談鋼桶的表面處理(1)
上海徐工涂料技術有限公司 徐國興
“鋼桶,特別是冷軋板制成的鋼桶,在涂漆之前,前處理與否,油漆附著力可相差數百倍”。這是中日合資帕卡瀨精(Parkv Rizing)有限公司日方技術人員,在上海商檢局組織的“鋼桶脫脂、磷化業務洽談現場操作”會議上表述的論點。筆者認為,這不是為了商業需要的夸大。試想,質量再高,附著力再強的油漆,涂在一層防銹油上,怎么會牢固呢?與涂‘在具有良疑棗處理表面的鋼桶上相比,附著力怎能不相差數百倍呢!我們用冷軋板制成的鋼桶,未經表面處理涂上了油漆,裝運時繩子一拉,油漆拉下一片,就是明顯的例子。
有人說,在熱軋板制成的鋼桶上,油漆附著力是很好的。的確,熱軋板制成的鋼桶表面具有較好的粗糙度,且由熱軋高溫形成的氧化皮與基磷尊合牢固,所以在一段不長的時間內,在未經表面處理的熱軋板制成的鋼桶上,油漆附著力確實不錯。請注意!這只是在一段不長的時間內。鋼桶廠的人都知道,熱軋板制成的鋼桶未經表面處理外放置一段時間,就開始出現油漆剝落,銹跡斑斑的現象。這就是沒經過表面處理的結果。相比之下,經表面處理的鋼桶就是用舊了,碰破了,卻不生銹,油漆也不脫落。國外的鋼桶廠表面處理車間的面積要占到全廠面積的三分之二左右,可見其對前處理的重視程度。
在國內外市場變幻莫測的今天,爭奪市場已成為余球廠商最關注的焦點。然而,爭奪市場,要靠一流的產品,一流的質量,一流的包裝。對鋼桶來說,它是別的產品的包裝,而涂漆c不管是內涂,還是外涂,則是包裝的包裝。它是直觀的第一印象,也是保護鋼桶不受銹蝕,延長使用壽命,保證內裝物品質關鍵。所以,一定要重視鋼桶的漆前處理。以下,我們分三個方面進行探討。
一、鐵的表面性質
暴露在大氣中的金屬表面,不可避免地要受到氧、二氧化碳、二氧化硫、硫化氫、水、氨,等氣體的腐蝕。腐蝕是普遍存在的現象。在給定的狀態下,金屬能否自發地轉化為另一狀態——即腐蝕產物,其先決條件是產生化學反應,伴隨能量的釋放。若轉化反應釋放能量,則此金屬處于熱力學的不穩定狀態。該反應具有熱力學推動力,腐蝕可自發進行。若轉化反應需供給能量,則此金屬處于熱力學的穩定狀態。該反應不具有熱力學推動力,腐蝕不能自發進行。包括鐵在內的大部分金屬都處于熱力學的不穩定狀態,都具有熱力學推動力,所以都不可避免地要受到腐蝕。鋼桶用鋼板的腐蝕介質是水和氧,其反應過程如下:

鋼板受空氣的侵蝕,會使表面氧化。這是由于鋼板表面的鐵原子奪取空氣中的氧原子而生商?的氧化物,附在鐵基體的表面,俗稱鐵銹。在高溫下,鋼鐵材料更易與氧結合,鋼桶用熱軋板就具有經高溫氧化的氧化皮。
1,熱軋板
鐵氧化物的厚度和構成,隨著溫度的不同而不同。在高于900℃時形成鐵磷狀,其質硬脆,與鐵基體具有較好的結合力,而且成三層結構:外層主要由含氧31.9%的三氧化二鐵構成。此層的厚度在軋制一晝夜時為氧化皮總厚度的4%左右;中間層主要由含氧為27.6%的四氧化三鐵構成。此層厚度在軋制一晝夜時為氧化皮總厚度的36%左右;其余的60%為內層即直接靠近鐵基體的部分,由含氧為22.2%的氧化亞鐵構成。
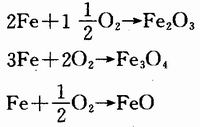
