鋼桶的涂裝與環境保護(2)
——在第五屆泛亞洲鋼桶行業會議上的演講論文
上海徐工涂料技術有限公司 徐國興
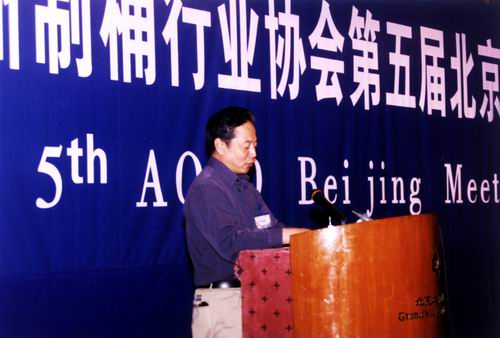
2.廢氣
鋼桶涂裝廢氣的來源主要是噴漆室和烘道的排氣。噴漆室的廢氣是噴漆室在排氣過程中產生的。為了保證良好的工作條件,噴漆室需要在 0.25~1.5米 / 秒的風速范圍內進行換氣,因此,噴漆室排出廢氣的特點是風量大,有機揮發物濃度極低 (大約在10~20ppm范圍內 )。噴漆室廢氣除含有有機揮發物氣體外,還含有—部分由于涂料過噴而形成的漆霧,這些漆霧的顆粒直徑大約在20 ~ 200微米左右。
烘道的排氣主要含有溶劑蒸氣、涂料成膜過程中熱分解氣體,還有使用氣體燃料或液體燃料燃燒所生成的廢氣。這類廢氣中的有害物質主要是苯類、酯類、醇類、醚類和酮類以及一些胺類及醛類等。
噴漆室和烘道廢氣的處理法有直接燃燒法、催化燃燒法、吸收法和活性炭吸附法等。
a.直接燃燒法
直接燃燒法是將噴漆及烘干過程中產生的廢氣引入燃燒室,直接與火焰接觸燃燒,把廢氣中的可燃成分燃燒分解,變成無臭無害的二氧化碳和水蒸氣的一種方法。
為了防止廢氣中的碳氫化合物由于不完全燃燒而生成一氧化碳,在燃燒室內,除供給充足的氧氣外,還必須要有650 ~ 800℃的燃燒溫度和0.5~1.0秒的廢氣滯留時間。
廢氣直接燃燒系統是由燒嘴,燃燒室,預熱器等部分組成的。為達到預期的燃燒效果,燒嘴要能形成連續穩定的完全燃燒的火焰,燃燒面積要大,并能使廢氣與火焰充分接觸。
直接燃燒法系統設計耍考慮以下幾點:
(1)因為噴漆廢氣是含有多種溶劑蒸氣的混合氣體,當其濃度接近爆炸極限值時進行燃燒,即會產生爆炸。所以為防止爆炸,對于接近爆炸極限值下限的高濃度氣體,需要用空氣稀釋到預定的安全度。
(2)直接燃燒怯處理噴漆和烘道產生的廢氣時,為避免光化學煙霧物質NOx的產生,燃燒溫度不宜超過800℃。
(4)要考慮余熱的利用。
直接燃燒法,管理容易,維護簡單,可靠性高。但需要的處理溫度高,耗費燃料多。
b.催化燃燒法
催化燃燒法是利用催化劑使廢氣中的有機溶劑蒸氣發生激烈氧化燃燒,生成水和二氧化碳,從而達到除去廢氣中的有害物的方法。
在將廢氣進行催化燃燒的過程中,廢氣由風機經管道送入熱交換器,將廢氣加熱到催化燃燒所需耍的起始溫度。經過預熱的廢氣,通過催化劑層使之燃燒。燃燒生成的高溫干凈氣體,可以在鋼桶烘道得到再利用。
由于催化劑的存在,催化燃燒法廢氣燃燒的起始溫度約為250~500℃,大大低于直接燃燒法的燃燒起始溫度650—800℃,因此不需要從外部供給大量的熱能,就能使廢氣進行完全燃燒。燃料的消耗遠比直接燃燒法為低。
催化燃燒系統由催化元件、催化燃燒室、熱交換器及安全控制裝置等部分組成,作為催化燃燒系統的核心部件—催化元件,外面是用不銹鋼制成的金屬框架,內部充填表面鍍有催化劑的金屬載體。催化劑多為白金系的貴重金屬,如鈀、鉑等。金屬載體制成各種形狀,有網狀、蜂窩狀、球狀,柱狀等。載體的材料多為鎳,鉻等耐熱合金及陶瓷等。
