鋼卷板及鍍鋅質量異議缺陷圖譜詳解(2)
文/京唐

表面類缺陷(續)
8、鋅渣

【定義與特征】
在熱鍍鋅板面上分布有類似米粒的小顆粒或塊狀的不規則顆粒稱為"鋅渣"。有以下三種情況:
①粗渣粒是指嵌在金屬鍍層中,尺寸為0.5mm~2.0mm 的渣粒;
②細渣粒是指在鍍層中呈條狀或聚集分布的直徑小于0.5mm 的細小渣粒;
③渣斑是指嵌于金屬鍍層中,尺寸為2.0mm~10mm 的渣粒。
【產生原因】
①底渣、懸浮渣和浮面渣沉積在鋼帶上形成渣粒;
②鋅液溫度波動、撈渣不凈、沉沒輥使用超期、鋁含量超標等。
【預防與糾正】
①控制鋅液溫度在460°C ±5°C, 提高鋅液溫度控制穩定性, 減少鋅渣的產生;
②當發現鋅渣缺陷較多時,增加撈渣頻次,及時撈取鋅鍋中的浮渣,同時適當降低刀高度(根據鋼帶規格在50mm~450mm 之間調整),生產高表面要求鍍鋅板時,要使用氮氣管進行吹渣處理;
③在沉沒輥系裝配前,保證沉沒輥修復質量,尤其是沉沒輥溝槽和表面粗糙度和光度要滿足工藝要求,沉沒輥按周期及時更換;
④鋅液中鋁含量穩定控制在0. 18%~0. 22% 。
【鑒別與判定】
肉眼檢查。粗渣粒和渣斑較重時有手感,呈點狀、塊狀,以及條狀突出于鍍鋅板表面。高表面要求鍍鋅板不允許出現鋅渣缺陷。
9、鋅灰

【定義與特征】
特征形貌為白色點狀,針尖大小,或呈細長彗星片狀(托尾巴)的缺陷稱為"鋅灰"。
【產生原因】
爐鼻子內附集的鋅灰,在鋼帶運行過程中由于震動掉落到鋼帶表面。
【預防與糾正】
①定期更換鋅鼻頭和鋅泵;
②增加爐鼻子加濕裝置和除鋅灰裝置;
③提高沉沒輥穩定性,降低液面波動。
【鑒別與判定】
肉眼檢查。與其它鋅渣比較,程度較輕;手感不明顯。按標準判定。
10、鍍層云紋

【定義與特征】
鍍層厚度的水波狀變動稱為"鍍層云紋"。分為以下三種情況:
①停車鍍層云紋是波紋狀波動較大呈海浪狀,缺陷分布無規律,手感極嚴重,局部露鐵缺陷;
②減速鍍層云紋是波紋狀波動較大呈水紋狀,有—定規律,手感較嚴重;
③鋅流波痕鍍層云紋是波紋狀波動較小呈魚鱗狀,有規律,無手感。
【產生原因】
①停車鍍層云紋:因機組停車,導致鋼帶入鋅鍋溫度、鋼帶速度不能達到工藝要求產生;
②減速鍍層云紋:鋼帶運行速度過低,鋼帶上的鋅液因重力原因下流,產生減速鍍層云紋;
③鋅流波痕鍍層云紋:機組生產速度低、鍍層厚鋼帶厚度厚、鋼帶入鋅鍋溫度和鋅液溫度低、鋼帶表面粗糙度低等產生。
【預防與糾正】
①控制鋼帶進入鋅鍋溫度及鋅液溫度滿足工藝要求,在較長時間的停車后重新起車,升溫時,盡量采取快速升溫的方法以及減小退火爐噴冷段的輸出;
②對于不同規格的鋼帶,速度避免減小到相應規格鋼帶運行的最小速度,在有突發問題需要降速時,采取小幅多次的方法,避免一次降速20m/min 以上;
③ 生產厚料厚鍍層鍍鋅板時,盡量用最大生產速度進行生產,同時使氣刀刀唇距離盡可能減少,降低氣刀高度等。
【鑒別與判定】
肉眼檢查。不易與其它缺陷混淆,一般是在停車、停車后起車或是急降速的時候出現。鍍鋅板不允許有鍍層云紋。
11、沉沒輥印
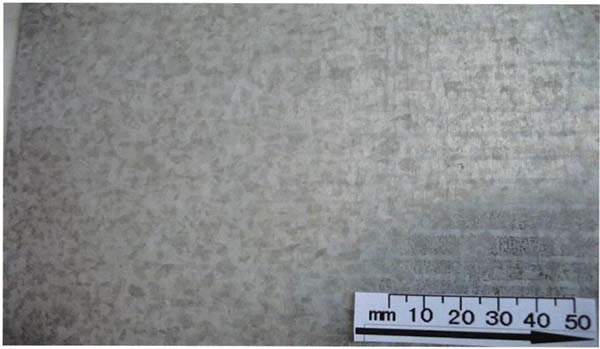
【定義與特征】
沉沒輥溝槽形狀印到鋼帶表面,形成沿軋制方向的縱向(斜向)條紋稱“沉沒輥印"。沉沒輥印通常是與沉沒輥溝槽有相同形狀的印痕。
【產生原因】
①沉沒輥表面有劃傷或硌坑以及溝槽的修磨質量或倒角不滿足使用要求;
②沉沒輥軸頭與軸套裝配間隙過大,導致沉沒輥在運行時震動大;
③鋅鍋張力調整不當;
④鋅鍋內鋁含量低,自由渣較多,粘浮在溝槽內。沉沒棍印是由鋅鍋沉沒輥上條紋狀沉積物劃傷冷軋鋼帶表面引起的,有時還與合金層生長中斷有關。
【預防與糾正】
①沉沒輥棍面及溝槽不允許有有手感的劃傷、裝配時做好各項防護,避免輥面人為損傷;
②沉沒輥裝配時,保證安裝精度;
③出現沉沒輥印缺陷時,每次10 %范圍內調整鋅鍋張力,并觀察缺陷的程度,反復調整;在剛換完沉沒輥的初期,不排產厚料生產;
④出現沉沒輥印,同時發現鋅鍋內鋁含量偏下限時,在鋅鍋四角添加高鋁錠,適當提高鋁含量。
【鑒別與判定】
肉眼檢查。不易與其它缺陷混淆。不允許存在。
12、鋅花不均

