噴塑技術在鋼桶涂裝上的應用
文/許邦義
摘要:所謂的粉末靜電噴涂是以被涂物為陽極,一般情況下接地:粉末涂料霧化結構為陰極,接電源負高壓,這樣在兩極就形成了高壓靜電場。由于在陰極產生電暈放電,可使噴出的涂料微粒介質帶電,并進一步霧化。按照“同性相斥、異性相吸”的原理,已帶電的微粒狀涂料介質受電場力(F=qE)的作用,沿電力線定向地流向帶正電的被涂物表面,沉積成一層均勻、附著牢固的薄膜。靜電噴涂也可采用正極性電暈放電,但負極性電暈放電的臨界電壓較正極性電暈放電低,又較為穩定、安全且不易產生火花。
關鍵詞:現狀、鋼桶、噴漆、噴塑、環境、健康、技改
?我公司下屬包裝容器分廠主要負責本公司相關產品包裝物的生產。如:50L開口鋼桶及各種塑料瓶,蓋、袋等。其中50L開口鋼桶的年產量約為40萬只,具有國家進出口檢驗檢疫總局頒發的危險化學品出口包裝物生產質量許可證。
我們現有鋼桶生產線中表面涂裝方法使用的是傳統的噴漆工藝,其基本工序為:
酸洗——磷化——干燥——原漆稀釋——噴漆——烘干。
該工藝的不足和問題如下:
1) 工序較多、耗時較長。由于上述工序均需逐一進行,每道工序均有一定的時間要求,走完全套工序約需2個小時。
2) 成本較高、浪費較多。在全套生產工序中除油漆外還需消耗相當數量的鹽酸、磷化液、水、稀釋劑等。這些耗材中有相當部分無法回收。浪費和污染是難免的。
3) 清洗復雜、不利環保。由于在噴漆操作過程中對于多余漆霧的解決方法主要是通過真空水幕吸收法來進行,該方法的缺點為:其一是不能百分之百的吸收所有多余的漆霧,那么就必然有漆霧進入大氣和被人吸入。其二是整個真空水幕系統在工作80小時后即要進行清洗維護,該清洗維護不僅復雜且工作量也很大.對清洗出的廢漆如處理不當還會對環境造成污染。另一點由于稀釋原漆所用的稀釋劑為二甲苯,它對保護環境和員工健康來說均不利。
那么上述的高成本、高勞動強度、環境污染,職工身體健康等問題能否通過技改來進行改變或改善呢?
針對上述生產過程中存在的問題,我們的目光瞄向了近年來在金屬涂裝領域異軍突起并蓬勃發展起來的靜電粉末噴塑技術。下面我們就靜電粉末噴塑技術作一粗略的介紹。
一、靜電粉末噴涂基本原理
所謂的粉末靜電噴涂是以被涂物為陽極,一般情況下接地;粉末涂料霧化結構為陰極,接電源負高壓,這樣在兩極就形成了高壓靜電場。由于在陰極產生電暈放電,可使噴出的涂料微粒介質帶電,并進一步霧化。按照同性相斥,異性相吸”的原理,已帶電的微粒狀涂料介質受電場力(F=qE)的作用,沿電力線定向地流向帶正電的被涂物表面,沉積成層均勻、附著牢固的薄膜。靜電噴涂也可采用正極性電暈放電,但負極性電暈放電的臨界電壓較正極性電暈放電低,又較為穩定、安全且不易產生火花。因此,在通常情況下將被涂物作為正極接地。總體來說,凡被涂物在200℃時不發生變形、能使荷電的粉末微粒吸附在被在其表面,其表面涂裝都可以采用粉末靜電噴涂。因此 粉末靜電噴涂技術可廣泛應用于儀器儀表、家用電器、機電設備、汽車船舶,輕工器材、家具機械及建材等金屬零件的表面防護和裝飾性涂裝。從目前采用的噴涂技術來看,粉末靜電噴涂在工業涂裝中有其獨特的優勢:
1) 粉末涂料是固體涂料,沒有溶劑,不揮發,大大減少了由溶劑引起的污染問題,有利于環保和操作人員的身體健康。
