脂及輕微銹蝕,達到表面凈化的目的。堿液的組成有氫氧化鈉、碳酸鈉、磷酸三鈉、碳酸鉀、硅酸鈉(水玻璃)、肥皂等。在這些組分中氫氧化鈉起皂化作用、洗滌清理作用,磷酸三鈉起軟化水的作用,碳酸鈉主要是起調節pH值作用,硅酸鈉加強潤濕和乳化作用等。
這種方法在國內制桶行業中應用廣泛。堿液除油在施工中有兩種方法,一是將鋼桶浸入堿液中除油,二是采用噴淋的方法除油。后者應用較多,效果也較好,適合于大批量流水線生產。
3.乳化除油
乳化除油是利用能促使兩種互不相溶的液體(如水和油),形成穩定乳濁液的物質(乳化劑),來除去鋼桶表面上的油脂及其它污物,達到除油的目的。它能在室溫下進行,溫度對其清洗效果影響不大,除油比堿液除油效率高,它可使油脂在乳化劑中被溶解除掉,水溶性的污物則在水中得到溶解被清除。
乳化除油可采用噴淋或浸漬的方式進行。一般以噴淋的方式除油效果較好,但浸漬式較簡單,各有所長。
二、鋼桶表面的除銹方法
1.機械處理法
機械處理法較為簡單,最古老的方法是手工處理,即利用鋼刷、砂布、砂紙、布等工具手工除銹,工作效率極低,質量也不好。另一種方法是用擦桶機進行擦桶,效果較好。如圖14-1和圖14-2所示為鋼桶內外表面擦桶機示意圖。
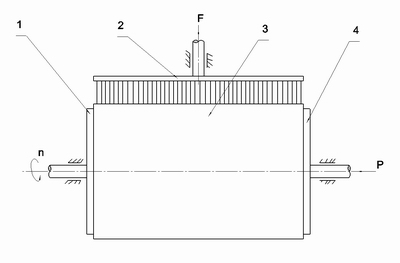
1—轉盤;2—鋼刷、布刷;3—鋼桶;4—壓盤
圖14-1 外表面擦桶機

1—壓盤;2—鋼桶;3—鋼刷
圖14-2 內表面擦桶機
外表面擦桶機由轉盤、壓盤、鋼刷、布刷等組成。鋼桶由轉盤和壓盤夾緊,并隨著轉盤轉動,兩排刷緊貼在鋼桶表面進行擦桶。
內表面擦桶機由壓盤和鋼刷等組成,內轉子三排鋼刷,隨著離心力的作用與鋼桶內壁壓緊,鋼桶由壓盤緊壓于底座上不動,鋼刷轉動刷桶。
對于銹蝕太嚴重的鋼桶表面,最好采用噴砂、拋丸等方法較為理想,對于舊漆清除,這種方法也是最理想的。
2.化學除銹
化學除銹的原理是:金屬的銹蝕產物主要是金屬的氧化皮,化學除銹就是用酸溶液與這些金屬氧化物發生化學反應,使其溶解在酸溶液中。另外,酸與金屬作用產生氫氣,使氧化皮機械地剝落。
在工廠里除銹習慣上叫酸洗,酸洗的方式目前廣泛應用的是浸漬酸洗和噴淋酸洗。一般當金屬經脫脂處理后,再進行酸洗除銹,接著用水洗凈,再以堿液進行中和處理,其工藝一般是:酸洗除銹→冷水沖洗→熱水沖洗→中和處理→冷水沖洗→熱水沖洗(或繼之進行磷化處理)。
三、磷化處理
磷化是指鋼桶表面經含有鋅、錳、鉻、鐵等磷酸二氫鹽的酸性溶液處理后發生化學反應,在金屬表面形成一層主要成分為不溶于水的穩定的磷酸鹽保護膜的過程。
1.磷化的作用
(1)提高耐蝕性:磷化膜是一層不導電的隔離層,使金屬表面由原來的優良導體變成不良導體,抑制金屬表面微電池的形成,有效阻止涂膜的腐蝕。
(2)提高附著力:磷化處理能使基體與涂層間的附著力大大提高。這是因為磷化膜與金屬可形成緊密結合的整個結構,其間沒有明顯分界面,而且磷化膜具有多孔性,涂料可以滲透到其孔隙中互相滲透,形成“拋錨效應”緊密結合,提高了附著力。
(3)提供潔凈的表面:由于磷化膜只能在無油污、無銹層的潔凈金屬表面上形成,所以磷化處理后的金屬表面是清潔、均勻、無油、無銹的。
(4)可改善金屬材料的冷加工性能:經磷化處理后的金屬更易進行冷加工。
(5)改進表面摩擦性能:磷化后的金屬表面平整平滑度提高,易于滑動。
因此目前鋼桶涂裝,幾乎100%采用涂裝前磷化處理,磷化處理是鋼桶涂裝前處理工藝中不可缺少的重要環節。
2.磷化處理工藝
磷化工藝可采用浸漬、噴淋、涂刷等幾種方法。在鋼桶生產中,最常用的方法是噴淋法。噴淋法是用泵將磷化液加壓,并以0.1~0.2MPa壓力將磷化液噴成霧狀噴淋在鋼桶表面,只需經1~2min處理即可達到磷化目的。利用噴射的沖擊力與磷化時的化學作用相結合,使磷化速度提高,噴淋液濃度較低,形成的膜層結晶細密、均勻。