為了保證催化燃燒的正常進行,在設計催化燃燒系統時,需考慮以下幾點:
(1)廢氣濃度大小。廢氣濃度過低,燃燒效果差,若提高燃燒效果,勢必造成燃料的消耗,廢氣濃度過高,燃燒熱量大,升溫高,不僅會把催化劑燒壞,降低催化劑的使用壽命,而且處理不當,還會造成爆炸事故。廢氣中有機物的濃度最好維持在10一15克 / 米3 。
(2)要根據廢氣中所含不同的有機物的成分確定適宜的預熱溫度。預熱溫度過低,不能進行催化燃燒,預熱溫度過高,則造成燃料的浪費。由于廢氣所含成分不同,預熱溫度也不同,對于我們鋼桶行業常用的氨基烘漆所產生的有機揮發物,預熱溫度約為250 ~ 300℃;而對于環氧涂料所產生的有機揮發物,預熱溫度約為400—500℃。
(3)廢氣在催化劑層的滯留時間是影響廢氣處理效果的重要因素,滯留時間長,將會增加催化劑層的厚度,造成催化材料的浪費,滯留時間短,使廢氣處理不干凈。廢氣在催化劑層的滯留時間最好為0.14~0.24秒。
(4)要考慮充分的供氧條件。廢氣中的有機溶劑成分是通過催化劑產生強氧化反應,進行物質轉換而生成二氧化碳和水的,為此,要使燃燒充分進行,必須有充足的氧氣供應。若供氧不足,則不能完成廢氣凈化,而生成其他有害物質,如一氧化碳等,或在催化劑表面造成積炭,使催化劑活性下降。
(5)要考慮催化劑的中毒和活性衰退問題。從理論上講,在不存在外界污染的情況下,催化劑可以持續地使用,而實際上,水蒸氣、重金屬、塵埃、漆霧等的污染是不可避免的。這些污染造成催化劑中毒,輕者活性降低,重者完全喪失活性。因此,設計時,應盡量減少催化劑污染中毒,提高催化劑的使用壽命。催化劑中毒后,經再生處理,可以恢復其性能。
c.吸收法
吸收法一般是用液體作為吸收劑,使廢氣的有害成分在液體中被吸收的方法。
氣體用液體吸收劑的吸收過程,是由于氣體的分子擴散,通過氣相和液相的相間膜而發生的氣體物質的轉移傳質過程。其擴散轉移的推動力,在氣相界面膜處,是氣體分壓和在界面處的氣體分壓差,在液相界面膜處,是液相界面處的所溶氣體物質的濃度與液相中所溶氣體物質濃度差。在穩定吸收過程中,兩相界面處的液體中的溶質濃度和氣體中的溶質分壓,構成動平衡狀態。
從進行吸收法的原理和過程來看,作為吸收法的關鍵是選擇能把被吸收物質進行有效吸收的吸收劑。對于涂料施工過程中的廢氣,由于是多種有機揮發物的稀薄混合氣,選用吸收劑;是比較困難的。若廢氣中的主要成分是親水性溶劑,可用水作為吸收劑:若排氣中的主要成分是疏水性溶劑,則需要選用對此溶劑吸收效果好的吸收荊。