因鋼桶用的熱軋板是在高于900℃的溫度下軋制成的,所以它的氧化皮由通稱為無水氧化鐵的三氧化二鐵、四氧化三鐵、氧化亞鐵構成。它呈黑藍色與鐵基體有較好的結合力。但是,當遇到空氣中的潮氣(即水份)時,無水氧化鐵就逐漸轉化為氫氧化鐵。油漆所用的溶劑均含有一定的水份。如:拷部標生產的醋酸乙酯含水O,3一o.7%,即使試劑級的醋酸丁酯含水也達O,1%左右。因漆膜存在大量的微孔,這些微孔使得漆膜下的氧化鐵能與大氣溝通,所以即使在無水氧化鐵表面涂上油漆,時間一長,無水氧化鐵也會變成氫氧化鐵。在氫氧化鐵生成過程中,其體積成倍增長。原來的無水氧化鐵發生層與層之間的裂變,從而破壞了與鐵基體的牢固結合。最后,成片殼起,脫落,附于其上的油漆層也隨之脫落,使得垮基體銹跡斑斑。還有,由于電位的不同在水份透過漆膜微孔進入鐵基表面情況下,氧化亞鐵、眵零化三鐵和金屬鐵能形成腐蝕電池,在涂層下很快腐蝕鐵基體,加速了涂層的脫落。前文所說,油漆涂在未經前處理的熱軋板制成的鋼桶表面,在一段時間內附著力不錯,這一段時間就是指無水氧化鐵未轉化成氫氧化鐵的那一段時間。一旦氫氧化鐵轉化過程開始,則油漆層的破壞也就開始,鋼桶的銹蝕也就開始了。所以,對于熱軋板鋼桶,漆前有必要除去氧化皮,并進行磷化處理。
2.冷軋板
冷軋板是在低于鐵金屬的結晶溫度,使鐵金屬產生塑性變形而制成的無銹的鋼板。為了防銹,在其表面涂有防銹油。此防銹油是基礎油(主要成份為礦物油、植物油、動物油等)中添加緩蝕劑和各種用途的輔助劑(如抗氧劑、增粘劑、降凝劑、助溶劑等)構成的。在一定時期內,防銹油可保護冷軋板不被銹蝕,但給油漆施工帶來了麻煩。若不去除此層防銹油,由于冷軋板基體較光滑,油漆附著力不好,況且,鐵基體通過漆膜微孔與外界的水份、氧氣接觸,也會生成體積成倍增大,結構較松散的氫氧化鐵,從而也會破壞漆膜,使鐵基體銹蝕。所以,對于冷軋板鋼桶在漆前去除防銹油后,一定要進行磷化處理。國外的桶廠與鋼鐵廠的供貨時間銜接得很好,如日本桶廠,在制桶的當天,由鋼鐵廠將剛軋制好的無,防銹油的冷軋板定時、定量送到,桶廠馬上制成桶,馬上進行除污和磷化,再行油漆,所以可以省去除油這一工序。
二、漆前處理
涂漆質量的好壞與漆前處理的質量關系很大。一般來說,我們鋼桶的漆前處理,對熱軋板鋼桶來說,需進行去除氧化皮(除銹)和磷化;對冷軋板鋼桶來說需進行去油和磷化。
1.除銹
除銹就是除去鋼桶表面的銹跡、氧化皮及各種腐蝕產物。對于鋼桶除銹來說,常用的方法:手工除銹、機械除銹和化學除銹等。
(l)手工除銹
手工除銹對于鋼桶來說:就是用鋼絲刷、砂布等工具除銹。勞強度大,效率低,質量差,適用于產量低的小型鋼桶廠。
(2)機械除銹
機械除銹是用壓縮空氣或機械動力將丸料(如石英砂、鋼丸、鐵丸、鋼絲段、玻璃珠等)從噴咀高速噴出或經高速旋轉葉輪打擊在鋼桶表面,借沖擊、切削、磨刷等作用力除去銹跡和氧化皮,同時也可去除鋼桶表面毛刺、飛邊和焊渣等。這種方法可使鋼桶表面得到不同程度的粗糙度。適宜的粗糙度能增加涂層和金屬的實際接觸面積并提高附著力,但是粗糙增加到一定限度時,則鋼桶鐵基表面的內應力增加,甚至可能形成小裂紋,從而損害了鋼桶的強度。一般來說,適用于鋼桶的機械除銹有噴砂、噴丸、拋丸等。