四、鈍化處理
金屬表面在完成除油、除銹等表面處理后,往往容易重新生銹。 為了防止發生返銹,通常要進行化學處理,使金屬表面形成一層保護膜。鈍化處理就是其中一種方法,形成的鈍化膜不活,因此有增強防銹的功能。另外,鈍化也常是磷化處理工藝中的后處理工序。把金屬與鉻鹽作用生成三價鉻離子(Cr3+)與六價鉻離子(Cr6+)組成的鉻化層的過程稱為鈍化。
長期以來,鈍化劑使用的主要成分是鉻酸鹽,由于它存在毒性大、污染環境的缺點,使用受到限制。含鉻污水在排放前需經嚴格治理。目前使用的大多是低含鉻量的鈍化液配方,并配合嚴格的廢水治理措施。
五、鋼桶表面綜合處理法
1.綜合除油除銹處理(配方見表14-1)
這種方法的特點是,乳化除油和酸洗除銹相互促進,酸洗產生的氫氣促進乳化劑的乳化作用,將氧化皮或銹表面的油污去掉,便于酸與鐵銹產生接觸,因此時間快、效果好、能簡化工藝、減輕勞動強度。
2.綜合防銹處理(配方見表14-1)
這種處理法具有較高的防銹能力,一般四小時內可保持不生銹,即使用水沖洗干凈,也有較好的防銹能力。適用于鋼桶處理后不能及時烘干或涂漆的情況,鋼桶短時間隔置不會重新起銹。
3.除油、除銹、鈍化“三合一”處理(配方見表14-1)
這種處理方法可同時達到除油、除銹、鈍化的要求。但鋼桶表面帶有氧化皮和嚴重的銹斑時,此法不太適宜,用這種方法處理后,經熱水沖洗,烘干后即可涂漆。
表14-1 綜合處理配方表
處理液功能 |
處理液組分 |
含量(g/L) |
綜合除油除銹修理 |
硫酸 |
15~25份 |
若丁 |
0.06~0.1份 |
平平加或OP緩蝕劑 |
0.6份 |
烷基苯磺酸鈉 |
0.6份 |
水 |
100份 |
綜合防銹處理 |
磷酸氫二鈉 |
4份 |
亞硝酸鈉 |
7份 |
碳酸氫鈉 |
1.2份 |
甘油 |
1.8份 |
水 |
100份 |
除油、除銹、鈍化“三合一”處理 |
磷酸 |
50~300g/L |
硫脲 |
3~5g/L |
M-7有機硅酸鹽溶液 |
0.1g/L |
OP-7乳化劑 |
3~5g/L |
處理條件:槽液溫度85℃以上。處理時間:2~3分鐘。 |
4.除油、酸洗、磷化、鈍化“四合一”處理
四步工序一步完成,大大減少設備和作業面積,可提高效率,降低成本,但質量控制技術要求較高,兩種比較成熟、在生產中使用已取得較好處理效果的配方見表14-2。
表14-2 “四合一”處理液配方
序號 |
組分名稱 |
使用量
(g/L) |
處理條件 |
處理方式 |
溫度(℃) |
時間(min) |
1 |
相對密度1.66的磷酸(80%) |
110~180ml/L |
40~60 |
10~15(浸漬)
1~2(噴射) |
浸漬或噴射 |
氧化鋅 |
30~50 |
硝酸鋅 |
150~170 |
氯化鎂 |
15~30 |
鉬酸銨 |
0.8~1.2 |
烷基苯磺酸鈉 |
20~40ml/L |
酒石酸 |
5~10 |
重鉻酸鉀 |
0.2~0.4 |
水 |
余量 |
2 |
磷酸二氫鋅 |
50~70 |
50~70 |
10~20(浸漬)
1~2(噴射) |
浸漬或噴射 |
硝酸鋅 |
100~140 |
亞硝酸鈉 |
0.1~1 |
硝酸鈣 |
0.2~1 |
酒石酸 |
5~8 |
烷基苯磺酸鈉 |
5~15 |
重鉻酸鉀 |
0.3~0.5 |
水 |
余量 |
六、表面處理常見缺陷及改善措施
目前國內大多數鋼桶生產企業采用的原材料鋼板是冷軋薄鋼板,對于冷軋薄鋼板,表面處理主要是除油和磷化,其它處理表面處理根據材料和需求的具體情況酌量取舍。
1.除油中常見的問題及解決方法(見表14-3)
表14-3除油中常見的問題及解決方法
問題 |
出現原因 |
解決方法 |
除油效果不佳 |
脫脂劑選擇不當 |
