【專利】包裝鋼桶縮口機
文/國家知識產權局
申請號 |
|
CN01127882.X |
申請日 |
|
2001.09.26 |
公開(公告)號 |
|
CN1408620A |
公開(公告)日 |
|
2003.04.09 |
IPC分類號 |
|
B65D1/12; B21D41/04 |
申請(專利權)人 |
|
東莞振華制桶有限公司; |
發明人 |
|
車振華; |
優先權號 |
|
|
一、摘要:
包裝鋼桶縮口機,涉及包裝容器生產設備技術領域,特指一種一次上料完成桶身的縮口、翻邊、滾筋的縮口機。技術方案為:控制成型滾輪進退的進刀氣缸與成型滾輪連接。本發明可以將成型速度由凸輪進刀方式的3-4只/分鐘提高到7-8只/分鐘,最高可達9只/分鐘;可以縮口出表面無痕跡的縮口,外觀圓滑、美觀,便于后續的表面處理、噴涂、印刷;在成型的過程中,不容易出現板材變薄的現象,極大地降低了成本,而由于將三道工序結合在一起一次完成,節約了生產空間及設備的花費。
二、權利要求書
1、包裝鋼桶縮口機,包括:機身(10)、電機(20)、減速箱 (30)、成型滾輪(40)、頂緊氣缸(60)、頂緊盤(70)、成型模(90), 機身(10)上連接電機(20)、減速箱(30)、頂緊氣缸(60);電 機(20)輸出軸經減速箱(30)后連接成型模(90),頂緊盤(70) 連接頂緊氣缸(60);其特征在于:控制成型滾輪(40)進退的進 刀氣缸(50)與成型滾輪(40)連接。
2、根據權利要求1所述的包裝鋼桶縮口機,其特征在于:成型模(90)的滾筋模(901)、翻邊模(902)套于減速箱(30)的 輸出軸(301)上,位于滾筋模(901)、翻邊模(902)間的彈性元件(903)通過內襯(905)與輸出軸(301)相套接,并在彈性元件(903)外圓上套有縮口模(904);滾筋模(901)、翻邊模(902) 與縮口模(904)相接的一側各凸伸一環(9011)、(9021),縮口模 (904)的內圓端亦凸伸有一環(9041)。
3、根據權利要求1所述的包裝鋼桶縮口機,其特征在于:控 制縮口機動作的PLC控制部分(80)連接于機身(10)上。
三、說明書
包裝鋼桶縮口機
1、技術領域:
本發明涉及包裝容器生產設備技術領域,特指一種一次上料 完成桶身的縮口、翻邊、滾筋的縮口機。
2、背景技術:
縮口廣泛運用于包裝鋼桶的生產中,作為鋼桶成型過程中的 一道重要的工序,對鋼桶端部進行不同直徑變化的縮口,有利于滿 足集裝箱滿載運輸的要求,提高鋼桶強度,增強圓整性,利于后續 處理;良好的縮口將會極大地提高出口鋼桶適于長距離海運的要 求;同時,賦予鋼桶優良的外觀,提升產品檔次和競爭力。
