《金屬包裝設計與制造》(24)
金屬包裝制造常見模具結構
文/吳若梅、劉躍軍
在金屬包裝容器的成型、制造過程中,大都需要模具的輔助。隨著工業的發展和科技的進步,社會對金屬包裝容器的要求也越來越高,因此模具在設計、材料、生產、使用等各方面都發生了很大變化。本節對現在應用最廣泛的沖裁模、彎曲模和拉深模及其典型結構做了詳細分析;對在金屬包裝容器制造過程中起到重要作用的翻邊、縮口、脹形、整形等模具也做了簡單介紹。
一、沖栽模
1、單工序沖裁模
單工序沖裁模是指即在一副模具中只完成一種工序,如落料、沖孔。由于落料和沖孔在沖裁工藝中僅僅是取舍部分不同,而模具工作原理大致相同。下面以無導向落料模為例,介紹落料模的工作流程、原理及特點。
如圖11-2所示為無導向落料模。沖裁(落料)工序開始時,首先利用導料板4及定位板7將坯料定位,之后在沖壓力作用下進行沖裁,在凸模推力的作用下,從壞料上分離下來的沖裁件直接從凹模洞口落下,環繞在凸模上的廢料由固定卸料板3脫下,完成落料工作。這種落料模的特點是上、下模均無導向裝置,沖裁位置由機床滑塊的導向精度決定,結構簡單,制造難度較低。此類模具的缺點是安裝調試比較困難,條料排樣形式局限較大,操作也不夠安全,僅適用于沖裁精度要求不高、形狀簡單和生產批最小的沖裁件。

與無導向落料模相比,固定導板導向落料模和導柱導向落料模均對壓還位置及上下模的運動做了精確導向,沖裁精度高,安裝方便,但制造成本較高,適用于生產批址較大、精度要求較高的制件。
2、復合沖裁模
復合沖裁模在結構上最主要的特征是:存在一個零件具備凸模和凹模兩個零件的功能,稱之為凸凹模。如在落料沖孔復合模中既作為落料凸模又作為沖孔凹模的零件就是凸凹模。如圖11-3所示為沖孔落料復合模的基本結構。落料凹模與沖孔凸模均安裝在下模,凸凹模安裝在上模。沖裁開始時,隨著上模的下降,凸凹模的外側刃口與落料凹模配合工作,完成落料工序;同時,凸凹模的內側刃口與沖孔凸模配合工作,完成沖孔工序。

根據凸凹模在模具中的裝配位置不同,通常將復合模分為正裝式復合模和倒裝式復合模兩種。凸凹模裝在上模的稱為正裝式復合模,凸凹模裝在下模的稱為倒裝式復合模。
如圖11-4所示為落料沖孔倒裝復合模。凸凹模21安裝在下模上,沖孔凸模16和落料凹模7安裝在上模上。還料由定位銷6(兩個導料銷和一個擋料銷)定位,沖裁時,上模向下運動,因彈性卸料板5和安裝在凹模型孔內的推件板20分別高出凸凹模和落料凹模的工作面約0.5mm, 且落料凹模7上與定位銷對應的部位加工出了凹窩,坯料首先被壓緊。隨著上模的繼續下降,沖孔、落料兩個工序同時完成。此時,沖下的工件卡在凹模孔內、沖孔廢料在凸凹模的型孔內積聚,坯料箍緊在凸凹模上,而彈簧4被壓縮,彈性卸料板5相對凸凹模的上表面向下移動了一個工作距離。上模回程時,被壓縮的彈簧回彈,推動卸料板向上移動復位,同時將雛緊在凸凹模上的還料脫卸。卡在凹模孔內的工件,借助打料橫桿(隨滑塊一起上下運動)與擋頭螺釘(固定在壓力機的機身上)之間的撞擊力,被打桿12、推板13、推桿15和推件板20組成的剛性推件裝置推出。在下一次沖裁行程時,凸模的推壓將積聚在凸凹模型孔中的沖孔廢料推出,從而實現逐個自然漏料。