根據油污的具體情況合理選擇脫脂劑。 |
脫脂工藝選擇不當 |
可采用二次脫脂工藝。可多級脫脂,多級清洗 |
表面油污過厚,脫脂不均勻 |
一般要先進行手工預擦洗,先除去鋼板上嚴重的油污、灰塵、泥沙等 |
除油時間過短 |
延長除油時間 |
除油溫度偏低 |
提高除油溫度 |
脫脂劑濃度偏低 |
按照使用要求提高濃度至工藝范圍 |
機械作用不夠 |
提高噴射壓力 |
噴嘴堵塞,流量不足 |
定期清理噴嘴 |
工作液中含油量太高 |
定期更換槽液,采用二槽或多槽清洗 |
脫脂后水洗不徹底 |
加強水洗,水洗水要連續溢流 |
工作液泡沫高 |
溫度過低 |
提高溫度至規定范圍 |
循環泵密封處磨損而進空氣 |
更換泵的密封材料,最好選用立式泵 |
脫脂劑選擇不當 |
更換脫脂劑,選用低泡或無泡型新型脫脂劑 |
噴射壓力過高 |
降低噴射壓力,調整噴嘴位置等 |
沒采用消泡工藝 |
采用消泡劑,如醇類、硅油類、聚醚類等 |
水洗槽泡沫過多 |
水洗槽溢流量太小 |
加大溢流水量 |
循環泵密封處磨損而進空氣 |
更換泵的密封材料,最好選用立式泵 |
槽液使用時間長 |
定期更換槽液 |
水洗槽堿度過高 |
堿槽向水洗槽竄溶液 |
改造設備,避免竄液 |
鋼桶帶太多的堿液進入水洗槽 |
改變夾持形式,延長滴液時間 |
水洗槽的溢流量太小 |
加大溢流量 |
槽液使用時間長 |
定期更換槽液 |
鋼桶水洗后生銹 |
工序間隔時間過長 |
工序間增加噴濕 |
鋼桶在水洗段時間過長 |
零件不允許在此長時間停留,加緩蝕劑。 |
2.磷化常見弊病及解決措施(見表14-4)
表14-4磷化常見弊病及解決措施
故障現象 |
產生原因 |
解決措施 |
磷化膜結晶粗糙、多孔 |
游離酸度過高 |
降低游離酸度 |
磷化液中氧化劑不足 |
增加氧化劑比重 |
亞鐵離子含量過高 |
加雙氧水調整 |
鋼桶表面有殘酸 |
加強中和及水洗 |
鋼桶表面過腐蝕 |
控制酸洗液濃度和酸洗時間 |
膜層過薄,無明顯結晶 |
總酸度過高 |
加水稀釋 |
鋼桶表面有硬化層 |
用強酸侵蝕或噴砂處理 |
亞鐵離子含量過低 |
補加磷酸二氫鐵 |
溫度低 |
提高槽液溫度 |
鋼桶表面黏附白色粉狀沉淀 |
游離酸度低,游離磷酸量少 |
補充磷酸二氫鋅,在特殊情況下,可加磷酸調整游離酸度 |
含鐵離子少 |
磷化液中應留一定量的沉淀物,新配溶液與老溶液混合使用 |
鋼桶表面氧化物未除凈 |
加強酸洗,充分水洗 |
溶液氧化劑過量,總酸度過高 |
停加氧化劑,調整酸比 |
槽內沉淀物過多 |
清除過多的沉淀物 |
磷化膜不均勻、發花或有斑點 |
除油不干凈 |
加強除油、清洗 |
溫度過低 |
提高槽液溫度 |
鋼桶表面鈍化 |
加強酸洗 |
酸比失調 |
將酸比調整到工藝范圍 |
磷化膜不易形成 |
鋼桶表面有硬化層 |
改進加工方法,除去硬化層 |
溶液中硫酸根過高 |
用鋇鹽處理,使其降至工藝規范要求 |
溶液中混入雜質 |
更換磷化液 |
五氧化二磷含量過低 |
補充磷酸鹽 |
磷化膜耐蝕性差與生銹 |
磷化膜晶粒過粗或過細 |
調整酸比 |
游離酸含量過高 |
降低游離酸,可加氧化鋅或氫氧化鋅 |
鋼桶表面過腐蝕 |
控制酸洗過程 |
溶液中磷酸鹽含量不足 |
補充磷酸二氫鹽 |
鋼桶表面有殘酸 |
加強中和與水洗 |
磷化膜發紅,耐蝕力下降 |
酸洗液中雜質附在金屬有面上 |
加強酸洗質量控制 |
銅離子混入磷化液 |
用鐵屑置換除去或用硫化物處理,使之沉淀去除,調整酸度 |
磷化溶液發黑 |
槽液溫度低于規定溫度 |
停止磷化,升高槽液溫度至沸點,保持1~2h,并空氣攪拌,直至恢復原色 |
溶液中亞鐵離子過高 |
加氧化劑如雙氧水、高錳酸鉀 |
總酸度過低 |
補充硝酸鋅等,提高總酸度 |
【返回目錄】