鍍鋅鋼桶用鋼板的開發與鍍鋅工藝控制
文/馬孝娟
摘要: 文章介紹了以冷軋低碳鋼為原料,通過化學成分、退火工藝等方面工藝設計試制生產鍍鋅油桶用鋼。試制結果表明試制生產的鍍鋅油桶用鋼力學性能穩定,鋼卷表面質量優良,很好地滿足了用戶使用要求。
關鍵詞: 鍍鋅;油桶用鋼;工藝;連續退火
1 前言
熱鍍鋅鋼板由于鋅在鋅層表面形成耐腐蝕性良好的薄膜不僅保護了鋅層,而且對基板也起到了保護作用,因此鍍鋅板被廣泛地應用于建筑業、容器制造及包裝業等行業。熱鍍鋅板作為制作油桶的原料,由于制桶工藝涉及到卷圓、桶身翻邊漲筋、W筋波紋滾壓成型等變形加工的工藝,制桶過程中材料存在一般加工用的變形。因此要求鍍鋅板既能夠對鋼卷有防護作用也要滿足制桶加工變形等的要求。八鋼公司具備完整的開發鍍鋅油桶鋼的生產鏈,通過原料成分設計,工藝參數調整控制,并且為保證產品性能對鍍鋅的連續退火和拉矯工藝作為關鍵工藝進行了控制,開發并試制了制油桶用熱鍍鋅鋼板。
2 鍍鋅產品工藝流程及原料化學成分設計
八鋼采用寶鋼標準Q/BQB420- 2018 中的牌號,因此采用S220GD+Z來試制油桶用鍍鋅板。
鍍鋅產品工藝流程:鐵水脫硫處理—120t 轉爐—LF精煉—板坯連鑄—加熱—1750mm軋制—層流冷卻—冷軋酸洗軋機—熱鍍鋅—分卷—包裝。整個流程要經過煉鋼、熱軋、冷軋、熱鍍鋅屬于熱鍍鋅鋼板,經過合理的設計可用于制桶。
冷軋一般加工用鋼采用冷軋低碳鋼成分,其中碳(C)含量及其在鋼中的存在形式決定著鋼的強度和其它性能,高的C含量會造成冷軋后產品的滲碳體級別升高,使強度增加,塑性下降。其中屈服強度是影響材料沖壓性能的一個重要力學性能指標,屈服強度表征材料拉伸時塑性變形起始時的抗力大小,屈服強度小則永久變形開始時抗力越小,材料越容易加工。伸長率是材料的塑性指標,伸長率高表明材料延展性更好,因此在標準要求力學性能基礎上對屈服強度進行了更進一步規定:220~320MPa(標準≥220MPa)。
鋼中的氮來自爐料,同時,在冶煉時鋼液也從爐氣中吸收氮。氮對低碳鋼的性能不利,它將惡化鋼板的彎曲、深沖性能,還會因變形不均勻而在沖壓件表面出現皺紋,解決方法是往鋼中加入足夠數量的鋁,采用適當的工藝使鋁和氮結合成AlN,可以減弱甚至消除氮引起的應變時效現象。因此采用低碳鋼的化學成分,并且控制N含量。化學成分要求見表1。

3 煉鋼、軋鋼關鍵工藝控制
3.1 煉鋼工藝
對于加工用途鋼種煉鋼采取擋渣、LF 精煉、控制拉速等措施控制鋼中非金屬夾雜物的含量。
轉爐控制好終點[C]含量,根據碳含量加入脫氧劑,維護好出鋼口,出鋼時間≥3.5 分鐘。出鋼擋渣,控制鋼包渣層厚度,要求出鋼回磷不大于0.003%。
LF處理:提溫、調整成分、脫硫、脫氣、去夾雜。
連鑄采用全程氬氣保護澆注,采用無碳保護渣和無碳鋼包覆蓋劑;中包安裝擋墻,連鑄最大拉速≤1.6m/min。