2) 在噴涂過程中,多余的粉末可以利用回收系統集中收集,達到回收再利用的目的,因此其粉末的利用率相當高,使企業的生產成本降低,獲得較好的經濟效益。
3) 整個涂裝過程只需經過前處理、噴涂、固化等工序,簡化了傳統的多工序噴涂手段,使噴涂作業線工作效率提高,無論是手工還是自動操作都比較方便。
4) 粉末靜電噴涂后,經過烘烤就可以得到性能優異的涂膜表面,該涂膜堅固耐用,能夠耐酸、耐堿,同時具有耐磨擦性、抗沖擊性、機械強度高等優點。
從上述的簡介中,可以清晰地看出粉末靜電噴涂的優點基本解決了我們目前噴漆工藝中存在的問題。通過對噴塑技術的了解,我們覺得這種噴塑技術完全可以替代目前我們使用噴漆技術(就我們的噴涂件對噴涂質量的要求而言)。最終我們取得了上級領導支持,同意立項對原噴漆工藝進行技改,要求是:多 快、好、省。
二、改造方案的確定
那么我們如何在現有生產裝置的基礎上,用最少的錢、最短的時間來對裝置進行改造才能達到我們的目的呢?
為了最大限度的節約資金,也為了環境的保護,必須對現有的生產裝置進行最大的利用,因此我們摒棄了直接購買成套靜電粉末噴涂裝置未對原有的噴漆裝置進行簡單的更換,而是決定少量購買靜電粉末噴涂裝置中核心的主要部件來對原設備進行技改,將原裝置作最大限度的保留,盡管這樣做是要承擔定風險的。我們具體想法為:
1) 將原有的噴漆操作室內的水幕及水循環系統全部拆除,保留操作室內的基本空間和真空負壓系統的主體部分。這樣做的目的是拆除水幕及水循環系統,一是因為此系統在以后的改造中已完全無用,二是為了給以后安裝粉末回收系統中的真空過濾器提供合適的空間。保留操作室內的基本空間和真空負壓系統的主體部分,一是為了以后粉末的回收再利用而準備在操作室內的正下方做一個方錐型的粉末回收收集器。二是為了給回收粉末的桶狀干式紙質過濾器提供與之相應真空度.而原噴漆系統裝置中的真空負壓系統正好可以利用。
2) 將原有的恒溫烘箱和輸送鏈系統原則上作整體保留,只對這兩個系統作了局部的適應性改造和調整。由于噴過的油漆在烘箱內只是單純完成一個高溫固化(160℃±50℃)的作用,而噴過的塑粉在烘箱內則要在完成高溫流平的第一個程序后再完成第二個程序——高溫固化(185℃±5℃),這樣一來,只需對原恒溫烘箱的溫度上限作適當調整即可。輸送鏈系統因被輸送物沒有改變而無需進行改造 故該系統作整體保留。
3) 將原有的壓縮空氣系統及噴漆操作室外的水循環系統進行改造,改造的目的是使得這兩個系統能夠適應在新的工藝條件下進行正常工作。
4) 根據對現有資料和同類行業目前生產狀況的研究.我們發現了一個共性的問題由于設備自身及生產過程中種種原因的作用,使得生產時在真空過濾系統的出風處或多或少會有一些極微量的未被回收的塑粉被排入大氣,量雖不大,但同樣會造成資金的浪費和環境的污染。針對這一現象,我們準備在同行中率先嘗試將化工生產中常用的噴淋吸收塔加裝在真空過濾系統的出風口處,目的是對微量粉末進行再吸收。此舉從理論及我們的經驗來看都是完全可行的。
5) 擬購買的主要零部件:高壓靜電發生器,原料(塑粉)桶、桶狀干式紙質過濾器兩組(Φ300mm~450mm,10只),真空脈沖反吹切換控制系統,噴槍等。
三、改造方案的實施
