很多工序都要進行質量檢驗,是不是太麻煩?如何減少質檢工序?
文/三哥
1.質檢工序太多會增加成本,還會破壞生產節奏;
2.質檢工序的最終目的不是檢驗產品,而是找到生產過程中確保品質的方法,去除質檢工序;
3.未把質檢工序當成調查不良品產生原因的工具、對數據進行管理的體制不健全等4.是質檢工序只增不減的重要原因;
5.把目光聚焦于“制造之時”和“制造過程”上,設置“良品條件”,觀察其是否滿足,能夠有效減少質檢工序;
6. 企業應注意“良品條件”中存在的偏差。
◆?◆?◆?◆
01 .確立“良品條件”,減少質檢工序
質檢工序的目的是為了確認制造出來的產品是否為良品。現如今,質檢工序正在逐漸腐蝕制造業的現場:隨著制造的復雜化,品質保證愈加困難,質檢工序也逐漸增多。
質檢工序一旦增加就很再難削減下去,這些環節最終都會變成企業的沉重負擔,降低企業的競爭力。從根本上來看,沒有任何附加價值的質檢工序越少越好。
但這里有一個問題:如果不檢查成品質量,又如何在制造環節中判斷產品是否合格呢?為了突破這個瓶頸,企業需要確立制造良品的方式,也就是迎接挑戰,創造出“制造良品的條件”,實現匠人之道。
“質檢工序太多了,怎么減少呢?”為制造業提供咨詢及工程服務的埃姆特科技公司(AIMNEXT,總部位于東京),最近收到了很多類似的問題。本是為品質“把關”的質檢工序,怎么反倒給制造現場造成了困擾呢?
◆?◆?◆?◆
02 .用“傳感器”去除加工后的檢查
為什么質檢工序一增加,大家就發愁?因為歸根結底,檢查是一道“無用功”。埃姆特董事長清威人表示:“在生產線上,能夠產生價值的是加工、組裝等制造工序,而不是質檢工序。”雖然質檢工序在保證產品質量方面發揮了重要作用,但在企業看來,質檢工序的增加,意味著成本的增長。
此外,質檢工序還會打亂生產線的流程。從這個層面上來說,它的確是個麻煩。有的質檢工序不僅會打亂周圍的制造工序和生產節拍,還會導致質檢工序前后的產品在庫時間延長。
很多企業在考慮未來勞動力不足的嚴峻形勢后,會大力推行自動化生產線,但仍逃不出質檢工序帶來的負面影響。保留質檢工序,會加大普及生產線自動化的難度,直接導致投資數額增多。而一旦開始推行自動化,后面再想減少質檢工序就十分困難了。
很多尖端企業已經邁出了第一步。例如,在使用機床加工的工序中,使用一種叫做“落座傳感器”的感應裝置,可以有效去除工序后的檢查。落座傳感器可以通過壓縮空氣測定微小縫隙的尺寸,檢查型材是否正確安放到了夾具中。
如果型材和夾具之間有碎屑,就會導致型材的不平整,這樣加工下去會加大不良產品的產生幾率。由于落座傳感器能夠有效預防此類不良品的產生,因此受到了很多企業的青睞。
生產這種落座傳感器的是日本美得龍公司(METROL,總部位于東京都立川市)。該公司董事長松橋卓司表示,希望落座傳感器可以滿足機床企業用戶“無中斷生產線”(去質檢化)的需求(圖1)。
這些企業,都預測到了未來自動化生產線的趨勢。并且,電裝公司(DENSO)等已經采用了美得龍的落座傳感器,成功廢止了加工后的質檢工序。
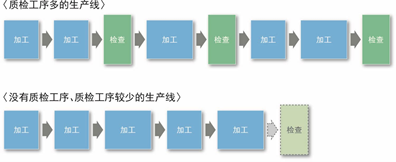
圖1?對沒有質檢工序,或者質檢工序較少的生產線的需求
去除或盡量減少加工工序間的質檢工序,可以提高生產效率,加速工廠的自動化進程。
◆?◆?◆?◆
03 .檢查本身不應成為唯一目的
埃姆特董事長清威人表示,質檢工序增加有各種各樣的理由,但最主要的還是“不良品的產生”。這種情況下,即便企業無法立刻搞清楚狀況,也要馬上恢復生產。因此,企業常常通過追加一道質檢工序,來防止不良品流入下一道工序。
豐田汽車的豐田生產方式(Toyota ProductionSystem,TPS)中有一個重要概念“自工序完結”,即生產線的各個工序要保證自己的品質,不讓不良品流入下一道工序。因此,質檢工序的設置,可以說是一種臨時對策。
問題是,質檢工序設置之后依舊會產生不良品,企業往往不究明其中的原因,只會不斷地推行檢查。
埃姆特董事長清威人表示:“通過比對制造條件和檢查結果,充分、靈活地利用質檢工序收集到的數據,能夠得出行之有效的對策,甚至有望完全廢除質檢工序。但遺憾的是,很多企業只會單純地用質檢工序來判斷產品是否合格。”
隨著時間的流逝,很多相關人員都離開了生產現場,所以很多時候,“檢查”本身成了唯一目的。質檢工序一旦增加就很難減少,說的也是這個道理(圖2)。

圖2?質檢工序增加(不減少)的機制
不良品的產生等問題會讓企業增加質檢工序。如果不究明問題的根源,就會讓質檢工序殘留下來。理想狀態是,查明不良品產生的原因,停止質檢工序。