3.2 熱軋工藝
對于生產冷軋低碳鋼薄板嚴格控制熱軋工藝非常關鍵。研究結果[4]表明,采用連退工藝生產的冷軋低碳鋼薄板在熱軋時采用中高溫卷取,采用低溫卷取的帶鋼抗拉強度明顯升高延伸下降。中高溫卷取目的是使熱軋卷的鐵素體晶粒長大, 碳化物聚集而粗大,氮化鋁進一步析出和長大。這樣的熱軋工藝和連退工藝相配合, 有利于鐵素體晶粒的長大,對沖壓用鋼力學性能有利,熱軋溫度要求見表2。

熱軋供冷軋原料金相組織為:鐵素體+ 珠光體,晶粒度8級(見圖1)。
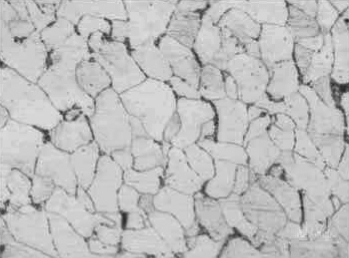
圖1 熱軋原料卷金相組織
3.3 冷軋工藝
冷軋工藝中影響最終性能的主要因素是冷軋壓下率。冷軋壓下率的提高不僅可以降低退火的再結晶溫度,還有利于產生有益的形變織構。對于低碳鋁鎮靜鋼而言,在同一熱軋卷取溫度下,鋼板的平均塑性應變比r 值隨著冷軋壓下率的增加而提高,考慮到八鋼冷軋軋機能力,S220GD+Z試制的冷軋壓下率設定為60%~73%。
軋機是保證鍍鋅原料清潔的重要工序,鍍鋅原料板面的清潔程度主要取決于冷連軋機組乳化液的干凈程度,其次與空氣中的灰塵量也有一定關系。因此規定在冷軋5#軋機出口吹掃壓力不得小于5kg,并且要按照規定在軋機出口測板面反射率。
4 鍍鋅工藝的關鍵控制要點
4.1 鍍鋅機組工藝流程
八鋼熱鍍鋅生產線可生產鍍鋅板:厚度0.25~1.6mm;寬度720~1250mm;最大卷重21t;鋼卷外徑最大1900mm;鋼卷內徑508/610mm;鋅層重量:雙面鍍層(60~275g/m2兩面);正常鋅花。
八鋼熱鍍鋅生產工藝流程:上卷—開卷—切頭、切尾—焊接—堿洗—堿液刷洗—電解清洗—刷洗—熱水漂洗—熱風干燥—入口活套—連續退火—鍍鋅—氣刀吹掃—鍍后風冷—淬水—拉伸矯直—鈍化處理—出口活套—涂油—剪切—卷取—卸卷—稱重—包裝。控制好鍍鋅產線中的連續退火和拉伸拉矯工序的工藝參數可以生產出滿足力學性能要求的熱鍍鋅產品。
4.2 連續退火工藝要求
冷軋過程中,由于晶體中原子產生刃型位錯運動,因此晶格可沿一定的滑移面和滑移方向(即軋制方向)進行雙滑移或多系滑移,從而表現除了鋼板在軋制力作用下的塑性形變。這樣經冷軋后,發生了晶粒延長、扭曲或破碎(見圖2)。位錯增加,形變抗力增大,經過冷軋后薄板的抗拉強度可達800~900MPa,必須經過再結晶退火以恢復材料的加工成形性能。
八鋼熱鍍鋅是通過連退機組進行再結晶退火,對于已冷軋硬化的鋼板,在退火時加熱速度越快,即在不同溫度下停留的時間較短,則再結晶溫度越高,否則,再結晶溫度越低。制定了機組速度要求:0.6~1.0mm,30~60mpm;1.0~1.6mm,20~40mpm。連退溫度要求見表3。

圖2 冷軋后組織
鋅鍋溫度的控制要平穩,不可急速升溫和降溫,防止鋅粒缺陷的產生。