對于我們鋼桶行業來說,吸收法是不太實用的。我國鋼桶涂裝對環境污染最大的要算 PVF涂料了,不但是它的固體含量低,在烘烤過程中有占涂料用量 75 %以上的有機揮發物要跑到環境中去,而且由于揮發物的比重大、黏附性強,所以造成揮發霧氣在烘道附近久久不能排去,對人體和環境影響很大。PVF涂料烘烤過程中產生的霧氣是鄰苯二甲酸二甲酯的液滴微粒形式,所以不能叫做煙(煙是由固體微粒組成的)。對于這樣的霧氣,我們其實可用水作為吸收劑,不過在這里作為吸收劑就要打個引號了,因為水在這里的作用只是將鄰苯二甲酸二甲酯蒸汽冷卻凝聚下來罷了。
筆者曾經在實驗室做過用水噴淋冷凝鄰苯二甲酸二甲酯霧氣的實驗。將烘箱內烘烤 PVF涂料產生的鄰苯二甲酸二甲酯霧氣用水流負壓器(俗稱水老鼠)抽吸至水流中,烘烤過程未見有鄰苯二甲酸二甲酯蒸汽逃逸,而當實驗結束時,在水流負壓器下的儲水槽中發現了沉在水底的已經液化了的鄰苯二甲酸二甲酯。
所以我們在烘烤 PVF鋼桶時,是否能設計一個沖淋塔,將烘道中產生的霧氣抽出,使烘道保持負壓,負壓的大小以不至于使烘道熱能損失過多,又能使產生的霧氣無法逃逸發散為準。抽出的霧氣送至沖淋塔,從塔底由下而上,而水由上噴淋而下。為了使二者充分接觸,中間可設置多個塔板或填充大量小瓷環。這樣,在霧氣和水的上下流動接觸的過程中,在相間膜處,霧氣被水冷凝并被攜帶向下,使氣體得以凈化。干凈空氣由吸收塔上部排出,而含有鄰苯二甲酸二甲酯液體的水由噴淋塔下部流入水槽。由于鄰苯二甲酸二甲酯的比重達到 1.19,要比水高許多,被液化的鄰苯二甲酸二甲酯沉在水底,所以水槽上部可設有溢流口,溢流出來的水可循環利用,到時只需打開水槽的底閥將結存的鄰苯二甲酸二甲酯放出回收就行。
d,活性炭吸附法
其實除了用活性炭吸附,還可用活性鋁、硅膠、分子篩等吸附方法。其中分子篩的綜合吸收性能是最好的。但考慮到成本和鋼桶行業的實際情況,用活性炭吸附烘烤涂料的廢氣最實用。
活性炭是疏水性的,對有機溶劑有較高的吸附效率。另外,活性炭具有遠比其他吸附劑為高的比表面積,一般的為 500 ~ 1500米2/克。因此,在凈化有機溶劑廢氣中,多使用活性炭作為吸附劑。
活性炭由于制造的原料和活化的方法不同,有不同的比表面積和物理性質。一般情況下選用果殼類的顆粒狀活性炭效果好些。顆粒狀活性炭的粒徑,一般多為 5毫米左右。粒徑越小,雖然通過的阻力越大,但吸附效率越高。
來自噴漆室和烘道的廢氣,經過除塵器和冷卻器,除去漆霧、灰塵,并降低到一定溫度后,通過風機,從吸附塔的下部被送入吸附塔。在吸附塔內,廢氣中所含的有害成分,在活性炭龐大的固相表面被吸附濃縮,從而達到凈化廢氣的目的。凈化了的空氣,通過引風機被排入大氣。
隨著吸附過程的進行,活性炭逐漸失去吸附效能而達到飽和狀態,這時,通過與吸附塔上部連接的蒸汽管道,將蒸汽通入吸附塔內,使活性炭進行脫附,經脫附再生的活性炭可繼續使用。脫附后的水蒸氣及涂料有機揮發物蒸氣的混合氣進入冷凝器,使之冷卻,凝聚變為液體,流入分離器。在分離器內,將涂料有機揮發物液體同水進行分離,回收。
活性炭吸附塔的設計要注意:
(1)應設置預處理裝置,使廢氣在進入吸附塔之前,除去其中含有的漆霧,并降低至適宜的溫度,以提高活性炭的吸附效率。否則,由于活性炭表面被涂料顆粒覆蓋以及廢氣溫度較高而造成活性炭吸附率下降。
(2)應考慮防爆和防止活性炭層的自燃。
(3)應考慮恬性炭的再生和補充,以保證吸附過程的連續進行。
(4)應考慮布氣的均勻性,防止在吸附過程中溝流、偏流、短路等現象的發生,保證一定的吸附效率。
3,噴漆室和烘道廢漆殘渣的處理
噴漆室和烘道廢漆殘渣目前并沒有一個理想的處理方法。以前比較多的做法是掩埋和自行焚燒,但由于對土壤的污染以及經滲透后對水源對作物的污染,掩埋被不少國家所禁止;自行將這些廢漆殘渣焚燒,也是不可取的,因為沒有專門的燃燒設備是不可能將廢漆殘渣充分燃燒的,倒是會產生大量一氧化碳以及其他有毒物質污染環境。
不過現在很多地方的環保部門已經建造了集中的垃圾焚燒廠,這些焚燒廠會將垃圾分門別類,將可燃燒的垃圾集中燃燒,將垃圾變廢為寶成為寶貴的能源。經和當地環保部門聯系后,不少這類焚燒廠會定時上門收集需要焚燒的垃圾。
四,改善涂裝污染的途徑
現在鋼桶行業的效益都不是很好,但大多桶廠將精力花在管理、鋼材、涂料、能源等方面的降耗上,如果我們在降低涂裝污染中也能找到降耗增效的途徑,這不是利國、利民也利己的好事么。
1,前處理沖淋水的互換
如前文所說,我國鋼桶行業現在所使用的大多數去油液一般都是含有表面活性劑、氫氧化鈉、磷酸三鈉、碳酸鈉、硅酸鈉以及各類助劑的化學去油劑,呈偏堿性,所以去油后的循環利用的沖淋水時間長了,也就變為偏堿性的廢水,這時就需要更換沖淋用水了。
而大多數磷化液都是含有磷酸、磷酸鹽、硝酸鹽、鉬酸鹽以及各類助劑等的偏酸性液體,磷化后的循環利用的沖淋水時間長了也變為偏酸性的廢水了,這時再不換水的話就會影響涂料涂裝了。
這時,如果將這兩處的沖淋水互相換一下的話,就會出現意想不到的結果。
去油后的鋼桶表面,由于去油液的關系,本身也呈現偏堿性,若用呈偏酸性的含有少量磷化液的磷化后沖淋廢水沖淋后,不但部分中和了鋼桶表面的偏堿性,而且對后道的磷化工序也較為有利。
而在磷化后的鋼桶表面由于磷化液的關系呈偏酸性,若用偏堿性的去油后沖淋水沖淋,則部分中和了偏酸性的鋼桶磷化層表面。不過這里要注意一個問題,去油液的沖淋廢水中除了呈偏堿性外還含有從鋼桶表面清洗下的油脂,所以如果油脂含量較多的話就會造成鋼桶磷化表面的污染,就是去油液沖淋廢水中的油脂含量很低,也要再經清水的反復沖淋確信鋼桶磷化層表面干凈才行。
這樣的互換沖淋水廢水的再利用,既降低了污水的排放,又節約了用水。
2,改變涂料品種和噴涂方法
除了前處理,改善鋼桶涂裝污染的主要途徑有兩個,就是改變涂料品種和施工方法,從根木上消除或減少鋼桶涂裝有害物的產生。如將造成嚴重污染的溶劑型涂料,改變成水性涂料、粉末涂料或高固體分涂料,以消除或降低涂料有機揮發物對大氣的污染,采用高效的涂裝方法,提高涂料的利用率,減少涂料的飛散等。
