國內典型的鋼桶生產工藝流程是什么樣的?
文/楊柳
問:
國內典型的鋼桶生產工藝流程是什么樣的?
答:
鋼桶生產的工藝流程各家都有所不同,主要與生產工藝、設備、產量、產品結構、質量要求等有關。大體上典型的生產工藝流程都差不多。我們以實例介紹一下。這是某產品為200升鋼桶和中小型鋼桶的企業,生產工藝在國內屬于比較典型的情況。僅供參考。
一、工藝流程圖
200升鋼桶生產工藝與中小型鋼桶生產工藝相比,減少底蓋內表面噴涂及烘干工序和桶身內表面噴涂及烘干工序,其它工序均相同,具體見圖1 和圖2。
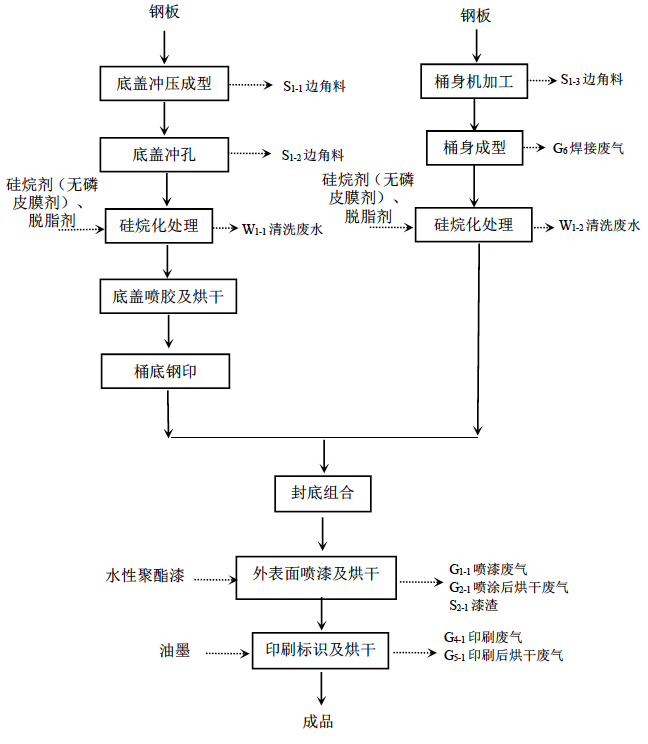
圖1?典型200升鋼桶工藝流程圖

圖2 典型中小型鋼桶工藝流程圖
二、工藝流程說明
1、底蓋沖壓成型、底蓋沖孔:
將外購的鋼板在底蓋預卷機、沖床、蓋自動沖孔線等設備上沖壓成型,和沖孔,形成桶的底和蓋的毛坯。該過程產生邊角料。
2、硅烷化處理:
硅烷化處理是指以有機硅烷水溶液為主要成分對金屬表面進行處理,以達到防腐和增加油漆結合力的作用的處理方法。本項目硅烷化處理包括預處理和硅烷化處理兩個階段。
a. 預處理:本項目預處理工序包括預脫脂、脫脂和清洗三個過程。預脫脂和脫脂均采用脫脂液和水按1:4 的比例配比的脫脂液噴淋處理。預脫脂和脫脂均配套脫脂槽(有效容積5m3)和配槽(有效容積3m3),工件置于脫脂槽中噴淋脫脂,噴淋液儲備在配槽中,脫脂槽收集的脫脂液回到配槽循環使用。通過檢測和控制游離堿度添加和控制槽液濃度,脫脂槽定期清理槽渣,脫脂液定期添加,不排放。
脫脂后的工件采用三級逆流淋洗,每一級設置1 個5m3 的淋洗槽和1 個3m3的配槽,工件放在淋洗槽內用噴淋裝置噴淋清洗,噴淋清洗水源儲備在配槽中。三級淋洗的廢水進入二級淋洗的配槽,二級淋洗的廢水進入一級淋洗的配槽,一級淋洗的廢水進入污水處理站的調節池。
b. 硅烷化處理:本項目擬設置2 個體積為6m3 的硅烷化處理槽,脫脂清洗后的工件由載帶運至硅烷化處理槽內,后用硅烷劑(無磷皮膜劑)(硅烷10~40%,防銹添加劑1~5%,水55%~89%)和水配比(1:3)的硅烷化處理液噴淋。工件由載帶自動連續運輸,在噴淋區的停留時間約為60s。硅烷化處理液經硅烷化處理槽收集后循環使用,根據pH 值(控制在8.0~9.5)或者游離堿的點數不定期添加。硅烷化處理槽定期清理槽渣,硅烷化處理液定期添加,不排放。
3、底蓋內表面噴涂及烘干:
在底蓋內表面噴涂系統中完成。本項目底蓋內噴涂系統包括水簾噴房+烘道,工件經載帶自動連續運至噴房內的噴涂工位后自動噴涂。噴房設置移門,工作時移門關閉,工件進口端設置負壓風幕,工件出口端與烘道進口端緊密連接。噴涂后的工件自動輸送至烘道,在160℃的條件下烘干30min左右,烘道通過天然氣燃燒加熱。噴涂過程產生噴漆廢氣、漆渣;烘干過程產生烘干廢氣和天然氣燃燒廢氣。
4、底蓋噴膠及烘干:
內表面噴涂并烘干后的底蓋,利用底蓋噴膠設備在邊緣噴填一圈密封膠,以用于底蓋和桶身的封合粘結。噴填好密封膠的底蓋進入膠水烘干烘道,在100℃溫度下烘干約5min,烘道使用天然氣燃燒加熱。本項目擬采用的密封膠主要成分為天然乳膠、高嶺土、重晶石、防老劑、促進劑、蒸餾水,在噴填及后續烘干過程中基本不會有廢氣產生。該過程產生天然氣燃燒廢氣。
5、桶身機加工、桶身成型:
將外購的鋼板在剪板機上剪切成所需的尺寸,然后在通過全自動縫焊機、預漲型機等設備進行成型工序。桶身機加工過程產生邊角料;桶身成型過程產生焊接煙塵。
6、桶身硅烷化處理:
桶身表面硅烷化處理和底蓋硅烷化處理的工藝完全一致,此處不再贅述。
7、桶身內表面噴涂及烘干:
桶身內表面噴涂及烘干和底蓋內表面噴涂及烘干的工藝完全一致,此處不再贅述。
8、封底組合:
先利用底蓋預裝配機、縫焊機將經前述處理的底、蓋和桶身組裝起來,再利用封底蓋機密封組合。
9、外表面噴漆及烘干:
在外表面噴涂系統中完成,具體工藝與內表面噴涂完全一致,此處不再贅述。
10、印刷標識及烘干:
利用自動絲印機在桶身和桶蓋的外壁印刷用戶產品標識,然后在油墨烘道內烘干,烘道溫度100℃左右,烘干時間約10min,烘道采用天然氣燃燒加熱。該過程產生印刷廢氣、印刷后烘干廢氣和天然氣燃燒廢氣。同時,印刷機定期用清洗液清洗產生清洗廢液。
|