目前,國內大多數生產廠家采用的縮口都是單一的對桶口或 桶底進行縮口,不能實現縮口、翻邊、滾筋在同一臺縮口機上完成, 而且,縮口時均采用凸輪控制的靠模方式完成;這樣一來,復雜的 傳動機構使得設備占用場地大,凸輪的進刀速度很慢,導致生產速 度只能達到3-4只/分鐘,且縮口部分的外觀質量不良,有多道環 向的成型痕跡,外觀看起來加工很粗糙。
此外亦有部分廠家將縮口、翻邊、滾筋三道工序在同一機器 上實現,其結構如專利ZL 92203895.3中所述,具體結構見附圖1、2,由機身1、傳動裝置2、3、氣動裝置4、壓緊機構5、胎模6、翻邊滾輪7、波紋滾輪8、縮口滾輪9、翻邊凸輪10、波紋凸輪11、縮口凸輪12、凸輪支架13、機械手14組成,胎模6上設有翻邊、 波紋、縮口三個模印,凸輪支架13上設有與胎模6相對應的翻邊、波紋、縮口凸輪10、11、12,此三個凸輪同時控制機械手14上的 翻邊滾輪7、波紋滾輪8、縮口滾輪9的上升和下壓;當工件套于 胎模6上后,打開氣動裝置4,使壓緊機構5向前運動,直至凸輪 支架13帶動翻邊凸輪10、波紋凸輪11、縮口凸輪12同步運轉,隨著凸輪各自的升降變化,機械手14上連接的滾輪相應的上升或 下壓,當與胎模6上的模印相吻合后,則停止傳動裝置2、3,開啟氣動裝置4,取下工件即可;此種結構,由于是凸輪帶動滾輪,通過靠模方式實現一臺機器上的翻邊、波紋、縮口,存在由支架到凸輪,再到滾輪的多重運動傳遞,使得成型速度緩慢,生產效率低, 控制精度不高;而且,波紋外翻,無法滿足集裝箱滿載運輸的要求。
3、發明內容:
本發明的目的在于提供一種一次上料完成縮口、翻邊、滾筋, 生產速度快,質量好,適于集裝箱滿載運輸的縮口機。
本發明是通過如下技術方案實現的:控制成型滾輪進退的進 刀氣缸與成型滾輪連接,所述的成型模的滾筋模、翻邊模套于減速 箱的輸出軸上,位于滾筋模、翻邊模間的彈性元件通過內襯與輸出 軸相套接,并在彈性元件外圓上套有縮口模;滾筋模、翻邊模與縮 口模相接的一側各凸伸一環,縮口模的內圓端亦凸伸有一環;控制 縮口機動作的PLC控制部分連接于機身上。