4.3 鍍鋅拉矯工藝控制
拉矯工藝對鋼板的成型性能也起到關鍵的作用,不僅能清除板面存在的浪形、瓢曲、輕度的鐮刀彎和改善表面的平直度,還能消除屈服平臺,改善材料的各向異性。理論和實踐都證明了有屈服平臺的帶鋼在沖壓加工時會出現滑移線,彎曲成圓時有橫向折彎,從而使加工件表面不良,因此拉矯對不同用途的帶鋼要采用不同的延伸率,以達到提高產品性能的目的。由于鍍鋅線無光整機,對于低碳沖壓用鋼而言,要求屈服極限很低且消除屈服平臺,拉矯延伸率控制在0.8% ~1.2%。
5 試制的制油桶用熱鍍鋅鋼板性能檢測
5.1 力學性能
檢測試制S220GD+Z的屈服強度、抗拉強度、延伸率三項力學性能值分布見圖3,屈服強度值分布在250- 320MPa,抗拉強度值分布在320~380 MPa,延伸率值分布在25~38%,力學性符合標準要求(見表4),可滿足用戶制桶的加工需求。

圖3 S220GD+Z力學性能過程能力分析
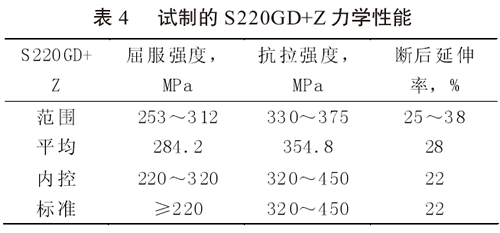
5.2 金相組織
S220GD+Z鍍鋅產品金相組織為:鐵素體+ 珠光體+球粒狀滲碳體,晶粒度9級(見圖4)。組織中拉伸變形的晶粒已被再結晶的等軸鐵素體晶粒代替,此時珠光體趨于球粒化。隨著退火溫度升高,形成一些位向與變形晶粒不同,內部缺陷較少的等軸小晶粒,這些小晶粒不斷向變形金屬中擴展,冷變形的拉長晶粒完全消失整個再結晶完成。
再結晶退火消除了冷軋變形造成的內應力,加工硬化現象被消除,這樣材料的強度和硬度顯著下降,塑性和韌性也會大大提高。
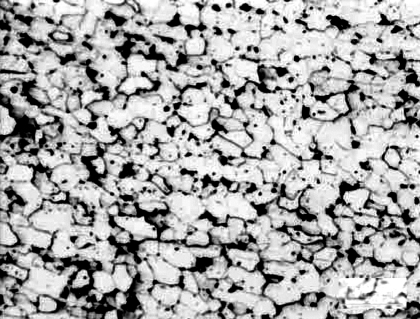
圖4 鍍鋅成品金相組織
5.3 用戶試用情況
用戶的制桶工藝介紹:
(1)桶身。鋼卷開卷下料—卷圓—通身電焊—通身縫焊—通身翻邊漲筋—縫焊試漏—W筋波紋滾壓成型;
(2)桶蓋。桶頂蓋沖壓成型—預卷—注膠—桶頂沖注入孔及鉚合—桶頂沖透氣孔及鉚合。
桶身與桶蓋加工完后工序:脫脂磷化水洗—烘干—卷邊封口—試漏—試漏烘干—噴粉、噴漆—噴涂烘干—堆碼—出廠檢驗—出廠。
用戶反饋,八鋼生產的S220GD+Z鍍鋅板在漲筋、沖孔等制桶過程中變形較大的加工工序中未出現開裂、鋅層剝落等缺陷,試制的S220GD+Z鍍鋅板滿足制桶用途。
通過用戶試用,制桶用鍍鋅產品S220GD+Z化學成分、工藝參數設計合理,制桶用S220GD+Z經過開發與試制,已投入批量生產。
6 結束語
鍍鋅板由于鋅層的隔絕作用減緩了外界環境對桶的腐蝕,很大程度上延長了桶的使用時間,鍍鋅板在制桶業中被廣泛使用。為生產滿足制桶用鍍鋅板,選擇低碳鋁鎮靜鋼的化學成分為原料,采用適當的熱軋、冷軋工藝參數,通過鍍鋅線上的連退工藝設計,最終鍍鋅產品力學性能符合標準要求,并滿足制桶加工用途。