①噴砂:噴砂用的砂子要求有足夠的硬度,不能混有油污,、泥土或石灰質。一般采用粒度在1-2mm左右的石英砂,干濕均可。噴射距離在0.5m,噴射角度45°-8O°為好,噴射用壓縮空氣為O.4一O.6MPa。
②噴丸:一般可用O.2~lmm粒徑的鐵丸或鋼丸。噴射距離為O.2-0.5m,噴射角度為30°-90°,噴射用壓縮空氣為O.2-0.6MPa。
以上二法,可根據銹蝕的程度調整噴射壓力和角度。噴砂和噴丸能獲得比較光亮和紋理較為細密的鋼桶表面,但是由于噴砂和噴丸過程中產生大量的砂塵,嚴重影響操作工人的健康;并污染環境。由于鋼桶表面會沉積較多的灰塵,在磷化前還需進行除灰,所以此二法的應用受到了一定的限制。(噴砂機和噴丸機可定做)。
③拋丸:拋丸法是利用高速回轉的葉輪將彈丸從拋丸器的葉片中甩拋到鋼桶表面的除銹方法。此法效率高,質量好,動力消耗少,對于鋼桶的機械除銹是個值得推薦的方法。
另外,若條件許可,也可以采用高壓水噴射除銹,但此種方法較不易掌燎?尤其是高壓水壓力的調節,需視鋼桶表面的銹蝕程度而定。壓力太小除不掉銹,壓力太大鋼桶會變形,一般水壓在20-75MPa范圍內。
(3)化學除銹
化學除銹主要是利用酸性溶液與鋼桶表面的氧化物發生化學反應,使其溶解在酸性溶液中,以達到去除銹跡和氧化皮的目的。一般常用的酸性溶液有硫酸、鹽酸、磷酸等無機酸和檸檬酸、酒石酸等有機酸。由于有機酸反應較慢,且還易產生其它副反應,所以用于除銹的多為無機酸。
當酸與鋼桶表面氧化皮反應時,在溶解氧化鐵的同時,還透過疏松了的氧化皮孔隙和裂紋,使鐵基體也部分地發生溶解,并折出氫。由于氫的自由壓力,對沒溶解而已相當疏松的氧化皮,起到了從基體表面剝離的作用.氫的產生還起著對氧化鐵的還原作用,可使不易于溶于酸的磁性氧化鐵,還原成易與酸作用的氧化亞鐵或純鐵,加速下酸洗除銹過程。
一般來說,使用硫酸、鹽酸等強酸都能達到除去氧化皮的目的。鹽酸具有溶解氧化物能力大,溶解溫度低(40℃以下),除銹速度較’決的優點,但也存在酸耗量較大,經常要調換,易放出有害的氯化氫氣體的缺點。磷酸酸洗除銹能對鋼鐵形成具有一定防蝕能力的保護膜,但除銹能力不如硫酸和鹽酸,因此酸耗很大。由于其價格相對較高,所以不適宜作為大批量的除銹酸液,但可作為有特殊要求的處理液組份。
硫酸溶液與鐵氧化物生成氫的量要大于鹽酸。25%濃度的硫酸酸洗除銹的速度最快.一般使用的濃度在20%以內,過高的濃度能使金屬過蝕。用硫酸除銹,成本較低,揮發較少。當溫度提高時,在低濃度時也能進行除銹,而且能加快除銹速度。但是,若時間控制不當,即使加入緩蝕劑,也能使鋼鐵產生過蝕。
常用無機酸酸洗除銹方法的比較:
酸的種類 |
優點 |
缺點 |
使用條件 |
硫酸 |
1、成本低。
2、當濃度低時可提高溫度保持原有除銹力。 |
1、溫度高易造成氫脆和過蝕。
2、處理時間比鹽酸長。 |
1、濃度5-25%。
2、溫度60-80度。
3、10%酸液中二價鐵110g/L以下有效。 |
鹽酸 |
1、除銹速度快。
2、氫脆影響比硫酸小。
3、可在常溫下酸洗。 |