采用倒裝復合模,廢料能直接從壓力機工作臺孔中落下,具有操作方便、安全可靠等優點,且生產效率較高,故被廣泛應用。
3、帶齒圈壓板的沖裁模
在沖裁工藝中,還經常采用精密沖裁、半精密沖裁或整修等方法,以獲得尺寸精度更高、斷面更光潔、垂直度更高的沖裁件。其中,精密沖裁又稱為齒圈壓板沖裁法。這種沖栽方法與普通沖裁在工藝上相同,但是模具存在以下差別:
①凸、凹模間隙極小;
②凹模刃口位置帶圓角;
③在模具結構上比普通沖裁模多裝一個齒圈壓板和一個頂出器。
其工藝流程如圖11-5所示。
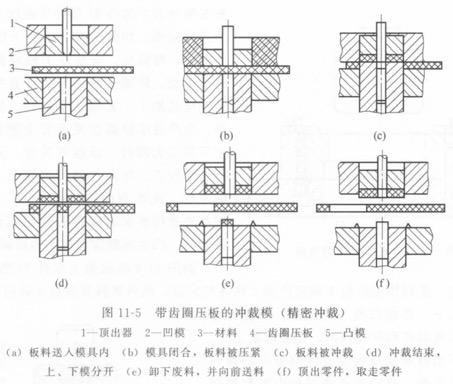
精密沖裁在提高沖栽周界塑性的同時,還大幅度降低了還料剪切區的拉應力。同時,由于凹模刃口為圓角,消除了應力集中,從而大大降低了因拉應力產生撕裂斷面的概率。此外,頂出器的存在能防止弓彎現象的產生,故能得到沖栽面光亮、錐度小、平整而精度高的工件。
二、彎曲模
金屬材料的彎曲主要通過模具及其裝備來完成,彎曲件的形狀及彎曲工序的安排決定了彎曲模的結構。金屬包裝材料幾乎涵蓋了所有類型的彎曲件,如鋼桶桶身的滾彎件、提手的折彎件等。由于彎曲件的種類很多,形狀不一,因此彎曲模的結構類型也是多種多樣的。
1、V形件彎曲模
如圖11-6所示為V形件彎曲模的基本結構。

零件3為凸模,由銷釘2固定在標準槽形模柄1上。凹模5通過螺釘和銷釘直接固定在下模座上。彎曲工序開始時,還料由定位板4定位。頂件裝置由頂桿6和彈簧7組成,其主要作用有:
①在彎曲過程中壓住蚽料防止還料位置偏移;
②回程時將彎曲件從凹模內頂出。
該模具的特點是結構簡單,便于安裝及調試,對坯料厚度的公差要求不高。適用于加工兩直邊相等的V形件,在彎曲終了時可利用頂件裝置對彎曲件進行一定程度的校正,回彈較小。
2、U形件彎曲模
根據彎曲后彎曲件的推出位置,可將U形件彎曲模分為下出件U形件彎曲模與上出件U形件彎曲模。如圖11-7所示為下出件U形件彎曲模,彎曲后,安裝在上模座的凸模繼續往下運動,將加工后的彎曲件直接從下模座的凹模孔推下,無須手工取件,模具結構簡單,生產效率較高且便于安全操作。但是由于下模座無頂桿、頂板等裝置,因而無法進行彎曲校正,彎曲件的回彈較大,底部也不夠平整。此類彎曲模可用千加工高度較小、底部平整度要求不高的小型U 形件。彎曲半徑和凸、凹模間隙應取較小值以減小回彈。
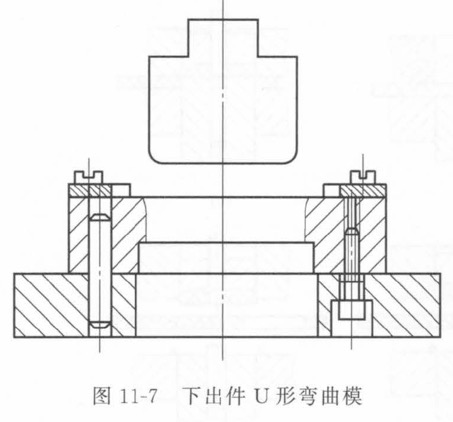
如圖11-8所示為上出件U形件彎曲模,彎曲開始時,先利用定位板4和定位銷2將還料定位,然后蚽料及頂板3被向下運動的凸模1同時壓下,并在凹模5內成形。回程時彎曲后彎曲件被頂桿和頂板頂出,完成彎曲工作。該模具與下出件彎曲模的主要區別是在凹模內設置了頂件裝置,再冷的彎曲過程中坯料被頂板緊緊壓住了,從而保證了彎曲件底部的平整。此外,頂板上還配備定位銷2,可利用坯料上的預留孔、工藝孔進行二次定位,即使U形件兩直邊高度不同,也能保證彎邊高度尺寸。