鋼桶涂裝污染的主要來源就是涂料本身,而涂料對環境的最主要污染就是有機揮發物。但有機揮發物是溶劑型涂料的重要成分,所以從環保角度以及發展方向來看,水性漆和粉末涂料值得提倡。事實上有些桶廠已經在部分使用水性漆和粉末涂料了,甚至有的桶廠已經全部使用粉末涂料。當然,從目前鋼桶行業的生產需要來看,要想完全排拆溶劑型涂料是不可能的,我們所能做到的就是盡量使用高固體含量的溶劑型涂料,這是降低對大氣污染最直接、最經濟、最有效、最能立桿見影的途徑。而且這不但有利于環境保護,同時也是降耗增效的有效手段。
改變涂裝方法,改進噴涂裝置,也是提高涂料涂覆效率、減少漆霧飛散有效手段。我們可以從我們鋼桶行業最常用的三種噴涂方法的比較來分析:
空氣噴涂借助于壓縮空氣氣流所造成的負壓把涂料帶出并經噴槍分散成霧狀,噴射于鋼桶表面。空氣噴涂的漆霧是由氣流帶出的,漆霧中混有大量的空氣,這就造成了涂料隨氣流擴散的弊病,并且,涂料中的有機揮發物由于氣流的擴散,更加快了揮發速度。所以空氣噴涂是涂料噴涂的幾種方法中對環境污染最大,對涂料的浪費也是最大的一種方法。
高壓無氣噴涂是靠密閉容器內的高壓活塞將高壓施加于涂料,獲得高壓的涂料通過高壓軟管、噴槍,經橄欖形的噴嘴孔將壓力能轉換成速度能,使涂料霧化成微粒噴到鋼桶表面。與空氣噴涂相比,由于漆霧中不含有大量的空氣,不會形成涂料隨氣流飛濺的現象,涂料的利用率顯著提高,對環境的污染也大為減少。并且由于高壓無氣噴涂可以噴涂相對空氣噴涂粘度高得多的涂料,噴涂中使用的稀釋劑可以減少,這也降低了對環境的污染,當然更降低了涂裝成本。
相對以上兩種噴涂方法,靜電噴涂對環境的污染是最小的。靜電噴涂是將高壓靜電發生器發生的負高壓電接加在金屬銳邊或尖端放電的噴槍電極上,而鋼桶則通過懸掛鏈或其他傳送裝置接地,使負極與鋼桶之間形成一個不均勻的靜電場。靠電暈現象,首先在負電極(噴杯)附近激發游離出大量的電子,漆霧進入電場后與電子結合成負電粒子,在電場力的作用下,定向地飛向帶正電荷的鋼桶表面。靜電噴涂不會或很少有漆霧飛散到空氣中去,這是幾種噴涂方法中對環境污染最小的主要原因。如果能在噴房內的鋼桶后面及兩旁裝有用漆包線繞成的帶有負電的直流高壓電網,那么由于對同樣也帶有負電的漆霧的排斥作用,噴房內壁也不會沾染漆霧。
減少鋼桶涂裝對環境污染的方法還有很多,例如,我們鋼桶行業現在使用的涂料,除了硝基漆和常溫快干的X-891涂料之外,大多數均可通過加熱降低粘度(如X-622環氧類的鋼桶專用內涂料,將溫度從 25℃提高到 40℃,粘度可下降 20 %左右),這樣就可減少甚至不用稀釋劑來噴涂涂料;在噴涂中,特別是空氣噴涂中使用線形小噴角的噴嘴可減少漆霧的飛濺;使用高質量的噴涂裝置也可使漆霧更加細化,飛散更少,涂裝效果也更好。
只要我們思想重視,鋼桶涂裝對環境的污染必定會降至最低,涂裝的涂料單耗必定也會降至最低,鋼桶的涂裝質量也會更好。
|