1、易放出氯化氫刺激味大。
2、酸耗量較大經常要調換。 |
1、濃度15-20%。
2、溫度:常溫-40度。
3、二價鐵含量130-150g/L以下有效。 |
磷酸 |
1、不會產生過蝕或氫脆。
2、可形成有一定防蝕力的保護膜。 |
1、成本較高。
2、重銹不易去除。
3、酸液去銹效力下降快。 |
1、濃度15-20%。
2、溫度40-80度。
3、二價鐵含量30g/L以下除銹效果好。 |
硫酸酸洗化學反應如下:
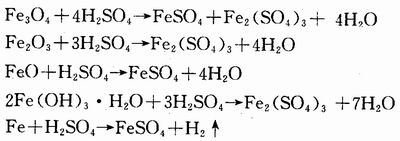
(4)化學除銹液的添加劑
在化學酸洗過程中,有較多的氫氣析出,特別是當酸直接與鐵金屬基體反應時氫氣的產生更為劇烈。這個過程使酸耗及金屬損失過多,金屬酸洗也因氣泡的產生而不均勻。由于氫離子擴散至金屬內部,導致金屬的物理性能變化,產生脆性,降低了韌性和延展性,這就是“氫脆”現象。析出較多的氫氣易造成污染和危險。此外,在酸液過濃或酸洗時間控制不當時也易引起金屬的過蝕。
為了改善上述情況,應在酸液中加入緩蝕劑。
一般認為緩蝕劑是具有較大帶正電荷分子的膠體顆粒物質,能在鐵金屬基體表面形成一層吸附膜或難溶的保護膜,從而阻止酸與鐵金屬的繼續反應而達到緩蝕。由于氧化皮和銹銹表面不具極性,所以不會產生這種保護膜,因而緩蝕劑的加入只對鐵金屬基體產生緩蝕作用,而酸液與氧化皮及鐵銹的反應是照常進行的。
緩蝕劑的加入增大了作為陰極的鐵金屬基體的氫超電壓,抑制了氫氣的過量產生,使基體金屬受到保護,改善了氫脆和酸霧的飛逸,降低了酸耗,礴少了酸洗設備的腐蝕。
緩蝕劑的種類較多,主要有硫脲、若丁、烏洛托品等。其中以若丁的緩蝕作用最高,但只適用于酸洗周期較短的過程。應用較廣的為硫脲。硫脲的添加量為硫酸量的0.05~0.1%。
另外,為了酸液的熱穩定及加快酸洗過程,還可在酸液中加入1-6%的潤濕劑如平平加、601洗滌劑等。
①硫酸質量:一般比重在1.75-1.84左右。若砷、二氧化硫、硫化氫等雜質過多,會降低酸洗速度,加速氫向鐵金屬基體的擴散,從而加劇鐵金屬的氫脆。
②酸洗液的配制:先按槽容量的3/4放入水量的60%左右再緩慢加入硫酸,最后稀釋至規定濃度。緩蝕劑和潤濕劑需先用水調好后再加入。當酸洗溫度在50-70℃之間時,硫酸的濃度可在10~25%之間選擇,濃度過低或過高都會減慢酸洗速度。當硫酸濃度高于85%左右時,硫酸與金屬基體不起反應了,所以濃硫酸可以用鐵制容器貯運。酸液的補充可通過酸堿滴定測得硫酸的濃度來確定,也可按當硫酸濃度為is%,溫度為60-70℃時,每酸洗100-160m2熱軋板鋼桶耗用30~60kg濃硫酸來估算。
⑧硫酸酸洗除銹工藝
硫酸酸洗除銹工藝可采用噴射法和浸漬法。為了安全和節約投資,國內鋼桶行業一般采用浸漬法。鋼桶置于塑料網籃中,塑料網籃吊于可移動的吊車上,這樣就可把鋼桶浸入酸洗液中。除銹后,再依次進入后面的靜水槽及再后面的流動水槽清洗,然后進入最后的磷化工序。酸洗槽大多為鋼板焊制,內襯塑料或玻璃鋼。酸洗時間視銹蝕程度而定,一般為5~15分鐘。
排放沖淋的酸性廢水和廢酸液時一定要用堿中和到PH接近7左右。
|