3、圓形件彎曲模
圓形彎曲件可根據尺寸大小進行分類,通常直徑小于5mm的屬小圓形件,直徑大于20mm的屬大圓形件。采用模具彎曲方法加工圓形件通常只限于中小型圓形件(注意:包括小圓形件和大圓形件),直徑較大的大型圓形件通常采用滾彎成形(鋼棍加工、無模具)。
小圓形件的加工方法通常是先將還料彎成U形,然后再彎成圓形;大圓形件通常采用三道彎曲工序或兩道彎曲工序彎曲成圓。加工直徑介于5mm和20mm之間的圓形件,可根據材料性質、彎曲件質量要求、壓力機性能參數等具體情況來確定加工工藝。
如圖11-9所示為小圓彎曲模。如圖11-9(a)所示為使用兩套簡單模具彎圓的方法,先將還料彎成U形,然后再將U形件彎成圓形。這種兩次彎曲操作方法效率較低,可將兩道工序合并,如圖11-9(b)、圖11-9(c)所示。其中圖11-9(b)為有側楔的一次彎曲模,上模下行時,芯棒3先將還料彎成U形,隨著上模繼續下行,側楔7便推動活動凹模8將U形彎成圓形;圖11-9(c)所示是另一種一次彎圓模,上模下行時,壓板2將滑塊6往下壓,滑塊帶動芯棒3先將坯料彎成U形,然后凸模1再將U形彎成圓形。如果工件圓形度或精度要求較高,可旋轉工件連沖幾次。彎曲后工件環套在芯棒3上,取下即可。

如圖11-10和圖11-11所示分別為三道工序彎曲大圓的方法及兩道工序彎曲大圓的方法。前者生產效率較低,但適用于加工還料厚度較大的工件;后者先將坯料預彎成三個120°的波浪形,然后再利用第二套模具彎成圓形,此方法操作簡單,但對各工序加工精度及模具要求較高。


4、其他形狀零件的彎曲模
除以上三種在金屬包裝容器中常用的彎曲模具之外,還有很多其他形狀件的彎曲模,如L形件彎曲模、Z形件彎曲模、較鏈件彎曲模及其他異形件彎曲模。由于這些彎曲件形狀、尺寸、精度要求及材料各不相同,難以有一個統一的彎曲方法,只能在實際生產中根據各自的工藝特點采取不同的彎曲方法。
三、拉深模
拉伸件的形狀及尺寸精度主要通過凸、凹模來控制的,因此,凸、凹模斷面形式的設計合理與否將直接影響拉伸過程中金屬材料的流動狀態,進而影響拉伸件質量。
1、拉深凸、凹模的結構
(1) 凸模的結構形式
如圖11-12所示為幾種常見的拉伸凸模結構形式,其中圖11-12(a)為最簡單的圓柱形,這種凸模結構簡單,制造成本較低,但是不利于工件脫模。為了解決這一弊端,可將凸模在高度方向上加工一定的錐度a[圖11-12(b)],一般圓筒形件的拉深凸模錐度a 可取2°~5°。中型和大型拉深件的加工通常需要多次拉深才能完成,其前幾道工序的拉深凸模一般可以做成帶有錐形側角的結構[圖11-12(c)],其轉角處為45°的斜面。為了避免工件在圓角處過分變薄甚至斷裂,通常需要在斜面和圓柱形連接處設置倒圓角。此外還應注意,此類凸模底部直徑小的大小應與下一次拉深時凸模的外徑相等。