實施經過在報請上級同意后,我們成立了專題項目小組對該技改項目進行系統的細化研究和具體部署,具體的改造步驟如下:
噴涂的前處理工序:我們只保留了原工序中的酸洗及其干燥部分。原因是我們利用同行的噴塑裝置對我們的待噴塑件進行多種工況下的多次試驗后得出了以下結論——在我們規定的工藝條件和原材料要求的情況下,待噴塑件可以不用進行磷化等工序而直接進行噴塑,其附著力的性能經相關權威部門的數次檢驗完全符合產品的要求。據此我們減去了前處理工序中除酸洗及干燥外的其他所有部分,帶來的好處顯而易見,既簡化了生產工序也降低了生產成本,同時對環境的保護也作出了貢獻。
噴漆操作室的改造:第一步,按預先擬定的想法,把操作室內的水幕及水循環系統全部拆除,保留操作室內的基本空間和真空負壓系統的主體部分后,對操作室的底板和后墻板進行了較大的改動。底板被改成了上大下小四棱錐狀,下面開300mm×300mm的粉末收集口,下置粉末收集槽。上大下小的四棱錐狀是為粉末的聚集而設計的。改動后的后墻板上增加了五副定位支架 上部增加了引風口。支架是為安裝桶狀干式紙質過濾器而設計,引風口是為安裝真空系統的動力源——引風機和風管而設計的。第二步,在操作室的右側角落安裝了噴粉系統.即:高壓靜電發生器、噴粉桶、噴槍和相關的電、氣路元器件,在操作室后上方的外側安裝了引風機、風管、真空脈 中反吹切換自動控制系統。至此,操作室的改造基本完成。
恒溫烘箱的改造:考慮到改造后烘箱的工作溫度較前有15%左右的提高,經測算,在適當的位置增加了兩組四根加熱棒(1500mm×600W,4根)。為了使烘箱內的溫度更加均勻,又在烘箱頂部的適當位置加了一臺擾流風扇。同時,為解決烘箱內檢修難和掉桶(噴涂件)難取的問題.在烘箱盡頭的底部加裝了個檢修人孔。改造后的烘箱在升溫速度和溫度均勻性等方面的性能達到了改造的預期要求。
輸送鏈系統因工件(被噴塑件)桶本身的幾何尺寸和重量均未變化,故無需對輸送鏈進行改動。我們原樣保留了該系統。
對微量粉末排空造成環境問題的治理事實上據我們所知在同行中,目前還沒有那家公司對這些微量排空的粉末進行處理。本著對公司和社會的雙重責任感,我們決定利用在化工企業積累的有關尾氣吸收的多種經驗來治理微量粉末排空而造成的環境問題。做法如下:在真空過濾系統排風口后增加一臺噴淋水洗尾氣吸收塔,該塔的具體參數如下:
塔種類:填料塔。填料為瓷環,堆碼形式為亂堆,噴淋液體為水,介質為含微量粉末的空氣(尾氣)。
塔徑:Φ600mm。
塔高:H=4600mm,填料段高度h=400mm,排空管高度:h1=2600mm。
噴淋用水實行循環使用,水循環系統中設計了一個蓄水池和一個沉淀池循環水先回到沉淀池進行沉淀后再通過過濾溢流到蓄水池待用。
至此,噴漆改噴塑的工程己基本完成。通過試生產檢驗,我們的預期目標全部實現。我們把兩年多實際生產中幾種主要耗材的消耗情況與技改前的噴漆作了對比,對比結果是,每年可節約66.36萬元。
下面是改造后的噴涂系統平面示意圖。
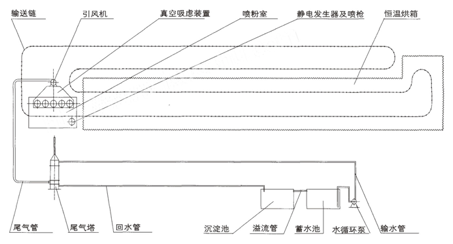
待完善的地方:目前噴涂操作室內待噴件的旋轉和噴粉操作還是人工進行的,我們希望下一步能改成全自動的,以便最大限度的降低成本和職工的勞動強度。
|