《廠長經理的設備管理課》
主講/辛巧娟
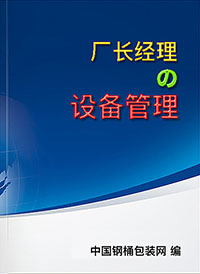
第二十五講
精益生產和精益維修
最早的精益生產來源于日本豐田大野耐一等研究和實踐的成果。其中有兩大要點, 一是準時化;二是人性化的自動化(并非純粹設備的自動化),稱為TPS,即豐田生產體系。其簡單描述是:根據訂單,通過看板傳遞信息,后拉式組織生產,力爭將中間庫存不斷降低,追求零庫存管理。也就是說企業沒有中間庫,沒有最終庫,接到訂單后逆推到每一道工序,直到第一道工序。美國人稱之為JIT(Just In Time)即準時化生產。JIT又稱為適時生產,就是在適當的時候生產出適當的中間或最終產品。后來麻省理工學院的學者將這種生產方式總結提煉為Lean Production,一般翻譯成精益生產,也有翻譯成精實生產的。
顯然,這種后拉式生產組織模式可以減少流動資金占有、減少庫存、降低市場變化風險,但卻對管理提出更高要求和挑戰。精益生產要求設備隨時待命,有更高的可用性,更低的故障率、設備管理組織需要有更快的應變能力,可以更迅速地解決現場問題。在這樣的前提下,國際一些企業提出精益維修管理問題。所謂的精益維修,就是讓維修適應精益生產的要求,是對傳統維修管理的挑戰,是更高水平、更精準的維修管理體制。
在當今世界,很多企業為了能夠應付激烈競爭的局面,要不斷增加利潤。降低成本成為實現這一目標的重要而且簡潔的手段。然而,連續降低成本也出現了一些負面的效果。于是不少企業開始探索精益生產的方式,與此對應的精益維修就應運而生。
在精益領域的維修就是關注價值的維修管理。
1)從成本的思維轉換成價值思維——傳統維修預算的關注點主要是降低成本,但要看到它能夠給組織或者客戶創造多少價值這一積極的一面。
2)強化維修組織——精益維修組織要為客戶創造附加值,是客戶的重要合作伙伴。
3)為產能提升做出貢獻——精益維修通過精益文化和工具的導入提升設備可靠性,減少停機損失,為產能和效益提升做出貢獻。
4)以少得多——通過良好精益思想和工具應用,可以利用較少設備生產更多產品,以優秀備件管理,降低庫存。
5)簡化工作——通過知識共有化,包括維修任務的描述、管理流程計劃、工具的運用來簡化工作。
關鍵的精益要素可以使組織效率改善,并保持持續的進步。它不僅是為了堵住漏洞、解決問題,達到某種數量的下降,而且讓我們的工作得到增值。其要素包含:
1)在客戶眼里,增加價值與無價值的比例不斷改善。
2)要了解精益的相關原則。
3)選擇正確的工具。
4)持續改善的理念。
5)營造改善的文化基礎。
沒有做過精益生產的人往往很難發現改善點,因為這些都是生產系統的固有內容,大家一直都是這么做的。另外的原四是改善項目更關注于以往正在進行的流程,看如何改善并使之創造增值,而非從大系統的角度看正在做的事情是否有價值。
精益生產要從文化上引導企業,其關鍵點是:
1)價值流——業務流程。
2)減少浪費——增加有附加值的任務。
3)流程——按照客戶要求方向進步。
4)后拉式——滿足客戶實際而非預想的需求。
5)完善——創造持續改善文化。
另外一個關鍵要素是選擇正確的工具。雖然沒有確定的工具清單,其實很多工具都可以應用,如企業的有氧活動(CPS+OPL)等。
精益生產是沒有終點的旅程,一旦停下來就可能被其他企業超越,所以要不斷培訓員工,不斷學習新的東西。