即使采用了易脫模凹模結構,由于受模具擠壓及外部空氣壓力的作用,拉伸后的工件仍常常緊緊套在凸模上不易脫下,因此,通常需要在凸模上開設通氣孔以減小空氣壓力的影響[圖11-12(a)]。
(2) 凹模的結構形式
常見的拉深凹模結構是一個上邊緣帶圓角的圓柱孔,如圖11-13所示。圓角以下高度為h的直壁部分同拉深凸模配合,擠壓金屬還料產生滑動使之變形成為圓筒形件(或杯形件)。h值大小設置是否合理對拉伸件的質量影響極大,如果h過小,拉伸件金屬材料未完全脫離彈性變形區進入塑性變形,拉深過程結束后會出現較大回彈,從而導致拉深件高度上各部分的尺寸不能保持一致;而當h過大時,還料金屬在凹模內直壁部分滑動摩擦力增大,造成制件側壁過分變薄甚至拉斷。
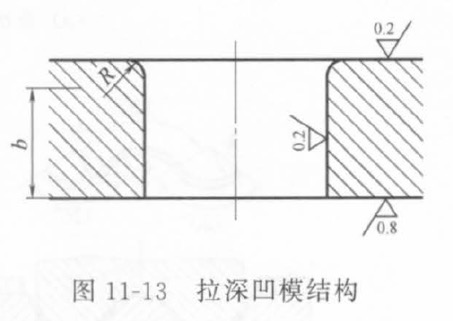
根據凹模是否配置壓邊圈,可將拉深凹模分為不帶壓邊圈的拉深凹模和帶壓邊圈的拉深凹模,如圖11-14和圖11-15所示。為了保證拉深坯料的正確定位,不帶壓邊圈的拉深凹模在口部通常做成臺肩結構,但此種結構形式的凹模不便于修模,因此帶壓邊圈的拉深凹模更為常用。
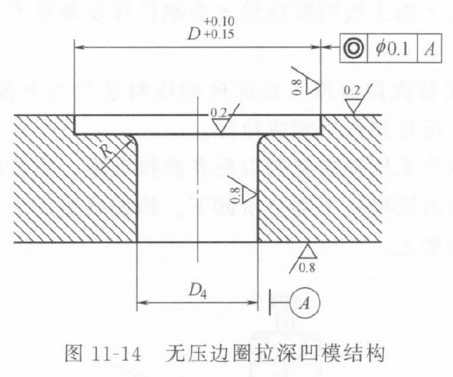
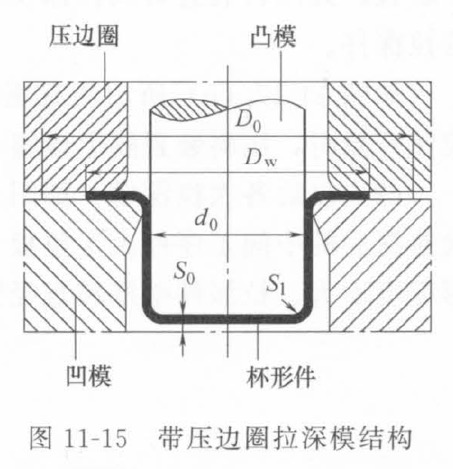
對于下出件拉深模,通常將凹模直壁部分的下端做成直角或銳角的形式,這樣在拉深過程終了時,拉伸件隨凸模上行時其口部會被凹模下端勾住,完成脫模,如圖11-16所示。如果此處設置為圓角或鈍角,拉伸件可能會隨凸模一起上行,無法順利完成脫模。
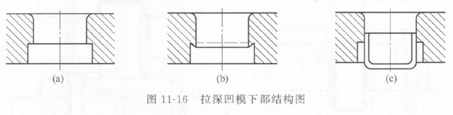
2、拉深模的典型結構
(1) 首次拉深模
如圖11-17(a)所示為無壓料裝置(如壓邊圈)的首次拉深模。此類拉深模可根據拉伸件性質決定是否設置卸件裝置:
①如果拉深結束后拉伸件回彈較小,拉深件緊套凸模,此時需要裝配卸件裝置,在凸模回程時,卸件裝置的底部會作用于拉伸件口部,完成卸件;
②如果制件拉深變形較小,拉深后有一定回彈量并因此引起拉深件口部張大,當凸模回程時,凹模下平面擋住拉深件口部而自然卸下拉深件,此時無需配備卸件裝置。無壓料裝置首次拉深模結構簡單,適用于加工板料厚度較大而制件深度要求不大的拉深件。

