|
鋼桶底蓋拉深模具拉毛拉裂缺陷和消除方法
文/張航偉
冷沖壓深拉延模具在成形過程中容易產生拉毛缺陷,隨著生產的持續,模腔內溫度升高,拉毛缺陷不斷惡化,給品質和模具維護帶來極大困擾。
在冷沖壓生產過程中,部分深拉延零件由于拉延深度較深,模具內材料流動量大,導致模具型腔與材料之間摩擦力大,模具內溫度隨著沖次的增加不斷升高,如圖1 所示。

圖1 某深拉延模具溫度變化趨勢(南方地區夏季)
拉延模具間隙設置一般按料厚進行設計,溫度升高后,受熱脹冷縮影響,模具凸凹模間隙會減小。材料受到的模具壓力增加,摩擦力增加,模具進一步發熱,如此惡性循環,模具溫度會隨著生產的持續急速上升。在此過程中,模具中如有細小異物顆粒或模具表面研合不平,零件會出現拉毛缺陷,隨著生產的持續拉毛會不斷惡化,甚至造成零件開裂,如圖2 所示。溫度的升高也會造成材料機械性能的降低,相關研究表明,汽車用電鍍鋅鋼板的力學性能隨著溫度的升高而降低。因此,模具溫度的升高更容易造成深拉延時零件開裂。

圖2 零件拉毛缺陷和開裂缺陷
確認拉毛開裂原因
根據拉延模具特性,在深拉延零件發生拉毛或開裂時,應對拉毛和開裂的特性進行分析:⑴確認拉毛缺陷發生的時間,是在量產剛開始時,還是在量產一段時間后。如果是由于深拉延模具溫度升高導致的拉毛,發生階段一般在生產開始一段時間后,且隨著生產的持續而不斷惡化。⑵確認開裂產生的原因。若是由拉毛缺陷引起的,則該類開裂是在拉毛發生一段時間后,由于拉毛嚴重,拉痕深度超過了零件板料厚度,從而導致開裂,且此種開裂裂紋與拉毛位置重合。根據以上分析,可以快速找出造成拉毛及開裂問題的原因,即模具過熱。
確認模具高溫區域
利用紅外熱成像儀,在生產過程中對模具的溫度進行監控,找出深拉延模具上模、下模溫度最高的區域。紅外熱成像儀的監控要點為,生產過程中進行不停機動態拍攝,對模具剛開始生產至生產結束的全過程,每間隔200 件進行熱成像數據對比,如圖3 所示。

圖3 某模具熱成像圖
一般情況下,熱成像測量溫度最高的區域為拉延深度最深,且易出現拉毛缺陷的位置。將熱成像溫度最高的區域與拉毛開裂的區域進行對比,確認位置是否吻合。
靶向降溫
冷沖壓不同于熱沖壓,熱沖壓在模具內有冷卻系統,可以降低模具的溫度,冷沖壓只能自然冷卻。根據以上分析,我們需對模具過熱區域進行適當降溫,從而解決因為模具受熱導致的拉毛及開裂不良,也就是對冷沖壓模具增加降溫功能,降溫裝置如圖4 所示。

圖4 冷風裝置加裝示意
利用小型工業氣體冷卻器對模具局部進行降溫,可在模具筋板減重孔中進行氣路布置,利用壓機自帶的壓縮空氣提供氣源,對局部溫度高且零件拉毛嚴重的位置布置一到兩個冷卻器,冷卻器布置時需注意:最好上下模同時布置,以便快速降低模具溫度;一般要求壓縮空氣壓強為0.4MPa 以上,小型的冷卻器出口氣體溫度為零下10 攝氏度。生產時,壓縮空氣常開,冷卻器出口噴出零下10 攝氏度的壓縮空氣對周邊的模具型腔降溫,模具高溫區域的溫度得到抑制。根據紅外熱成像儀的測量,加裝前后模具最高溫差在(8 ~10)攝氏度,加裝的冷卻器如圖5 所示。
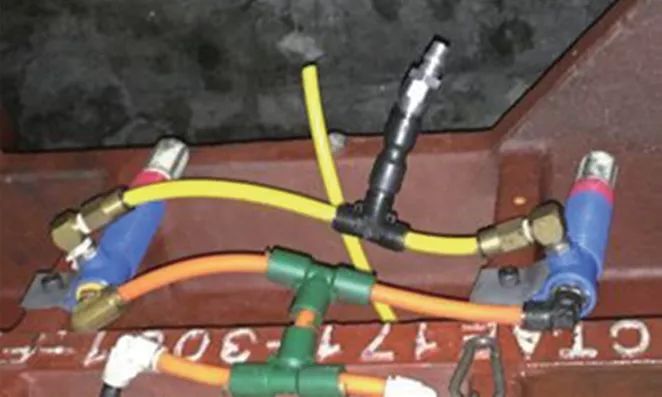
圖5 工業氣體冷風器加裝實際
效果跟蹤
加裝后確認模具高溫區域溫度已降低,在批量生產中可對冷卻器出口方向進行適當調整,保證冷卻器對模具高溫區域的有效降溫。加裝結果表明,拉毛情況得到了有效控制。
結束語
利用局部冷卻有效地控制模具溫度,使模具在批量生產時凸凹模間隙變化量減小,解決了模具因過熱造成的拉毛問題,當然,保證沖壓環境及板材的清潔、防止異物造成拉毛、保證模具研合良好、防止因研合不良造成的拉毛等其他措施可以同時展開實施。
|
|