精益生產也是以文化為基礎的,因為以前的很多改善是專注于設備和流程控制,但其中60%~80%的原因卻是來自人的因素——文化。也不限于管理上的或是現場操作層面上的,而是所有層面上的制度和行為。這往往是很難改變的,需要不斷地從基礎、領導、制度、參與和評價等方面堅持下去。
如何成為一個精益維修組織呢?首先要選擇正確的工作項目;還要選擇和培訓恰當的人;要應用準確的路線圖和工具,并提供有效的管理支持,旨在實現預期的結果。
選擇正確的工作項:項目要與組織目標相關聯,要確保項目可以獲益,要將項目按照價值、資源需求和時間排出優先序,而且選擇項目的關鍵管理要素,項目要關注“浪費”問題。
選擇和培訓恰當的人:要保證正確的領導和參與者,選擇可以改善的合適人選,建立精益的支持團隊,保證足夠的培訓和改善時間,而且要保證恰當的資源支持到位。
應用準確的路線圖和工具:這些內容包括價值流圖、標準化、糾錯防錯設計、快速改善流程以及精益矩陣等。
提供有效的管理支持:要經常性地進步評價,不斷清除障礙,持續地溝通,評價要與績效管理——個人KPI(Key Performance Indicator——關健績效指標法)掛鉤。
實現預期的結果:要推進有效的控制計劃,專注過程的常規培訓,每季度評價系統效率,持續識別和開發新項目等。
經常出現的主要障礙表現為人們的短期觀念,以技術改造為借口,過于關注設備硬件,忽視軟環境、缺乏激情以及沒有愿景等。
成為精益維修組織的關鍵因素是人的行為和態度——文化。首先要詳細、準確地描述什么是正確的行為,要能夠度量這些行為,要讓大家看到正反兩方面的結果差異,得到大家的晌應。為此,需要投入一定時間來糾正人的態度,人們是否主動?是否一起進步?怎么做更好?
精益維修組織的另外特征是具有精湛的診斷和維修技術。維修組織不是總在忙忙亂亂。要能夠不斷找出問題的源頭,解決未來的問題。企業要不斷培訓頃工掌握診斷知識,不斷告訴團隊如何積累經驗。
激情是行動的詞匯而非僅僅代表情感。精益團隊的領導應該是具有激情的領導,是工作的典范,每天都創造價值,每天都有勇氣,每天都樂觀,每天都是優秀的溝通者。
廣義的精益維修是個三維的概念,它體現在以下方面。
1、從設備整個生命周期上尋求精益
在設備整個生命周期管理的各個環節,包括設備規劃、選型、招標投標決策、安裝、使用、維護、修理、改造、淘汰都存在降低浪費和創造增值的空間,都可以尋求精益。
2、從維修管理流程上尋求精益
維修管理流程實際上就是從維修策略制定、信息采集、故障診斷、維修組織設計、維修資源配置、維修流程、維修技術和驗收標準,還包括設備管理KPI評價以及激勵等全過程,這也是PDCA循環在設備管理邏輯軸上的延伸。每個環節都存在精益的內容。例如,不向的策略,其投入產出比不同,不同的維修組織結構和維修資源配置會產生不同的維修成本;不同的KPI評價引導不同的結果。
3、從資源要素上尋求精益
資源是維修效果的保證。維修資源包括維修設備、備件、材料、能源、技術服務、信息、人工、知識、關系等。合理地配置不同的維修資源,充分發揮企業內部維修資源的效率,挖掘維修資源的價值,也是精益維修的重要任務。例如,備件庫存的優化可以在保證檢修的前提下使維修備件庫存和流動資金占有最小化;有效地將企業內部員工自主維護、外部合同化維修與企業內部專業維修隊伍合理搭配,可以使維修成本最小化,維修效率最大化;做好維修知識資產的發掘、儲存、分享、標準化和培訓,可以大大提升管理效率,減少重復性差錯,提升維修組織的整體水平, 其整體架構如圖25-1所示。
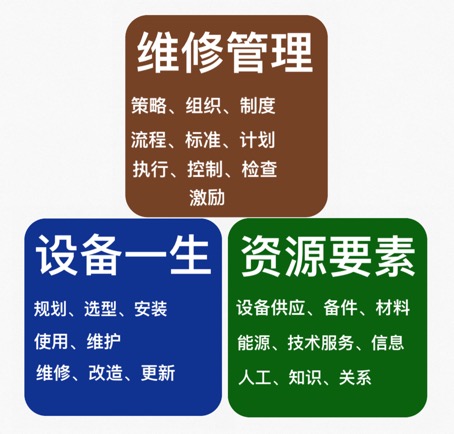
圖25-1 精益維修架構
返回目錄