如圖11-17(b)所示為有壓料裝置的正裝式首次拉深模。拉深模的壓料裝置在上模,拉深開始時,壓料裝置隨上模座一起往下運動,壓住蚽料后完成拉深。
(2) 以后各次拉深模
如圖11-18(a)所示為無壓料裝置的以后各次拉深模,完成前次拉深后的中間工序件由定位板6定位,拉深后由凹模孔下部臺階卸下。該模具適用于變形程度不大、拉深件壁厚和直徑要求均勻的拉深加工。
如圖11-l8(b)所示為有壓料裝置倒裝式以后各次拉深模,壓料圈6兼具壓料、定位作用,前次拉深后的中間工序件套在壓料圈上進行定位。壓料圈的高度應大于前次工序件的高度,并根據前次工序件的內徑設置其外徑。拉深完的工件在回程時由壓料圈和推件塊分別頂出完成卸件。
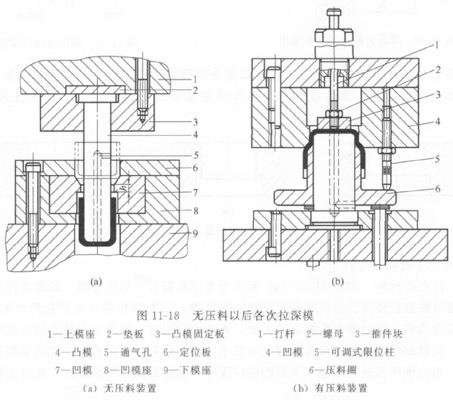
四、其他沖壓模具
在金屬包裝材料的生產制造過程中,除沖裁、彎曲、拉深這三大冷沖壓工藝外,其他冷加工方法也不可或缺,如翻邊、縮口、脹形、整形等。在這些加工方法中,模具也起到了重要的作用。
1、翻邊模具
根據翻邊工藝的不同,可將翻邊模具分為內孔翻邊模具和外緣翻邊模具。總體來看內孔翻邊模和拉深凸模有很多相似之處,也有壓邊和不壓邊、正裝和倒裝之分。同時,內孔翻邊模一般不需要設置模架。如圖11-19所示為幾種常見的圓孔翻邊凸模形狀及尺寸,其中圖11-19(a)~圖11-19(c)為較大孔的翻邊凸模,在這三種凸模中,拋物線形凸模最利于翻邊工藝的進行,球頭凸模次之,平底凸模最差。圖11-19(d)~圖11-19(f)所示的翻邊凸模端部帶有較長的引導部分,如圖11-19(d)所示凸模用于圓孔直徑大于10mm的翻邊,如圖11-19(e)所示凸模用于圓孔直徑小于10mm的翻邊,如圖11-19(f)所示凸模用于無預孔的不精確翻邊。
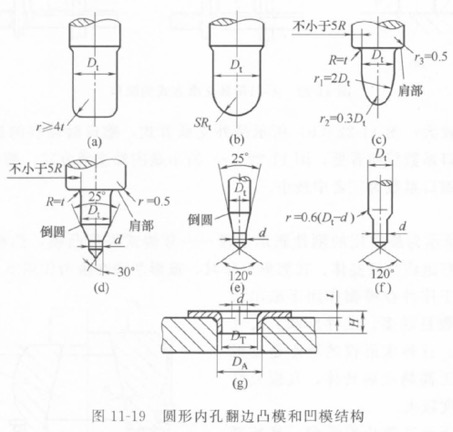
如圖11-20所示為內孔、外緣翻邊復合模結構,其中凸凹模安裝在下模座,既起到內孔翻邊凹模的作用,也起外緣翻邊凸模的作用。
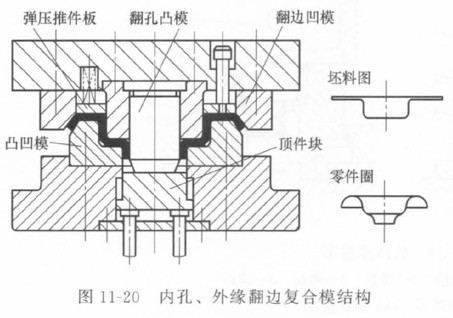
2、縮口模具
如圖11-21所示為縮口凹模結構圖,其基本結構通常為一個根據縮口件形狀要求設置的錐形孔。根據縮口時模具對蚽料壁部是否有支撐作用可將縮口方式分為三類,如圖11-22所示。圖11-22(a)所示為無支承方式,縮口過程中還料的剛性差,易失穩,因而許可的縮口系數較大;圖11-22(b)所示是外支承方式,縮口時還料的抗失穩能力較前者高,許可的縮口系數較前者低;圖11-22(c)所示是內外支承方式,縮口時還料的穩定性最好,許可的縮口系數為三者中最小。


