水性漆預處理鋼板涂裝流水線改造方案!
文/蘇杰
隨著工程機械、電站鍋爐、海洋工程、水力發電、石油化工、軍工裝備等行業的飛速發展,衍生的需求設備或產品對鋼板的需求量越來越多。鋼板在港機制造中是主要的生產材料,鋼板投產前的預處理質量直接決定產品的使用壽命。在現代化工業發展的初期階段,幾乎所有傳統的鋼板預處理中用的涂料都是以有機溶劑為分散介質的溶劑型涂料。溶劑型涂料中揮發出的有機化合物對人體有害、污染環境、易燃易爆。水性漆是以水作主要溶劑或分散介質,水性漆能降低對空氣的污染,有利于人類的健康生活和環境的可持續發展。為積極響應重工制造企業環保減排的嚴格要求,保護環境,改善涂裝人員的工作條件,工程機械應用水性漆勢在必行。水性漆涂料逐步代替傳統的溶劑型涂料的預處理涂裝流水線在重工業鋼板預處理中應運而生。本文闡述一套將傳統的預處理鋼板涂裝流水線改造成水性漆預處理鋼板涂裝流水線的實例,在合理做好污水源頭管理和環境保護方面有著重要的意義。
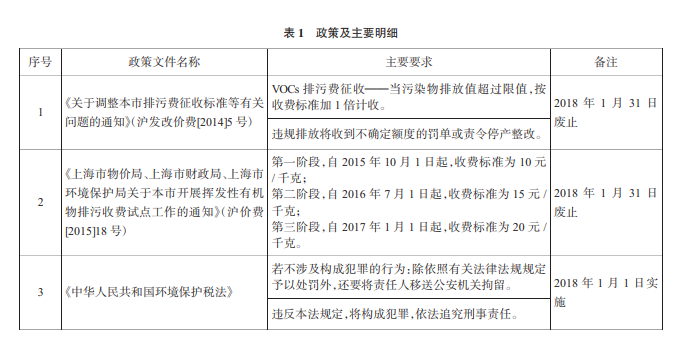
1、水性漆預處理鋼板涂裝流水線改造
根據調研分析,假若采用末端治理,后期維護處理成本高昂,而新建一條流水線一次性設備投入400萬元左右,且每年維護成本在100萬元以上。因此,開發改造傳統流水線成為最經濟可行的減排方案。針對傳統的預處理鋼板涂裝流水線上設備的不足之處提出改造方案,在原有設備基礎上進行局部升級,原有的工位、運轉系統、控制系統、加熱系統保持不變,只要求噴涂設備升級為水性專用噴涂系統,同時增加排風系統以保證涂層干燥時的通風量和供氣系統的供氣壓。
2、流水線工作流程
水性漆預處理鋼板涂裝流水線工作原理:通過輸送、噴漆、廢氣治理設備的流水線作業,實現鋼板底漆的均勻合格規范噴涂。此流水線主要包括6大部分:油漆烘干室、水性漆輸送管、廢氣治理系統以及原有流水線上的鋼板輸送系統、調漆房、噴漆房(見圖1)。將研究的符合鋼板底漆配比要求的水性漆,通過高壓無氣噴涂泵壓送至噴漆房,將已經在輸送機上且表面已除銹、清灰的鋼板,進行底漆涂裝預處理作業。
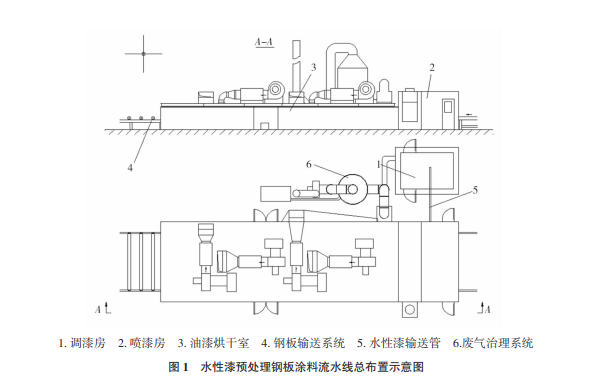
3、流水線改造施工步驟
安裝調漆房設備(配備氣動攪拌器,混合桶)→連接調漆房與噴漆房→安裝油漆烘干室設備(增設溫度感應探頭若干)→安裝電氣控制柜1套(采用PLC控制)→安裝廢氣治理系統(洗滌塔與電絮凝裝置,用水管進行連接)→流水線試運行。
4、流水線改造技術關鍵點
通過研發、設計、改造等多方面齊頭并進,將水性漆涂料成功在傳統預處理涂裝流水線上使用,在重工制造業鋼板底漆預處理過程,不僅大大減少了VOCs排放、改善車間工作環境,而且減輕企業在末端治理設備上的投入費用,幫助企業最大經濟程度的實現合規合法的環保生產。流水線改造主要在5個方面進行技術創新和攻關:
(1)改變傳統流水線上噴漆用的噴嘴選型,將噴嘴選型由38Z55型改成19Z40型,新型噴嘴具有防銹性能,不僅能提高在鋼板表面的噴涂質量,而且成功替代傳統流水線上的38Z55型噴嘴。
(2)通過將噴漆小車、高壓涂料輸送管、高壓無氣噴槍與新型噴嘴進行組合,并配上感應裝置形成一套自動噴涂水性漆的噴漆設備。
(3)為解決傳統流水線上調漆房使用水性漆涂裝作業時容易出現設備銹蝕的情況,增加高壓無氣噴涂泵1套(壓縮比為42:1)、攪拌器1套和混合桶1套(80L)設備,對原調漆房設置進行改造,實現水性漆涂料與水15:3的混合配比,保證噴涂質量。
(4)為解決油漆烘干室加熱溫度不均衡的問題,在板鏈輸送機的上、下增加吹風嘴組,對原油漆烘干室進行改造,將循環風管中電加熱器的熱風均勻輸送到鋼板表面,實現水性漆涂料在鋼板表面能夠快速固化,時效提高50%(≤5min),油漆漆膜厚度的質量要求也得以滿足。
(5)為解決末端廢氣的達標排放問題(漆霧顆粒物排放限值20mg/m3),增設1套廢氣治理系統,將烘干室、噴漆室內產生的廢氣接收至干式漆霧過濾器,再進入洗滌塔進行噴淋過濾后達標排放,減少對施工人員身體健康造成的危害。
為了可持續發展,溶劑型涂料即將退出歷史的舞臺,水性漆將有可能全面取代溶劑型涂料。對傳統預處理鋼板涂裝流水線進行水性漆涂裝改造,整個項目改造內容少、成本低、改造難度低,改造后效果明顯,符合綠色生產、工藝改革提質增效的發展理念,能夠規避使用溶劑型涂料產生的VOCs排放、資源浪費、安全隱患、工作環境污染以及不可再生等缺點,在行動上為可持續發展保駕。 |