埃姆特董事長清威人指出:“從根本上講,企業不僅要反省事后追加的質檢工序的必要性,還要時刻檢討所有質檢工序的設置是否合理”。如果還是頻繁產生不良品,那么以查明原因為目的而增設的質檢環節就沒有發揮應有的作用。
反之,如果不良品的發生確實在逐漸減少,那么就可以探討檢查工序的留存問題了。雖然產品交付前的“最終檢查”很難一下子全部廢止,但是在企業工廠的生產線上,為了防止不良品流入下一道工序,還增設了很多“工序間的檢查”,這些檢查是否有必要,企業需要自行判斷。
可惜,現實情況恰恰相反。很多企業的“工序間的檢查”不減反增。《日經制造》雜志通過發送終端信息的方式,向“日經制造NEWS”的讀者朋友們發送了調查問卷。
調查結果顯示,針對“近年來,您工作的工廠有沒有增加工序間的檢查”這一問題,有70%的讀者回答“增加了”。工序間的檢查增加,但維持在適當的水平,這是沒什么大問題的。但在增加數量上,60%以上的讀者都回答了“多”。
為什么質檢工序只增不減呢?“雖然日本企業都實行了可追溯性體系,但把質檢工序當成調查不良品產生原因的工具,對數據進行管理的企業少之又少”。雖然很多企業都有意減少質檢工序,但體制方面還不健全。
◆?◆?◆?◆
04 .看生產過程,而不是產品
怎樣才能有效減少質檢工序呢?實際上,質檢工序是在判定“制造出來的產品”是否合格。所以,如果想去除質檢工序,就要把目光聚焦于“制造的時候”和“制造的過程”上,判斷良品情況(圖3)。
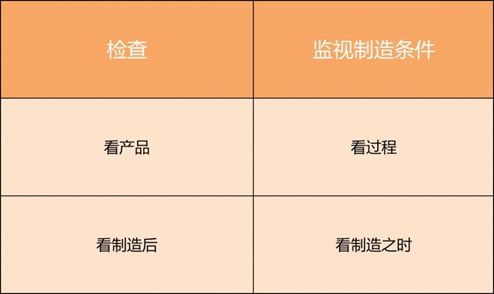
圖3?“檢查”和“監視制造條件”
檢查,是查看制造出來的產品。而監視制造條件,是關注制造時的過程。
你可以這么理解:我們在進行質檢前,會先給產品的尺寸、外觀等定一個基準,然后判斷這些條件是否得到了滿足,進而判斷產品是否合格。
而所謂關注過程,就是對模具溫度、螺絲扭入時的扭力等一系列制造條件設定一個基準。也就是說,要確立制造良品的制造條件(良品條件),然后再監視這些條件是否得到了滿足,進而做出判斷。
例如,阿雷斯提公司(Ahresty)的主營業務是鋁合金壓鑄成型。一直以來,阿雷斯提都是通過X光照射成品來進行成型產品內部構造檢查的。
而現在,阿雷斯提會通過觀察是否滿足實際制造條件來判定產品是否合格:如果實際制造條件滿足良品條件,那么就判定該產品為良品,將其順利流入下一道工序;如果實際制造條件不滿足良品條件,那么就單獨進行內部照射檢查。
X光裝置的內部檢查原理,是看成型產品內部是否存在空洞(空巢)。產品內部的空洞會降低產品的強度和耐久性。這種成型產品主要用于汽車,是一種安裝在汽車底盤上的支架零件,也是一種與汽車性能直接相關的“重要安保零件”。
所以,有空洞的產品都會被認定為不良品。為了找出這些不良品,阿雷斯提此前采用的一直是X光內部檢查的方法。
要想去除內部檢查,企業需要找到可以滿足不會產生空洞的良品條件。阿雷斯提將以往產生不良品的制造條件和內部檢查的全部數據進行了比對,詳細分析了產生空洞的原因,把空洞的主要成因列為制造條件,通過把握“在什么樣的條件下可以生產出良品/不良品”確立了良品條件。
◆?◆?◆?◆
05 .注意偏差產品
如上所述,我們可以根據制造的過程而非產品進行良品判斷,去除檢查工序。當然,企業必須提高警惕,因為良品條件中可能存在偏差。對于制造業而言,管理制度再嚴格,也無法完全規避偏差的出現。
阿雷斯提技術部技術開發2科科長大出克洋表示:“良品條件下制造出來的產品也不一定合格。”因此,“明明滿足良品條件,卻是不良品”“明明沒有滿足良品條件,卻是良品”的情況也時有發生(圖4)。
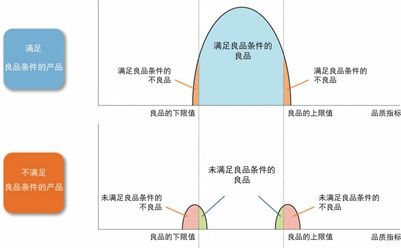
圖4?偏差的影響
由于實際當中會有一定的偏差產生,所以會出現“明明滿足良品條件但還是不良”以及“明明沒有滿足良品條件卻還是良品”的情況。
這兩者之間的概率存在一種此消彼長的關系。更令人頭疼的,是“明明滿足良品條件,卻是不良品”的情況。
因此,為了盡可能地把發生概率降低,企業需要在制造條件的管理范圍方面下一番功夫。“沒有滿足良品條件,卻是良品”的情況會讓企業平衡一定的時間和成本,如果在生產線下確認產品的確沒有問題,可以將其返回生產線。
實際上,阿雷斯提會對未滿足良品條件的全部產品進行X光檢查,如果是良品,就將其投入下一道工序。嚴格來說,這種情況并不能說是完全去除了質檢工序,但相比以往,已經大幅縮減了企業成本。??
|