3、脹形模具
如圖11-23所示為最常用的剛性脹形凸模分瓣式脹形凸模,凸模被分成多個模瓣,所有模瓣一起組成凸模整體。在脹形工作時,錐形芯塊在推力作用下上行,將分瓣凸模頂開,從而使工序件在模瓣作用下脹出所需形狀。模瓣的數目越多,工件形狀、尺寸和精度控制越好。這種脹形模的缺點是變形不均勻,難以加工高精度旋轉體,且模具結構復雜,制造難度較大。
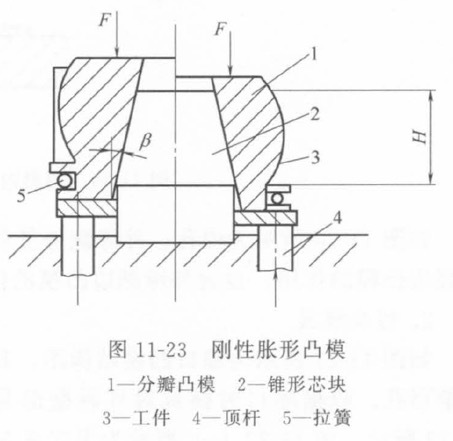
如圖11-24所示是軟凸模脹形,其原理是利用橡膠、液體、氣體和鋼丸等代替剛性凸模,與工件直接接觸完成脹形。這種脹形方法所加工的還料變形均勻,且不受零件形狀的復雜程度限制,因此在生產中被廣泛使用。
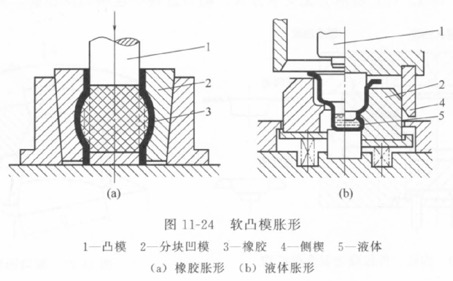
4、整形模具
由于工藝方法、模具精度、金屬加工后回彈現象等眾多因素的影響,冷沖壓制件在尺寸精度或形狀細節上離要求標準仍存在細微差距,這時就需要對這些制件進行整形。由于整型后制件的精度要求比較高,因而對模具的精度要求也是較高。
①校平模具。根據校平件的表面形狀,可將校平模具分為平板校平模具和齒面校平模具,如圖11-25所示。進行校平整形時,將工件置于上模板和下模板制件,然后在兩模板之間施加一定壓力,并根據要求保待一定時間,使工件完成定型。
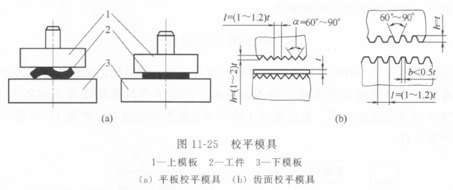
②彎曲件整形模具。彎曲件的整形分為壓校和墩校,如圖11-26所示。

③拉深件整形模具。根據拉伸件是否有凸緣,相應的將拉伸件整形模具分為無凸緣拉伸件整形模具和帶凸緣拉伸件整形模具,它們的基本結構和拉深模具基本一樣,都由凸模凹模組成,區別是前者未配置壓件裝置,而后者在整形過程中需要固定凸緣,因此配備了壓件裝置,如圖11-27所示。
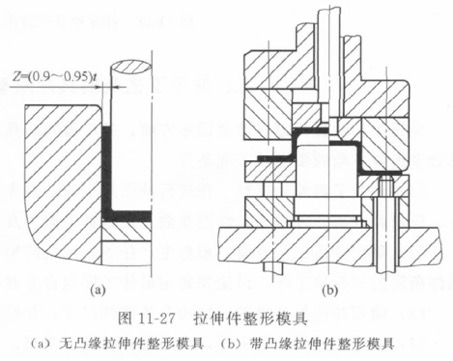
需要注意的是,帶凸緣的拉延件在整形過程中需要拉伸件多部位的參與,包括需凸緣平面、側壁、底平面和圓角等,有些區域在整形時需要從鄰近區域得到補充材料。
|