【定義與特征】
鋼板表面的鋅花尺寸局部過大或過小,不滿足正常要求,稱為"鋅花不均"。呈塊狀分布或者條狀分布,鋼帶表面局部或整卷出現。
【產生原因】
鋅花形成速度不同。
【預防與糾正】
①發現鋅花不均或鋅花小缺陷時,適當降低生產速度,保證鋼帶加熱和冷卻均勻;
②提高堿液濃度,加大刷輥插入量,增加排放量和次數,提高清洗效果。適當提高退火爐溫度,增強退火爐的清潔能力;
③控制鋅鍋內銻含量滿足工藝要求,鋅錠的添加采取少量多次的原則。
【鑒別與判定】肉眼檢查。表現通常為部分鋅花較小或是基本看不到明顯鋅花,周圍鋅花正常,鋼帶的帶頭與帶尾出現較多,不易與其它缺陷混淆。在帶頭帶尾允許少量存在。
13、邊部斜紋

【定義與特征】
鋼帶在冷卻過程中,在邊部形成的羽毛狀斜紋稱為"邊部斜紋”。
【產生原因】
鋅層冷卻不足,雖表層鋅層冷卻,但內部鋅液未充分冷卻,未冷卻部分鋅液有流動趨勢產生斜紋。
【預防與糾正】
①提高氣刀與鋅液面的高度,拉大氣刀與鋼帶距離,增加氣刀壓力;②降低鋅液溫度,降低機組生產速度。
【鑒別與判定】
肉眼檢查。不易與其它缺陷混淆。按標準判定。
14、邊部增厚

【產生原因】
①鋼帶邊部有毛刺,在通過氣刀時帶起的鋅液使刀唇堵塞;
②鋅液溫度偏低;
③邊部擋板間隙偏大,氣刀的角度調整不合適,造成對吹,形成紊流而產生;
④鋼帶在低速下形成邊部增厚的主要原因是邊部熱量損失嚴重,使鋅液粘度增大,邊部刮去的鋅液比中部少。
【預防與糾正】
①嚴格控制鋼帶邊部質量,拒絕帶毛刺、破邊的鋼卷上線生產;
②嚴格控制鋅液溫度;
③及時檢查邊部擋板間隙,合理調整氣刀角度;
④低速運行的情況下,加大吹氣量,同時適當降低氣刀高度,在鋅液冷卻前將多余的部分吹掉。
【鑒別與判定】
較嚴重時可用肉眼檢查;較輕時應用手觸摸進行判定;不明顯時,應用千分尺測量厚度進行比較。邊部增厚不允許存在。
15、麻點
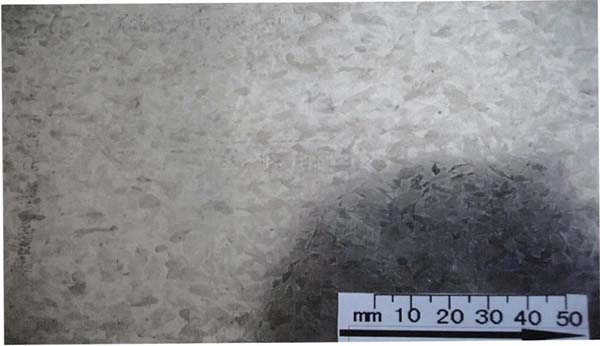
【定義與特征】
鋼帶在鍍鋅后形成斑點狀的局部凸起或凹坑稱為“麻點”。一般呈點狀,在鋼帶表面不規則分布,帶有輕微顏色。
【產生原因】
①后冷冷卻程度不夠,在頂輥處被硌傷,或冷卻不均;
②鍍鋅前基板銹蝕或污物未消除。
【預防與糾正】
①控制鋼帶后冷段風機的輸出,保證水平頂棍前溫度,保證水平頂棍刮刀的正常投入使用;
②發現原料銹蝕或污物時,適當增加刷棍插入量,提高退火爐內氫氣含量。
【鑒別與判定】
肉眼檢查。按標準判定。
(資料來源:京唐金屬制品有限公司、歐冶知鋼技術資料精選、首鋼技術研究院、鞍鋼集團鋼鐵研究院)