本發明成型滾輪由進刀氣缸控制其進退,而進刀氣缸、進刀 氣缸等的動作都由PLC控制部分實現自動控制,極大地提高了成 型的速度,利用本發明可以將成型速度由凸輪進刀方式的3-4只/ 分種提高到7-8只/分鐘,最高可達9只/分鐘;通過縮口模的偏心 旋轉,以及滾筋模、翻邊模間的配合,可以縮口出表面無痕跡的縮 口,外觀圓滑、美觀,便于后續的表面處理、噴涂、印刷;在成型 的過程中,不容易出現板材變薄的現象,極大地降低了成本,而由 于將三道工序結合在一起一次完成,節約了生產空間及設備的花費。
4、附圖說明:
下面結合附圖對本發明進一步說明:
附圖1為現有縮口機結構示意圖;

附圖2為現有縮口機俯視圖;
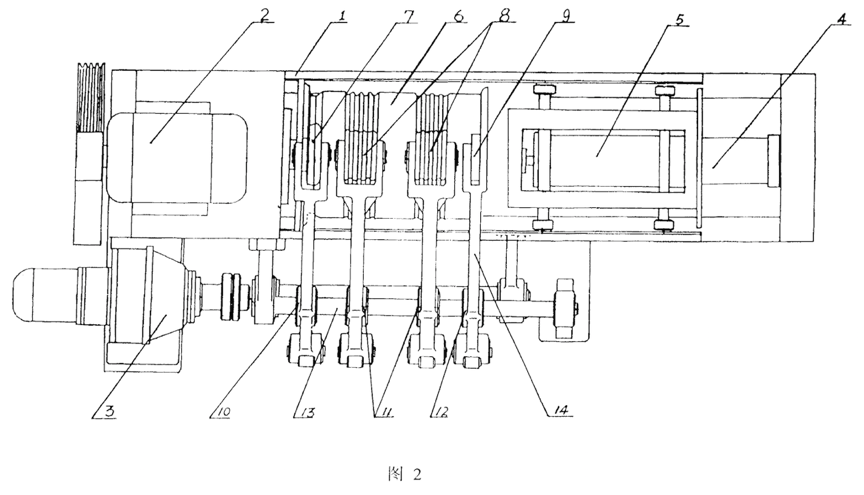
附圖3為本發明結構示意圖;
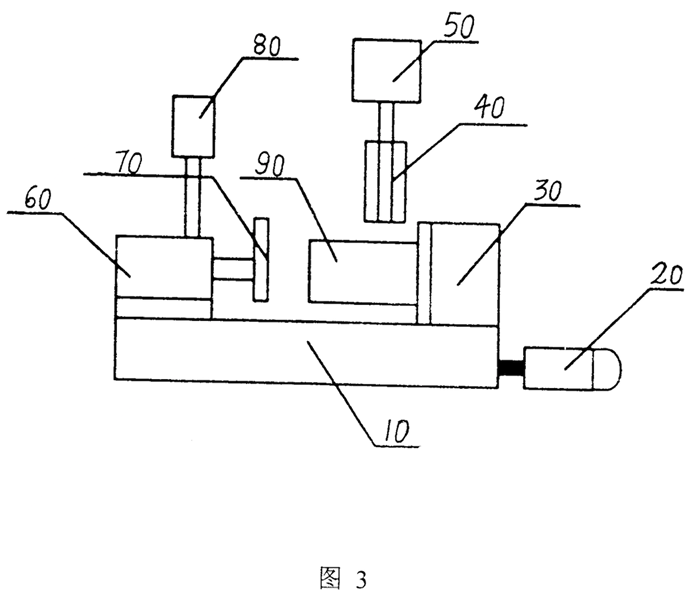
附圖4為本發明成型模90剖視示意圖。
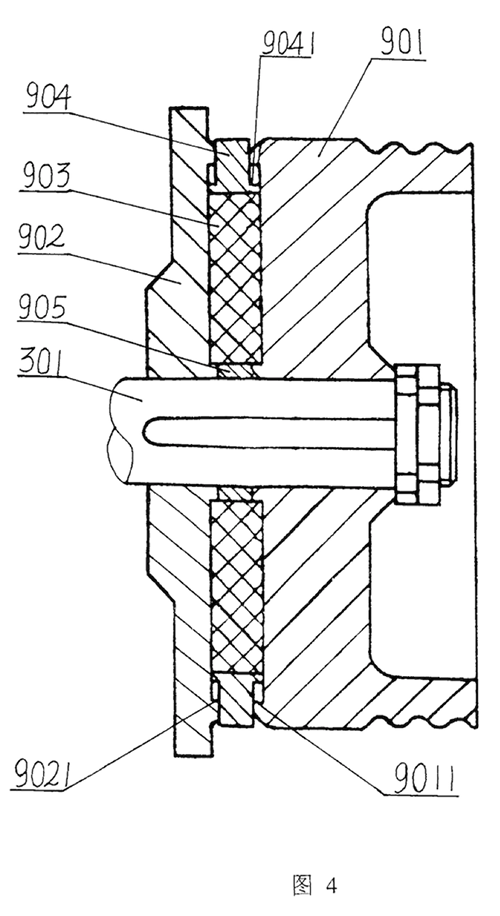
5、具體實施方式:
見附圖3、4,本發明包括有機身10、電機20、減速箱30、成型滾輪40、頂緊氣缸60、頂緊盤70、成型模90,機身10上連 接電機20、減速箱30、頂緊氣缸60;電機20輸出軸經減速箱30后連接成型模90,頂緊盤70連接頂緊氣缸60;控制成型滾輪40進退的進刀氣缸50與成型滾輪40連接;控制縮口機動作的PLC控制部分80亦連接于機身10上;所述的成型模90的滾筋模901、 翻邊模902套于減速箱30的輸出軸301上,位于滾筋模901、翻邊模902間的彈性元件903通過內襯905與輸出軸301相套接,并在 彈性元件903外圓上套有縮口模904;滾筋模901、翻邊模902與縮口模904相接的一側各凸伸一環9011、9021,縮口模904的內圓 端亦凸伸有一環9041。
當使用本發明時,先將桶料放于成型滾輪40上,然后由PLC控制部分80控制頂緊氣缸60,將頂緊盤70頂緊桶料,電機20啟動,通過減速箱30帶動成型模90旋轉,而成型模90的旋轉帶動桶料同步旋轉;同時,進刀氣缸50將成型滾輪40頂進,當進刀到一定的距離后,成型滾輪40的縮口滾部分首先頂住成型滾輪40,繼續進刀,通過桶料將縮口模904向內壓,彈性元件903被壓縮,當縮口模904的外圓與翻邊模902或縮口模904的環9011、9021外圓平齊時,縮口到位,且翻邊、滾筋亦同步完成;此時,進刀氣缸50停止成型滾輪40的進刀,進刀氣缸50內的壓力控制器達到預定的壓力數值,發送一信號到PLC控制部分80,由其控制成型 滾輪40的退刀以及頂緊盤70的后退,取下成型的桶料即可;由于在縮口的過程中,桶料內有隨著壓力大小而收縮的彈性元件903通 過縮口模904頂住,因而縮口質量好。